A prensagem isostática a quente (HIP) é um processo de fabrico que melhora as propriedades dos materiais através da aplicação uniforme de alta temperatura e pressão em todas as direcções.Embora ofereça vantagens significativas, como propriedades mecânicas melhoradas e a capacidade de produzir componentes de alta densidade, também apresenta várias desvantagens.Estas incluem elevados custos de equipamento e de produção, tamanho limitado do alvo devido a restrições do equipamento, baixa eficiência de produção e desafios no controlo da temperatura.Além disso, a HIP requer competências especializadas para a operação e pode não ser compatível com determinados materiais em pó, limitando ainda mais a sua aplicabilidade.
Pontos-chave explicados:
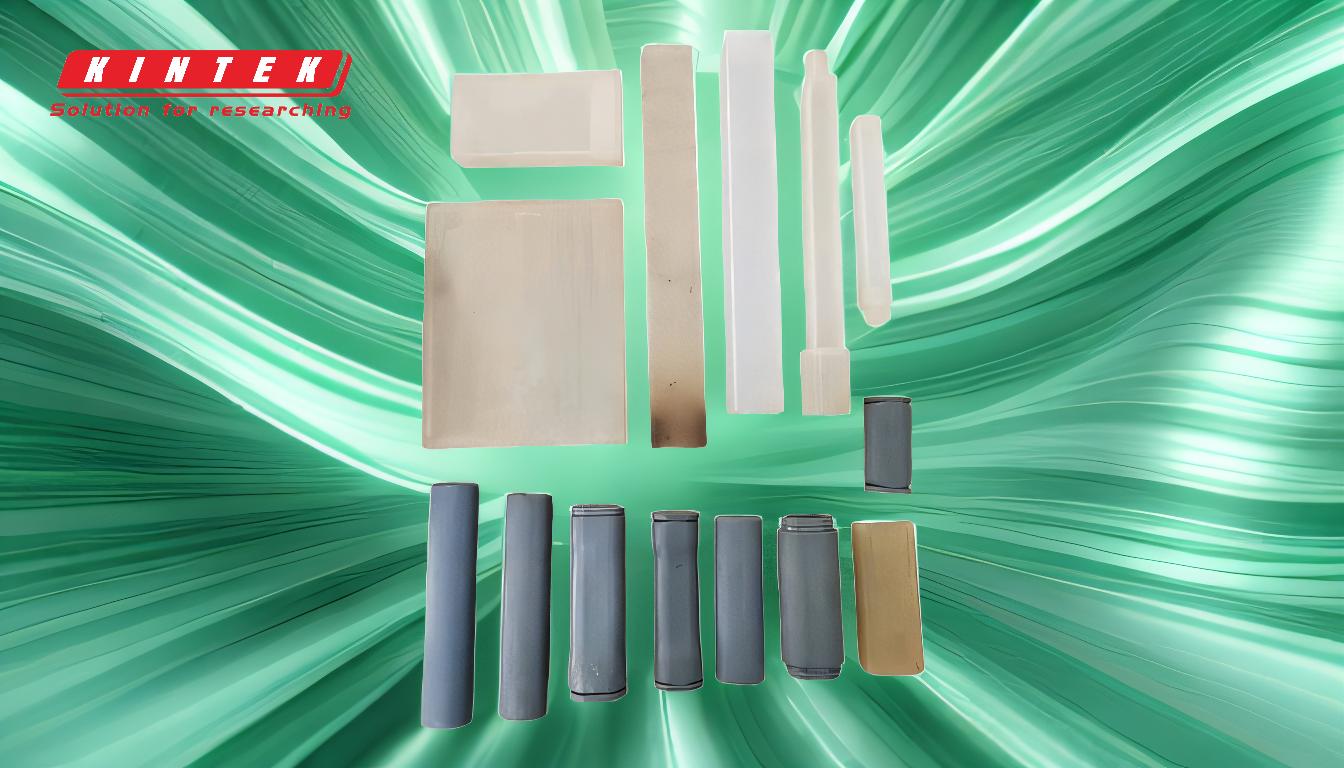
-
Elevados custos de equipamento e de produção:
- A aquisição e manutenção do equipamento HIP é dispendiosa, exigindo um investimento inicial significativo.
- O processo em si é dispendioso devido à necessidade de temperaturas e pressões elevadas, bem como de materiais especializados, como pós secos por pulverização.
- Estes custos tornam a HIP menos competitiva em comparação com outros métodos de sinterização, especialmente para a produção em grande escala.
-
Tamanho limitado do alvo:
- O tamanho dos componentes que podem ser processados utilizando a HIP é limitado pela pressão e pelo tamanho do cilindro de trabalho do equipamento.
- Esta limitação dificulta a produção de alvos de grandes dimensões, restringindo a aplicação da HIP em indústrias que requerem componentes de grandes dimensões.
-
Baixa eficiência de produção:
- A HIP tem taxas de produção relativamente baixas em comparação com métodos como a extrusão ou a compactação de moldes.
- O processo é moroso, o que reduz ainda mais a sua eficiência e aumenta os custos de produção.
-
Desafios no controlo da temperatura:
- O controlo preciso da temperatura é difícil devido ao aquecimento do meio de pressão causado pela fricção e pela sobrealimentação.
- Garantir uma distribuição uniforme da temperatura dentro do cilindro de trabalho também é um desafio, o que pode afetar a qualidade do produto final.
-
Requisitos de competências especializadas:
- O funcionamento do equipamento HIP requer uma mão de obra qualificada, que pode não estar prontamente disponível.
- A complexidade do processo requer formação especializada, aumentando o custo global e limitando a sua adoção em algumas regiões.
-
Questões de compatibilidade de materiais:
- Os pós processados com HIP não são frequentemente compatíveis com os processos de fusão, exigindo temperaturas excessivamente elevadas ou resultando em microestruturas desfavoráveis.
- Esta limitação restringe a gama de materiais que podem ser efetivamente processados com HIP.
-
Exatidão da superfície e requisitos de maquinagem:
- As superfícies dos componentes prensados adjacentes ao saco flexível em HIP têm uma precisão inferior em comparação com a prensagem mecânica ou a extrusão.
- Este facto exige frequentemente uma maquinação adicional, aumentando o tempo e o custo global da produção.
-
Custo inicial e investimento elevados:
- O custo inicial da instalação de uma unidade HIP é elevado, incluindo o custo da prensa, do equipamento auxiliar e das infra-estruturas.
- Este elevado investimento inicial pode constituir um obstáculo para as empresas mais pequenas ou com orçamentos limitados.
Em resumo, embora a HIP ofereça vantagens significativas em termos de propriedades dos materiais e qualidade dos componentes, as suas desvantagens - tais como custos elevados, tamanho limitado, baixa eficiência e requisitos de competências especializadas - tornam-na menos adequada para determinadas aplicações.Estes factores devem ser cuidadosamente considerados quando se avalia a utilização de HIP nos processos de fabrico.
Tabela de resumo:
Desvantagem | Explicação |
---|---|
Elevados custos de equipamento e de produção | Equipamento dispendioso, manutenção elevada e materiais de processamento dispendiosos. |
Tamanho limitado do alvo | Restringido pelo tamanho do equipamento, tornando difícil a produção de componentes de grandes dimensões. |
Baixa eficiência de produção | Processo moroso com taxas de produção mais lentas em comparação com outros métodos. |
Desafios no controlo da temperatura | Dificuldade em manter uma distribuição precisa e uniforme da temperatura. |
Requisitos de competências especializadas | Requer operadores qualificados e formação especializada, aumentando os custos. |
Problemas de compatibilidade de materiais | Compatibilidade limitada com determinados materiais em pó, restringindo as aplicações. |
Precisão da superfície e maquinagem | A menor precisão da superfície requer frequentemente maquinação adicional, aumentando os custos. |
Custo inicial e investimento elevados | Investimento inicial significativo em equipamento e infra-estruturas. |
Está a considerar a HIP para o seu processo de fabrico? Contacte os nossos especialistas hoje para discutir as suas necessidades!