A Deposição Física de Vapor (PVD) e a Deposição Química de Vapor (CVD) são tecnologias avançadas de revestimento utilizadas para melhorar as propriedades da superfície dos materiais, como a dureza, a resistência ao desgaste e a resistência à corrosão.A PVD envolve a vaporização de um material sólido no vácuo e a sua deposição num substrato, enquanto a CVD utiliza reacções químicas de precursores gasosos para formar um revestimento.Ambos os processos têm etapas, vantagens e aplicações distintas.O PVD é mais rápido e funciona a temperaturas mais baixas, o que o torna adequado para uma gama mais vasta de materiais, enquanto o CVD produz revestimentos mais densos e uniformes, mas requer temperaturas mais elevadas e tempos de processamento mais longos.
Pontos-chave explicados:
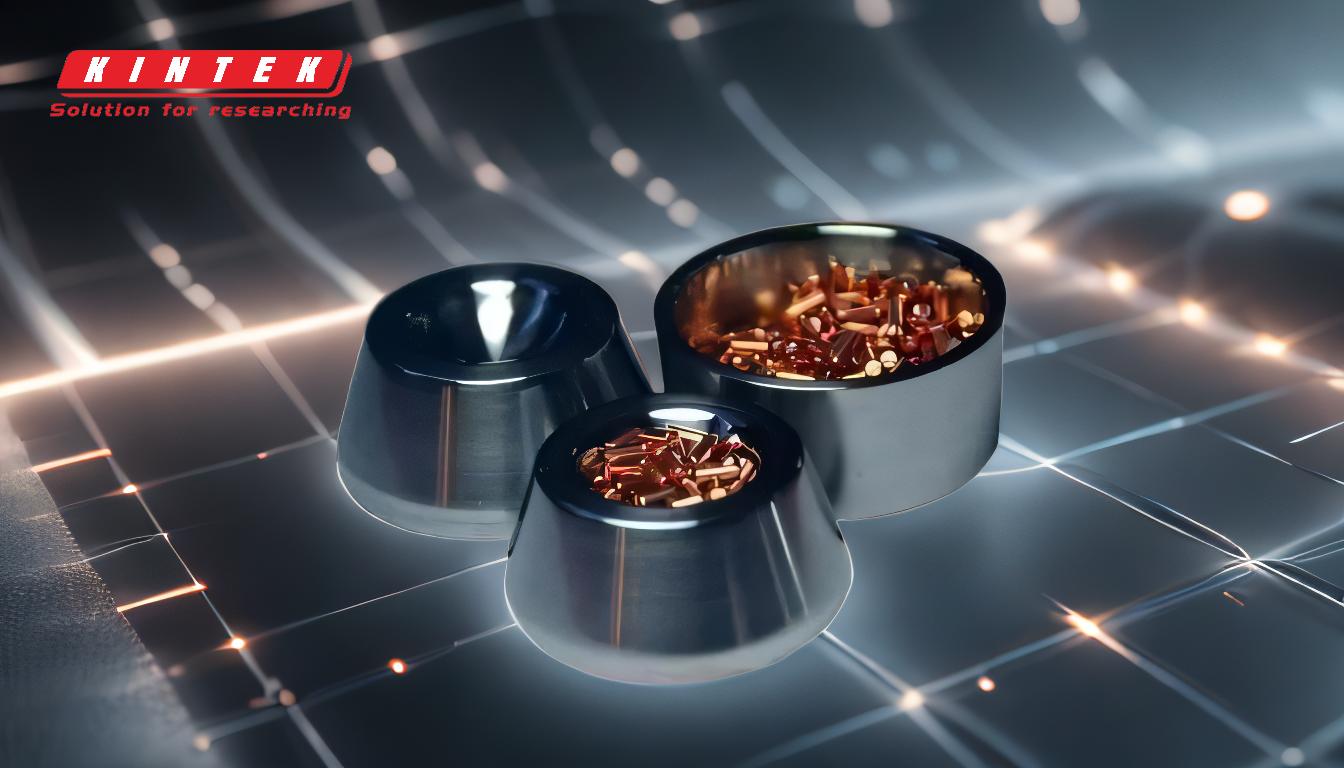
-
Visão geral dos processos de revestimento PVD e CVD:
- PVD:Consiste na vaporização de um material sólido no vácuo e na sua deposição num substrato.É um processo físico que funciona a temperaturas mais baixas (cerca de 500 °C) e é adequado para metais, ligas e cerâmicas.
- CVD:Utiliza reacções químicas de precursores gasosos a altas temperaturas (800~1000 °C) para depositar um revestimento.Normalmente, limita-se a cerâmicas e polímeros e produz revestimentos mais espessos, mais densos e mais uniformes.
-
Etapas do processo de revestimento PVD:
- Passo 1: Limpeza do substrato:O substrato é limpo para remover os contaminantes, garantindo uma melhor aderência do revestimento.
- Etapa 2: Pré-tratamento:O substrato é submetido a um pré-tratamento para melhorar a aderência do revestimento, envolvendo frequentemente a ativação da superfície ou a gravação.
- Etapa 3: Revestimento:O material alvo é vaporizado utilizando técnicas como o feixe de electrões, o bombardeamento de iões ou o arco catódico.O material vaporizado é então transportado para o substrato e depositado como uma película fina.
- Etapa 4: Controlo de qualidade:O substrato revestido é inspeccionado para garantir que o revestimento cumpre as normas especificadas, tais como a espessura, a uniformidade e a aderência.
- Etapa 5: Acabamento:Podem ser aplicados tratamentos adicionais para melhorar o aspeto ou o desempenho do revestimento, como o polimento ou o recozimento.
-
Etapas do processo de revestimento CVD:
- Etapa 1: Introdução do Precursor:Os precursores gasosos são introduzidos na câmara de reação.
- Etapa 2: Reação química:Os precursores reagem a altas temperaturas (800~1000 °C) para formar o material de revestimento desejado.
- Etapa 3: Deposição:Os produtos da reação são depositados no substrato, formando um revestimento denso e uniforme.
- Etapa 4: Pós-tratamento:O substrato revestido pode ser submetido a tratamentos adicionais, como o recozimento ou o acabamento da superfície, para melhorar as suas propriedades.
-
Principais diferenças entre PVD e CVD:
- Temperatura:A PVD funciona a temperaturas mais baixas (cerca de 500 °C), enquanto a CVD requer temperaturas elevadas (800~1000 °C).
- Espessura do revestimento:A PVD produz revestimentos mais finos (3~5μm), enquanto a CVD resulta em revestimentos mais espessos (10~20μm).
- Densidade e uniformidade do revestimento:Os revestimentos CVD são mais densos e mais uniformes em comparação com os revestimentos PVD.
- Compatibilidade de materiais:O PVD pode depositar uma gama mais vasta de materiais, incluindo metais, ligas e cerâmicas, enquanto o CVD está normalmente limitado a cerâmicas e polímeros.
- Tempo de processamento:A PVD é mais rápida, o que a torna adequada para aplicações que exigem tempos de execução rápidos, enquanto a CVD demora mais tempo devido às reacções químicas envolvidas.
-
Aplicações de PVD e CVD:
- PVD:Normalmente utilizado em aplicações que exigem uma elevada resistência ao desgaste, tais como ferramentas de corte, revestimentos decorativos e componentes aeroespaciais.Também é adequado para processos de corte interrompido, como a fresagem.
- CVD:Ideal para aplicações que requerem revestimentos espessos, densos e uniformes, como o fabrico de semicondutores, revestimentos resistentes ao desgaste para processos de corte contínuo, como o torneamento, e aplicações a altas temperaturas.
-
Vantagens e limitações:
- PVD Vantagens:Processamento mais rápido, temperaturas de funcionamento mais baixas e compatibilidade com uma vasta gama de materiais.
- Limitações da PVD:Revestimentos menos densos e menos uniformes em comparação com a CVD.
- Vantagens da CVD:Revestimentos mais densos e mais uniformes, adequados para aplicações a altas temperaturas.
- Limitações da CVD:Temperaturas de processamento mais elevadas, tempos de processamento mais longos e compatibilidade de materiais limitada.
Ao compreender os passos detalhados e as diferenças entre os processos de revestimento PVD e CVD, os compradores de equipamentos e consumíveis podem tomar decisões informadas com base nos requisitos específicos das suas aplicações, tais como as propriedades de revestimento pretendidas, a compatibilidade de materiais e as restrições de processamento.
Tabela de resumo:
Aspeto | PVD | CVD |
---|---|---|
Temperatura | Baixa (cerca de 500 °C) | Superior (800~1000 °C) |
Espessura do revestimento | Mais fino (3~5μm) | Mais espesso (10~20μm) |
Densidade do revestimento | Menos denso | Mais denso e mais uniforme |
Compatibilidade de materiais | Metais, ligas, cerâmicas | Cerâmica, polímeros |
Tempo de processamento | Mais rápido | Mais longas |
Aplicações | Ferramentas de corte, revestimentos decorativos, componentes aeroespaciais | Fabrico de semicondutores, revestimentos resistentes ao desgaste, aplicações a altas temperaturas |
Precisa de ajuda para escolher o processo de revestimento correto para a sua aplicação? Contacte os nossos especialistas hoje mesmo !