O revestimento por Deposição Física de Vapor (PVD) é um processo versátil utilizado para criar revestimentos finos, duradouros e de elevado desempenho em vários substratos.Os produtos químicos utilizados no revestimento PVD dependem das propriedades desejadas do produto final, como a dureza, a resistência à corrosão ou a cor.O processo envolve normalmente a vaporização de um material alvo, frequentemente um metal ou cerâmica, e a sua deposição sobre um substrato num ambiente de vácuo.São normalmente introduzidos gases reactivos como o azoto, o oxigénio ou o acetileno para formar compostos como nitretos, óxidos ou carbonetos, que melhoram as propriedades do revestimento.A escolha de produtos químicos e gases depende da aplicação específica e das caraterísticas desejadas do revestimento.
Pontos-chave explicados:
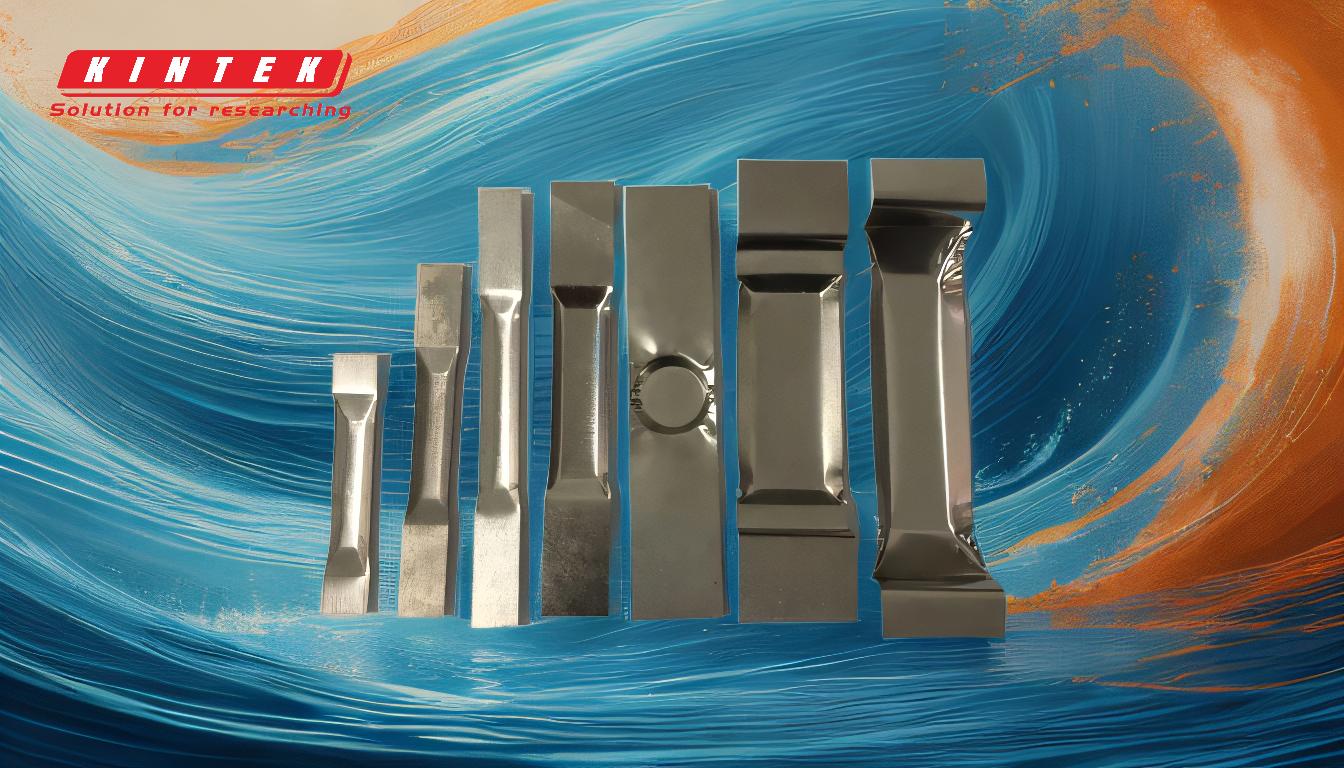
-
Materiais alvo no revestimento PVD:
- Os revestimentos PVD começam frequentemente com um material alvo, que é normalmente um metal ou uma cerâmica.Os metais mais comuns incluem o titânio, o crómio, o alumínio e o ouro, enquanto as cerâmicas, como o carboneto de silício ou o nitreto de titânio, também são utilizadas.
- Estes materiais são escolhidos com base nas propriedades desejadas do revestimento, como a dureza, a resistência ao desgaste ou a estética.
-
Gases reactivos utilizados em PVD:
-
Os gases reactivos desempenham um papel crucial no revestimento PVD, combinando-se com o material alvo vaporizado para formar compostos.Os gases comuns incluem:
- Nitrogénio (N₂):Utilizado para criar revestimentos de nitreto, como o nitreto de titânio (TiN), que são conhecidos pela sua dureza e aparência dourada.
- Oxigénio (O₂):Forma revestimentos de óxidos, como o dióxido de titânio (TiO₂), que são frequentemente utilizados em aplicações ópticas ou fotocatalíticas.
- Acetileno (C₂H₂):Utilizado para criar revestimentos de carboneto, como o carboneto de titânio (TiC), que são extremamente duros e resistentes ao desgaste.
-
Os gases reactivos desempenham um papel crucial no revestimento PVD, combinando-se com o material alvo vaporizado para formar compostos.Os gases comuns incluem:
-
Etapas do processo que envolvem produtos químicos:
- Vaporização:O material alvo é vaporizado utilizando métodos como a pulverização catódica ou a evaporação térmica.Esta etapa requer um controlo preciso da temperatura e da energia utilizada.
- Reação:O material vaporizado reage com os gases introduzidos para formar compostos.Por exemplo, o titânio reage com o azoto para formar nitreto de titânio (TiN).
- Deposição:O material reagido é depositado no substrato de forma controlada, formando uma película fina e uniforme.
-
Aplicações e seleção química:
-
A escolha dos produtos químicos depende da aplicação.Por exemplo:
- Revestimentos para ferramentas:O nitreto de titânio (TiN) é normalmente utilizado em ferramentas de corte devido à sua dureza e resistência ao desgaste.
- Revestimentos decorativos:Os revestimentos à base de ouro ou crómio são utilizados para fins estéticos.
- Revestimentos ópticos:Óxidos como o dióxido de titânio (TiO₂) são utilizados pelas suas propriedades reflectoras ou anti-reflectoras.
-
A escolha dos produtos químicos depende da aplicação.Por exemplo:
-
Vantagens dos produtos químicos de revestimento PVD:
- Pureza:Os revestimentos PVD são altamente puros devido ao ambiente de vácuo, que evita a contaminação.
- Versatilidade:Pode ser utilizada uma vasta gama de materiais e gases, permitindo a personalização das propriedades do revestimento.
- Durabilidade:Os revestimentos resultantes são altamente duráveis, resistentes ao desgaste, à corrosão e a temperaturas elevadas.
-
Considerações sobre segurança e ambiente:
- O revestimento por PVD é geralmente considerado amigo do ambiente em comparação com outros métodos de revestimento, como a galvanoplastia, uma vez que produz menos subprodutos perigosos.
- No entanto, o manuseamento adequado dos gases reactivos e do equipamento de vácuo é essencial para garantir a segurança.
Ao selecionar cuidadosamente os materiais alvo e os gases reactivos, o revestimento PVD pode ser adaptado para satisfazer requisitos de desempenho específicos em várias indústrias, desde a aeroespacial à eletrónica de consumo.
Tabela de resumo:
Categoria | Exemplos | Objetivo |
---|---|---|
Materiais alvo | Titânio, crómio, alumínio, ouro | Proporciona dureza, resistência ao desgaste ou atrativo estético. |
Gases Reactivos | Nitrogénio (N₂), Oxigénio (O₂), Acetileno (C₂H₂) | Forma nitretos, óxidos ou carbonetos para melhorar as propriedades do revestimento. |
Aplicações | Revestimentos para ferramentas, revestimentos decorativos, revestimentos ópticos | Adaptados à dureza, resistência ao desgaste ou propriedades reflectoras. |
Vantagens | Alta pureza, versatilidade, durabilidade | Garante revestimentos livres de contaminação, personalizáveis e de longa duração. |
Pronto para melhorar os seus materiais com revestimentos PVD? Contacte os nossos especialistas hoje para começar!