A moldagem por injeção é um processo de fabrico utilizado para produzir peças através da injeção de material fundido num molde. O processo é altamente eficiente e pode ser dividido em quatro fases principais: fixação, injeção, arrefecimento e ejeção. Cada fase desempenha um papel fundamental para garantir que o produto final cumpre as especificações desejadas. O ciclo completo dura normalmente entre 2 segundos e 2 minutos, consoante a complexidade da peça e o material utilizado. Abaixo, exploraremos cada fase em pormenor para proporcionar uma compreensão abrangente do processo de moldagem por injeção.
Pontos-chave explicados:
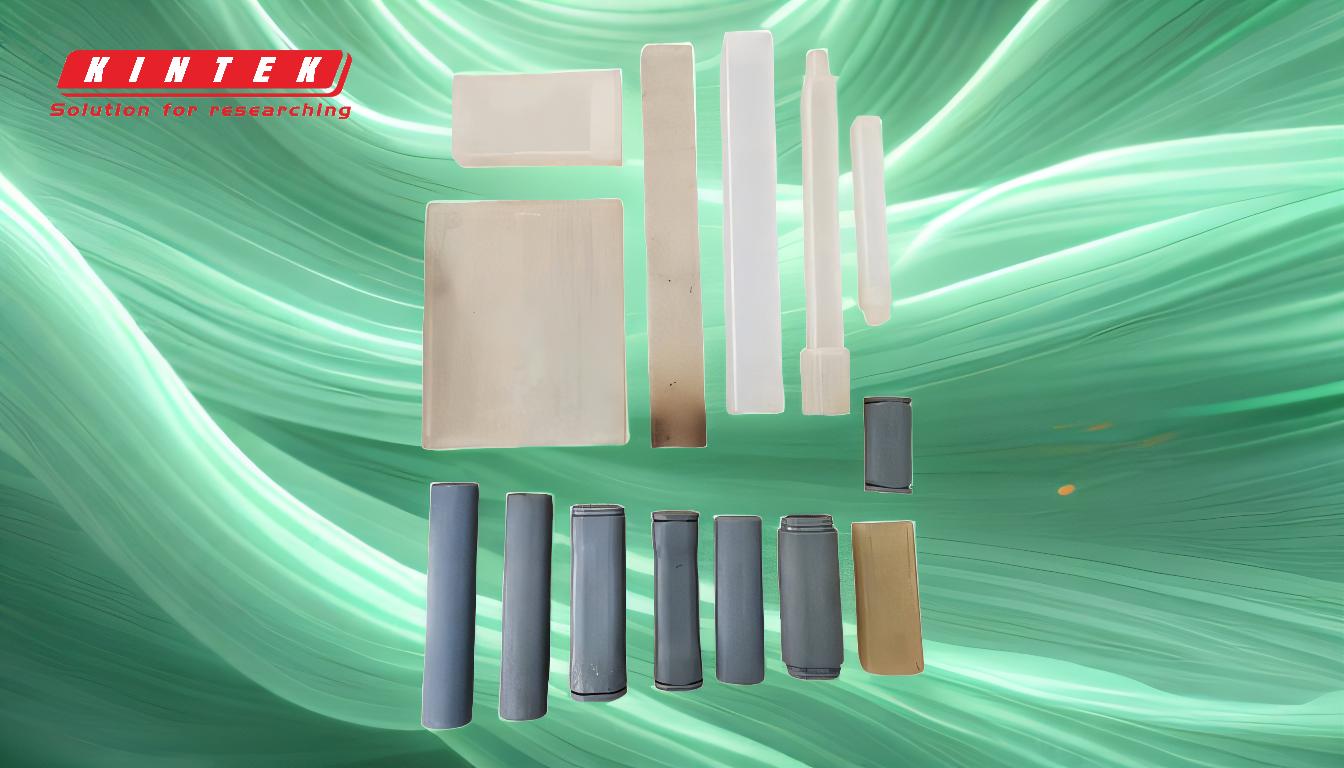
-
Fase de fixação
- Objetivo: A fase de fixação envolve a fixação das duas metades do molde para preparar a injeção do material fundido.
-
Processo:
- O molde é constituído por duas metades: a metade fixa (ligada à máquina de moldagem por injeção) e a metade móvel (que abre e fecha).
- Uma unidade de fixação aplica pressão para manter as metades do molde firmemente unidas durante o processo de injeção.
- A força de aperto deve ser suficiente para suportar a pressão do material injetado, evitando qualquer fuga ou deformação do molde.
- Importância: Uma fixação correta garante que o molde permanece fechado e estável, o que é fundamental para produzir peças de alta qualidade com dimensões precisas.
-
Fase de Injeção
- Objetivo: Nesta fase, o material fundido é injetado na cavidade do molde para formar a peça desejada.
-
Processo de injeção:
- O material (normalmente granulado de plástico) é introduzido num cilindro aquecido, onde é derretido e homogeneizado.
- Um parafuso ou êmbolo alternativo empurra o material fundido para a cavidade do molde sob alta pressão.
- O material preenche a cavidade, tomando a forma do molde.
-
Factores a considerar:
- A pressão de injeção, a velocidade e a temperatura devem ser cuidadosamente controladas para garantir que o material preenche o molde completa e uniformemente.
- O enchimento excessivo ou insuficiente do molde pode levar a defeitos como deformações, marcas de afundamento ou peças incompletas.
- Importância: A fase de injeção determina a forma inicial e a integridade da peça, o que a torna uma etapa crítica do processo.
-
Fase de arrefecimento
- Objetivo: Depois de o molde estar cheio, o material tem de arrefecer e solidificar para manter a sua forma.
-
Processo:
- O arrefecimento começa assim que o material é injetado no molde.
- O molde é concebido com canais de arrefecimento através dos quais circula um líquido de arrefecimento (normalmente água) para dissipar o calor.
- O tempo de arrefecimento depende das propriedades do material, da espessura da peça e do desenho do molde.
-
Factores a considerar:
- Um arrefecimento insuficiente pode levar a deformações ou tensões internas na peça.
- Um arrefecimento excessivo pode aumentar o tempo de ciclo, reduzindo a eficiência da produção.
- Importância: Um arrefecimento adequado garante que a peça solidifica corretamente, mantendo a precisão dimensional e a integridade estrutural.
-
Fase de ejeção
- Objetivo: Depois de a peça ter arrefecido e solidificado, é ejectada do molde.
-
Processo:
- O molde abre-se e os pinos ou placas ejectores empurram a peça para fora da cavidade do molde.
- A peça é então removida da máquina, manual ou automaticamente.
-
Factores a considerar:
- A ejeção deve ser feita com cuidado para evitar danificar a peça ou o molde.
- A conceção adequada do molde, incluindo a colocação dos pinos ejectores, é crucial para garantir uma ejeção suave.
- Importância: A fase de ejeção completa o ciclo, permitindo que o molde seja preparado para a injeção seguinte.
Considerações adicionais para os compradores de equipamentos e consumíveis:
- Seleção do material: O tipo de material utilizado (por exemplo, termoplásticos, polímeros termoendurecíveis) afecta o processo de moldagem e as propriedades do produto final.
- Conceção do molde: Um molde bem concebido com canais de arrefecimento e mecanismos de ejeção adequados é essencial para uma produção eficiente.
- Especificações da máquina: A máquina de moldagem por injeção deve ter a força de aperto, a pressão de injeção e a capacidade de arrefecimento adequadas para lidar com os requisitos específicos da peça.
- Otimização do tempo de ciclo: A redução do tempo de ciclo, mantendo a qualidade, é fundamental para melhorar a eficiência da produção e reduzir os custos.
Ao compreender estas fases e a sua importância, os compradores de equipamento e consumíveis podem tomar decisões informadas para otimizar o processo de moldagem por injeção para as suas necessidades específicas.
Tabela de resumo:
Fase | Objetivo | Processo chave | Importância |
---|---|---|---|
Fixação | Fixar as metades do molde para injeção | Aplicar força de fixação para segurar o molde firmemente; evitar fugas ou deformações | Garante a estabilidade do molde e as dimensões exactas da peça |
Injeção | Injetar material fundido na cavidade do molde | Derreter o material, empurrar para o molde sob alta pressão; controlar a pressão, a velocidade e a temperatura | Determina a forma e a integridade da peça; essencial para resultados sem defeitos |
Arrefecimento | Solidificar o material para manter a forma | Circulação do líquido de arrefecimento através dos canais do molde; controlo do tempo de arrefecimento com base no material e na espessura da peça | Assegura a precisão dimensional e a integridade estrutural; evita a deformação |
Ejeção | Retirar a peça solidificada do molde | Abrir o molde e utilizar pinos/placas ejectores para empurrar a peça para fora; assegurar uma ejeção suave | Completa o ciclo; prepara o molde para a injeção seguinte |
Pronto para otimizar o seu processo de moldagem por injeção? Contacte hoje os nossos especialistas para obter soluções à medida!