Os revestimentos PVD (Physical Vapor Deposition) são efetivamente resistentes aos riscos, graças à sua elevada dureza e durabilidade.Estes revestimentos são aplicados ao nível atómico, permitindo um controlo preciso das suas propriedades, como a dureza, a densidade e a aderência.Os revestimentos PVD são quatro vezes mais duros do que o crómio, o que os torna altamente resistentes a riscos, corrosão e desgaste.A sua dureza varia entre 1500 e 4500 HV (Vickers), significativamente superior à de muitos materiais tradicionais, como o aço-carbono ou o aço niquelado.Além disso, os revestimentos PVD aderem fortemente ao substrato, garantindo um desempenho duradouro mesmo em ambientes agressivos.Os seus baixos requisitos de manutenção e acabamentos decorativos aumentam ainda mais o seu atrativo para aplicações funcionais e estéticas.
Explicação dos pontos principais:
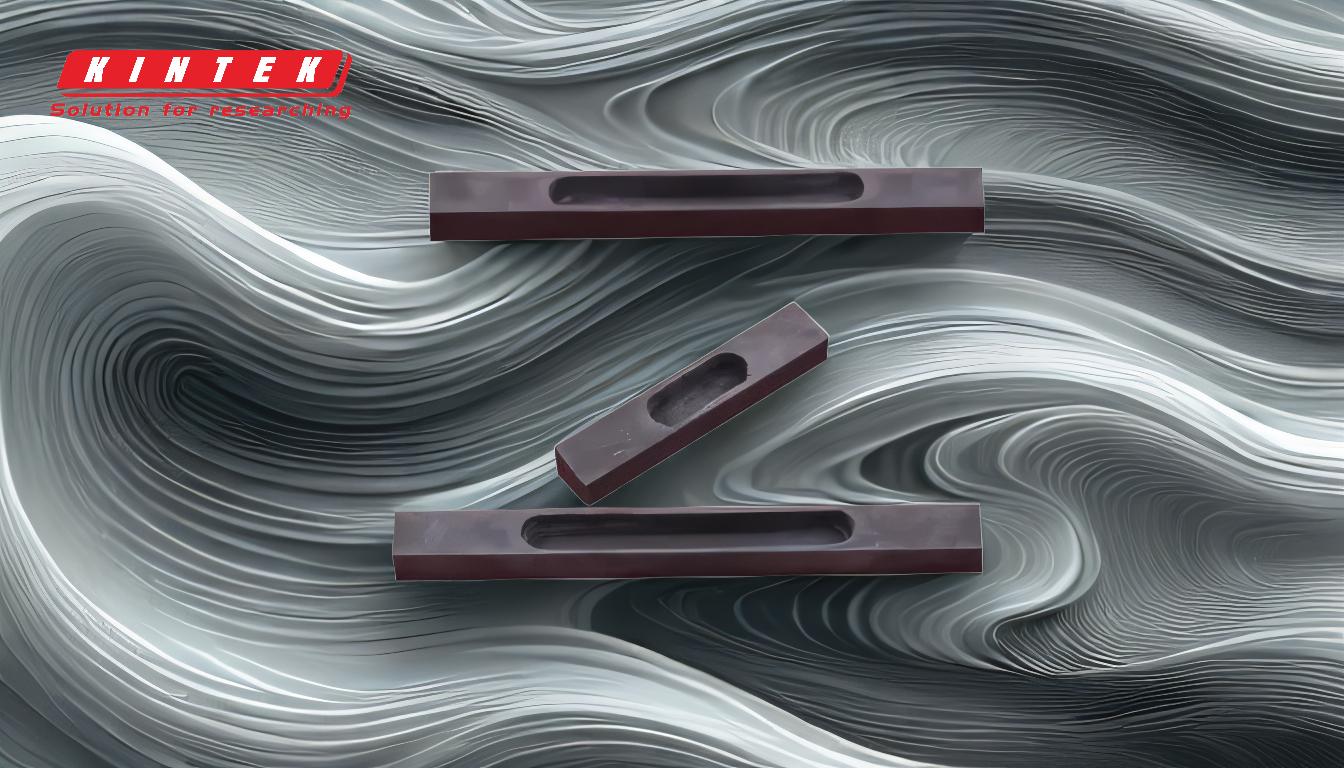
-
Elevada dureza dos revestimentos PVD:
-
Os revestimentos PVD têm uma gama de dureza de 1500-4500 HV (Vickers), o que é significativamente mais elevado do que muitos materiais tradicionais.Para comparação:
- Aço carbono: ~250 HV (25 HRC).
- Aço niquelado e cromado: 600-1000 HV.
- Esta elevada dureza contribui para a resistência aos riscos, uma vez que os materiais mais duros são menos susceptíveis de sofrerem deformações ou danos por abrasão.
-
Os revestimentos PVD têm uma gama de dureza de 1500-4500 HV (Vickers), o que é significativamente mais elevado do que muitos materiais tradicionais.Para comparação:
-
Comparação com o crómio:
- Os revestimentos PVD são quatro vezes mais duros do que o crómio, o que os torna mais resistentes aos riscos e ao desgaste.
- Esta dureza acrescida também aumenta a sua durabilidade em ambientes agressivos, como zonas costeiras ou ambientes industriais.
-
Aplicação ao nível atómico:
- Os revestimentos PVD são aplicados ao nível atómico, permitindo um controlo preciso da sua estrutura, densidade e estequiometria.
- Esta precisão permite a criação de revestimentos com atributos específicos, tais como elevada dureza, lubricidade e aderência, que contribuem para a resistência aos riscos.
-
Forte aderência ao substrato:
- Os revestimentos PVD aderem fortemente ao substrato, penetrando-o mesmo ligeiramente, o que garante uma adesão duradoura.
- Esta forte ligação evita que se lasquem ou descasquem, aumentando ainda mais a resistência aos riscos e a durabilidade geral.
-
Resistência ao desgaste e à corrosão:
- Os revestimentos PVD são altamente resistentes ao desgaste e à corrosão, o que os torna adequados para aplicações expostas a condições adversas.
- O seu baixo coeficiente de fricção e resistência química também contribuem para a sua longevidade e resistência aos riscos.
-
Benefícios ambientais e de manutenção:
- Os revestimentos PVD são amigos do ambiente e requerem pouca manutenção.
- A sua resistência ao embaciamento, ao desbotamento e aos riscos garante que mantêm o seu aspeto e funcionalidade ao longo do tempo.
-
Aplicações e versatilidade:
- Os revestimentos PVD são ideais para fins funcionais e decorativos, oferecendo um acabamento brilhante e uma resistência superior aos riscos.
- São amplamente utilizados em indústrias como a automóvel, a aeroespacial e a de bens de consumo, onde a durabilidade e a estética são fundamentais.
Em resumo, os revestimentos PVD são altamente resistentes a riscos devido à sua dureza excecional, forte adesão aos substratos e aplicação precisa ao nível atómico.Estas propriedades tornam-nos uma escolha superior para aplicações que requerem durabilidade, longevidade e atrativo estético.
Tabela de resumo:
Propriedade | Revestimentos PVD | Materiais tradicionais |
---|---|---|
Dureza (HV) | 1500-4500 | Aço carbono: ~250 |
Resistência aos riscos | Alta | Baixa a moderada |
Resistência ao desgaste e à corrosão | Excelente | Moderado |
Adesão ao substrato | Forte | Variável |
Requisitos de manutenção | Baixa | Alta |
Aplicações | Indústria automóvel, indústria aeroespacial, bens de consumo | Utilização geral |
Descubra como os revestimentos PVD podem melhorar a durabilidade e a estética do seu produto. contacte-nos hoje !