O revestimento por Deposição Física de Vapor (PVD) é um processo sofisticado utilizado para aplicar camadas finas, duradouras e funcionais nas superfícies de vários materiais.O processo envolve a vaporização de um material sólido num ambiente de vácuo e, em seguida, a deposição dos átomos vaporizados no substrato.Isto resulta numa camada fina e ligada que melhora o aspeto, a durabilidade e a funcionalidade do substrato.O processo de revestimento PVD é altamente controlado, envolvendo condições precisas de temperatura e pressão, e é amplamente utilizado em indústrias que exigem revestimentos de alto desempenho, como a aeroespacial, a automóvel e a de dispositivos médicos.
Pontos-chave explicados:
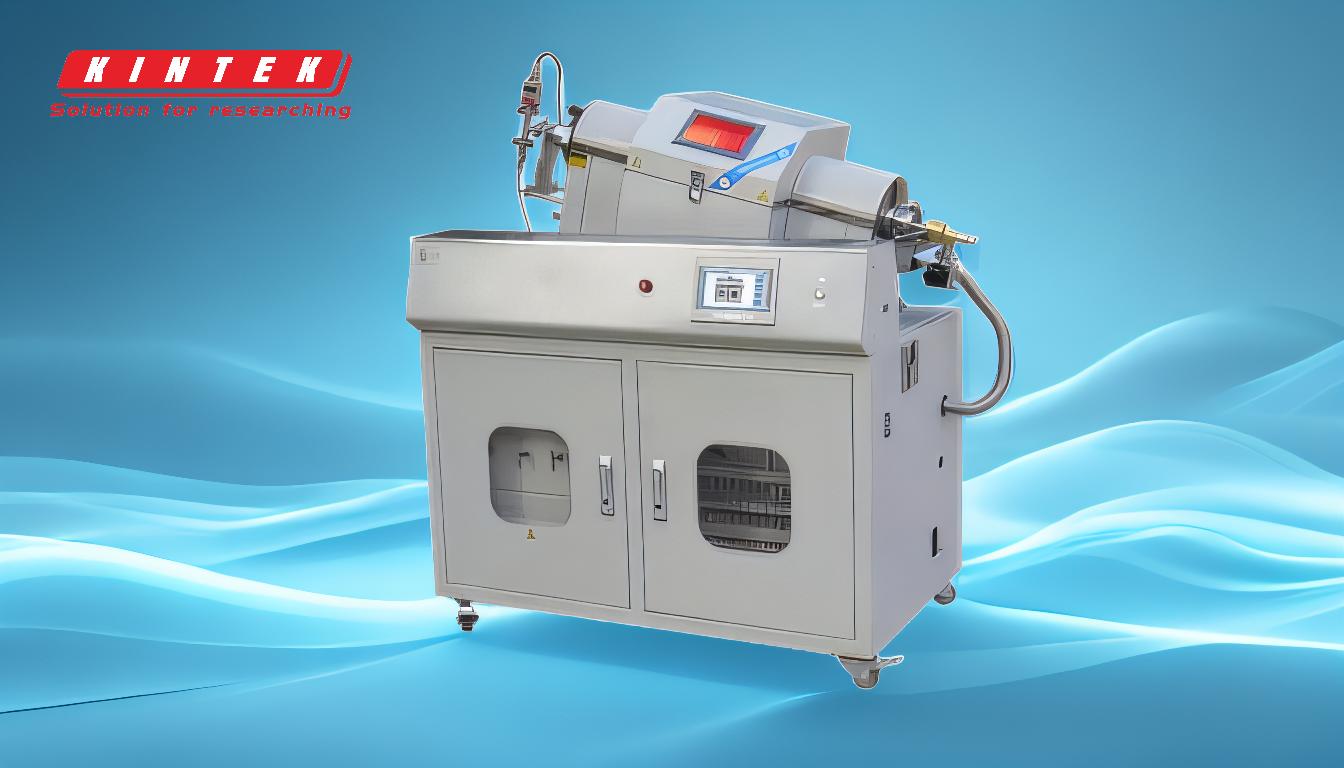
-
Princípio básico do revestimento PVD:
- Vaporização de material sólido: O princípio fundamental do revestimento PVD envolve a vaporização de um material sólido (frequentemente metais como o titânio, o zircónio ou o crómio) num ambiente de vácuo.Isto é conseguido através de vários métodos, como a pulverização catódica, a evaporação por feixe de electrões ou a descarga por arco catódico.
- Deposição no substrato: Os átomos vaporizados viajam através do vácuo e depositam-se na superfície do substrato.Esta deposição ocorre átomo a átomo, formando uma camada fina e uniforme que se liga fortemente ao substrato.
-
Ambiente de vácuo:
- Condições de alto vácuo: O processo tem lugar numa câmara de vácuo, onde a pressão é significativamente reduzida para criar um ambiente de alto vácuo.Isto assegura que o material vaporizado permanece limpo e não contaminado, conduzindo a um revestimento de alta qualidade.
- Atmosfera controlada: O ambiente de vácuo também permite a introdução de gases reactivos (por exemplo, azoto) para modificar a composição do revestimento.Por exemplo, a adição de azoto pode resultar na formação de nitretos metálicos, que melhoram as propriedades do revestimento.
-
Métodos de Vaporização:
- Sputtering: Neste método, iões de alta energia bombardeiam o material alvo, fazendo com que os átomos sejam ejectados da superfície e subsequentemente depositados no substrato.
- Evaporação por feixe de electrões: É utilizado um feixe de electrões para aquecer o material alvo, provocando a sua vaporização.Os átomos vaporizados condensam-se então no substrato.
- Descarga de arco catódico: É utilizado um arco elétrico para vaporizar o material alvo, produzindo um plasma de alta densidade de átomos de metal ionizados que se depositam no substrato.
-
Etapas do processo de revestimento PVD:
- Preparação: O substrato é limpo e colocado na câmara de vácuo.O material alvo é também posicionado dentro da câmara.
- Evacuação: A câmara é evacuada para criar um ambiente de alto vácuo, atingindo normalmente pressões na gama de 10^-3 a 10^-6 Pa.
- Vaporização: O material alvo é vaporizado utilizando um dos métodos acima mencionados (pulverização catódica, evaporação por feixe de electrões ou descarga por arco catódico).
- Transporte: Os átomos vaporizados viajam através do vácuo e são transportados para o substrato.
- Deposição: Os átomos condensam-se no substrato, formando uma camada fina e uniforme.O substrato pode ser rodado ou movido para assegurar um revestimento uniforme.
- Purga: Após a deposição, a câmara é purgada com gás inerte para remover quaisquer vapores residuais e preparar o ciclo seguinte.
-
Vantagens do revestimento PVD:
- Durabilidade: Os revestimentos PVD são altamente duráveis, oferecendo excelente resistência ao desgaste, à corrosão e a altas temperaturas.
- Finos e uniformes: Os revestimentos são extremamente finos (normalmente na gama dos nanómetros a micrómetros) e uniformes, garantindo um desempenho consistente.
- Amigo do ambiente: O revestimento PVD é considerado mais amigo do ambiente em comparação com outros métodos de revestimento como a Deposição Química de Vapor (CVD), uma vez que produz menos subprodutos nocivos.
- Versatilidade: Os revestimentos PVD podem ser aplicados a uma vasta gama de materiais, incluindo metais, cerâmicas e polímeros, o que os torna adequados para várias aplicações.
-
Aplicações do revestimento PVD:
- Aeroespacial: Os revestimentos PVD são utilizados para melhorar o desempenho e a longevidade dos componentes aeroespaciais, tais como lâminas de turbinas e peças de motores.
- Setor automóvel: Na indústria automóvel, os revestimentos PVD são aplicados para melhorar a resistência ao desgaste e o aspeto estético de componentes como peças de motor, rodas e acabamentos.
- Dispositivos médicos: Os revestimentos PVD são utilizados em implantes médicos e instrumentos cirúrgicos para melhorar a biocompatibilidade e reduzir o desgaste.
- Eletrónica de consumo: Os revestimentos PVD são aplicados a capas de smartphones, relógios e outros dispositivos electrónicos para aumentar a durabilidade e proporcionar um acabamento de qualidade superior.
Em resumo, o revestimento PVD é um processo altamente controlado e versátil que envolve a vaporização de um material sólido no vácuo e a sua deposição num substrato para formar uma camada fina, durável e funcional.O processo oferece inúmeras vantagens, incluindo durabilidade, uniformidade e respeito pelo ambiente, tornando-o adequado para uma vasta gama de aplicações industriais.
Tabela de resumo:
Aspeto | Detalhes |
---|---|
Princípio básico | Vaporização de material sólido em vácuo e deposição num substrato. |
Ambiente de vácuo | As condições de alto vácuo garantem revestimentos limpos e não contaminados. |
Métodos de vaporização | Sputtering, evaporação por feixe de electrões, descarga por arco catódico. |
Etapas do processo | Preparação, evacuação, vaporização, transporte, deposição, purga. |
Vantagens | Durabilidade, camadas finas e uniformes, amigo do ambiente, aplicações versáteis. |
Aplicações | Aeroespacial, automóvel, dispositivos médicos, eletrónica de consumo. |
Descubra como o revestimento PVD pode elevar os seus produtos- contacte os nossos especialistas hoje mesmo !