A pulverização catódica é um processo de fabrico versátil e amplamente utilizado, no qual os átomos são ejectados de um material alvo sólido devido ao bombardeamento por iões energéticos, normalmente provenientes de um plasma.Estes átomos ejectados depositam-se então num substrato, formando uma película fina.Este processo é um tipo de deposição física de vapor (PVD) e é valorizado pela sua capacidade de criar revestimentos uniformes e de alta qualidade numa variedade de materiais, incluindo superfícies tridimensionais complexas e sensíveis ao calor.A pulverização catódica é essencial em indústrias como a dos semicondutores, aeroespacial, optoelectrónica e revestimentos decorativos, permitindo a produção de materiais e dispositivos avançados com propriedades precisas.
Pontos-chave explicados:
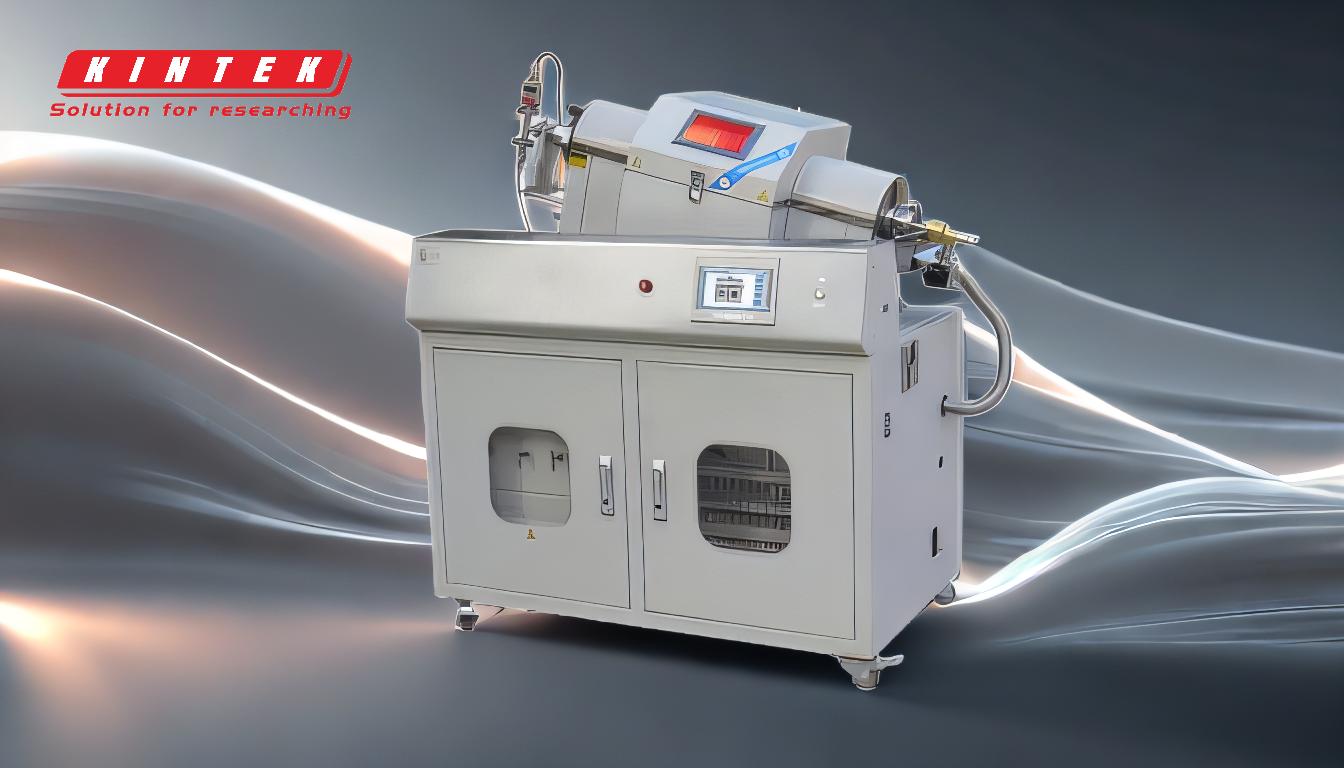
-
O que é Sputtering?
- A pulverização catódica é um processo de deposição física de vapor (PVD) em que os átomos são ejectados de um material alvo sólido quando bombardeados por iões energéticos de um plasma.Estes átomos ejectados viajam através de uma câmara de vácuo e depositam-se num substrato, formando uma película fina.
- É um processo de \"linha de visão\", o que significa que o material alvo e o substrato devem ser posicionados adequadamente para um revestimento eficaz.
-
Como funciona a pulverização catódica
- É utilizado um plasma para gerar iões, normalmente a partir de um gás inerte como o árgon, que são acelerados em direção ao material alvo.
- Quando os iões colidem com o alvo, deslocam átomos da sua superfície se a energia do ião for suficiente (normalmente 4 vezes a energia de ligação do material alvo, cerca de 5 eV).
- Os átomos pulverizados viajam então através da câmara de vácuo e depositam-se no substrato, formando uma película fina.
-
Aplicações da pulverização catódica
- Indústria de semicondutores: A pulverização catódica é utilizada para depositar películas finas para a criação de dispositivos electrónicos, como transístores e circuitos integrados.
- Aeroespacial e Defesa: É utilizado para aplicar revestimentos especializados, tais como películas de gadolínio para radiografia de neutrões.
- Optoelectrónica: A pulverização catódica é utilizada para criar revestimentos condutores transparentes para ecrãs e células solares.
- Revestimentos decorativos: É utilizado para aplicar acabamentos duradouros e esteticamente agradáveis em produtos de consumo.
- Proteção contra corrosão: A pulverização catódica pode criar filmes impermeáveis a gases para proteger materiais propensos à corrosão.
- Dispositivos médicos: É utilizado para produzir pilhas dieléctricas para isolar eletricamente instrumentos cirúrgicos.
-
Vantagens do Sputtering
- Versatilidade: A pulverização catódica pode depositar uma ampla gama de materiais, incluindo metais, ligas e isolantes.
- Revestimentos uniformes: Produz películas finas altamente uniformes e densas, mesmo em superfícies tridimensionais complexas.
- Baixa temperatura: O processo é adequado para materiais sensíveis ao calor, tais como amostras biológicas, uma vez que os átomos pulverizados têm temperaturas muito baixas.
- Materiais com alto ponto de fusão: A pulverização catódica é eficaz para materiais com pontos de fusão extremamente elevados, como o carbono e o silício.
-
Desafios e considerações
- Requisitos de vácuo: A pulverização catódica requer um ambiente de vácuo controlado, que pode ser caro e de manutenção complexa.
- Limitação da linha de visão: O processo é limitado pela necessidade de uma linha de visão direta entre o alvo e o substrato.
- Materiais isolantes: Os alvos isolantes requerem uma fonte de energia RF, o que aumenta a complexidade do processo.
-
Importância histórica e moderna
- A pulverização catódica tem sido utilizada desde o início do século XIX e continua a ser um método maduro e fiável para a deposição de películas finas.
- Desempenha um papel fundamental no fabrico moderno, permitindo a produção de materiais e dispositivos avançados, tais como revestimentos reflectores de alta qualidade para espelhos, dispositivos informáticos semicondutores e materiais de embalagem como sacos de batatas fritas.
Em resumo, a pulverização catódica é uma tecnologia fundamental no fabrico moderno, oferecendo uma deposição precisa e versátil de películas finas para uma vasta gama de aplicações.A sua capacidade de lidar com geometrias complexas, materiais sensíveis ao calor e revestimentos de alto desempenho torna-a indispensável em indústrias que vão desde a eletrónica à aeroespacial e outras.
Tabela de resumo:
Aspeto | Detalhes |
---|---|
Definição | Processo de deposição física de vapor (PVD) que ejecta átomos de um material alvo. |
Processo | Os iões gerados pelo plasma bombardeiam o alvo, ejectando átomos para um substrato. |
Aplicações | Semicondutores, aeroespacial, optoelectrónica, revestimentos decorativos e muito mais. |
Vantagens | Versátil, revestimentos uniformes, baixa temperatura, materiais com elevado ponto de fusão. |
Desafios | Requer vácuo, limitação da linha de visão, complexidade com isoladores. |
Descubra como a pulverização catódica pode revolucionar o seu processo de fabrico. contacte os nossos especialistas hoje !