O revestimento de carbono tipo diamante (DLC) é aplicado utilizando técnicas de deposição avançadas que garantem um revestimento forte, duradouro e de elevado desempenho.Os métodos mais comuns incluem a Deposição Física de Vapor (PVD) e a Deposição Química de Vapor (CVD), com variações como a CVD assistida por plasma de radiofrequência (RF PECVD) e a CVD de filamento quente.Estes métodos envolvem a criação de um ambiente controlado numa câmara de vácuo, onde os átomos de carbono são activados e depositados no substrato.A escolha do método depende do material do substrato, das propriedades desejadas do revestimento e dos requisitos da aplicação.Os revestimentos DLC são normalmente finos (0,5 a 2,5 microns) e proporcionam uma excelente resistência ao desgaste, baixa fricção e maior durabilidade.
Pontos-chave explicados:
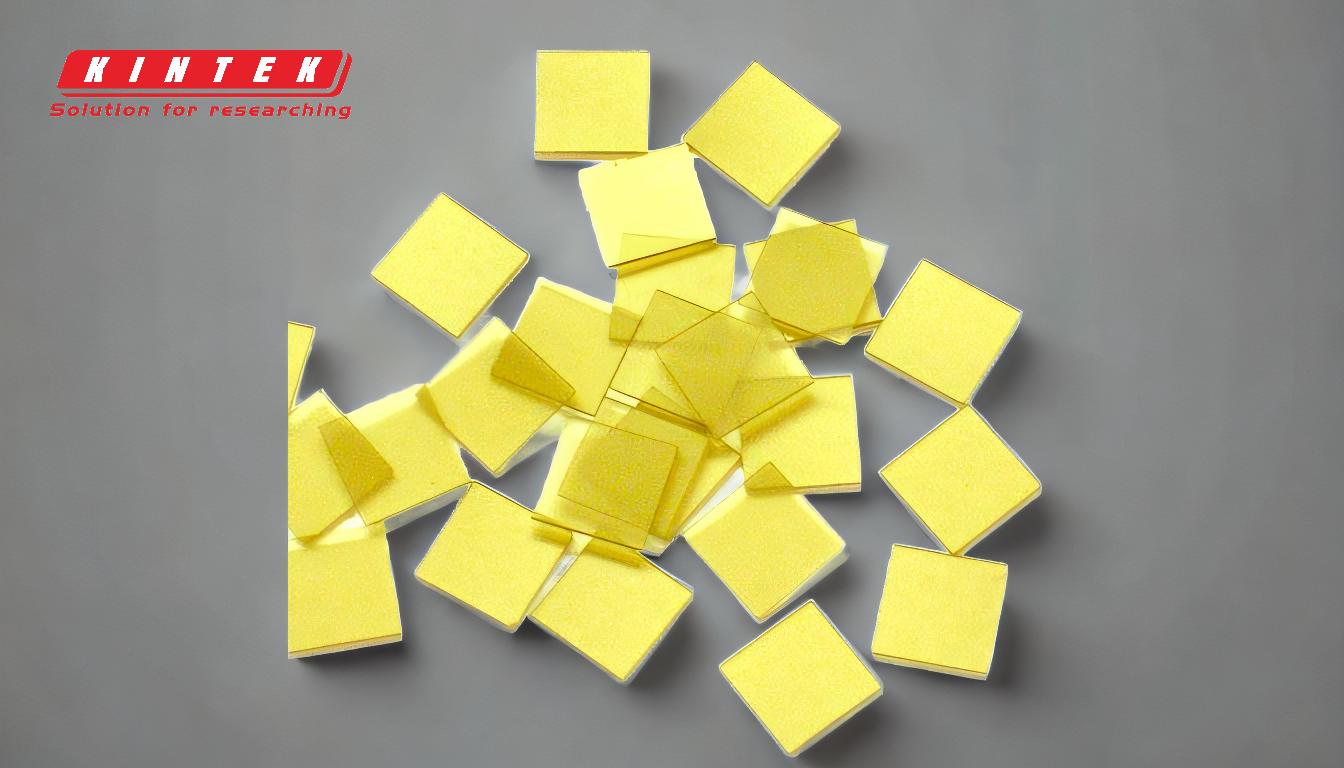
-
Visão geral da aplicação do revestimento DLC
- Os revestimentos DLC são aplicados utilizando técnicas de deposição avançadas para criar uma camada fina e duradoura de carbono com uma proporção significativa de ligações sp3.
- O processo de revestimento é adaptado ao material do substrato e à aplicação pretendida, garantindo um desempenho ótimo.
-
Métodos de deposição comuns
-
Deposição física de vapor (PVD):
- Envolve a evaporação de um material de origem e permite a sua condensação no substrato.
- Adequado para aplicar revestimentos DLC em ferramentas de metal duro, com uma espessura típica de 0,5 a 2,5 microns.
- As vantagens incluem o controlo preciso da espessura e uniformidade do revestimento.
-
Deposição de vapor químico (CVD):
- Envolve a deposição de átomos de carbono a partir de uma fase gasosa (por exemplo, hidrogénio e metano) no substrato.
- As técnicas mais comuns incluem a CVD de filamento quente, a CVD assistida por plasma de radiofrequência (RF PECVD) e a CVD por plasma de micro-ondas (MPCVD).
- Requer temperaturas elevadas (mais de 750°C) para ativar as moléculas de gás e formar uma película de diamante.
-
Deposição física de vapor (PVD):
-
Processo passo a passo para o revestimento CVD
-
Preparação:
- O substrato (por exemplo, ferramentas de carboneto de tungsténio) é limpo e preparado para garantir a aderência adequada do revestimento.
-
Carregamento na câmara:
- As ferramentas preparadas são colocadas numa câmara de vácuo contendo gases de hidrogénio e metano.
-
Ativação das moléculas de gás:
- Fios de tungsténio aquecidos a mais de 2.300°C fornecem a energia para quebrar as moléculas de gás e aquecer as ferramentas a mais de 750°C.
-
Deposição de átomos de carbono:
- Os átomos de carbono activados recombinam-se na superfície da ferramenta para formar uma película de diamante puro.
-
Arrefecimento e remoção:
- Após a deposição, as ferramentas são arrefecidas e retiradas da câmara, prontas a serem utilizadas.
-
Preparação:
-
Vantagens dos diferentes métodos
-
PVD:
- Temperaturas de processamento mais baixas, tornando-o adequado para substratos sensíveis à temperatura.
- Alta precisão e uniformidade na espessura do revestimento.
-
CVD:
- Produz películas de diamante puro de alta qualidade com excelente aderência.
- Ideal para aplicações de alta temperatura e substratos que podem suportar condições extremas.
-
PVD:
-
Aplicações dos revestimentos DLC
-
Ferramentas de corte:
- Aumenta a resistência ao desgaste e prolonga a vida útil das ferramentas.
-
Componentes automóveis:
- Reduz a fricção e melhora a eficiência do combustível nas peças do motor.
-
Dispositivos médicos:
- Proporciona biocompatibilidade e resistência ao desgaste para instrumentos cirúrgicos.
-
Eletrónica:
- Melhora a durabilidade e o desempenho de componentes como discos rígidos e sensores.
-
Ferramentas de corte:
-
Considerações para os compradores de equipamentos e consumíveis
-
Compatibilidade do substrato:
- Assegurar que o método escolhido é compatível com o material do substrato (por exemplo, carboneto, aço ou cerâmica).
-
Espessura e uniformidade do revestimento:
- Avaliar a espessura e a uniformidade necessárias para a aplicação específica.
-
Custo e escalabilidade:
- Considerar a relação custo-eficácia e a escalabilidade do método escolhido para a produção em grande escala.
-
Factores ambientais e de segurança:
- Avaliar o impacto ambiental e os requisitos de segurança do processo de deposição.
-
Compatibilidade do substrato:
Ao compreender estes pontos-chave, os compradores de equipamento e consumíveis podem tomar decisões informadas sobre o melhor método de revestimento DLC para as suas necessidades específicas, garantindo um desempenho ótimo e uma boa relação custo-eficácia.
Tabela de resumo:
Aspeto | Detalhes |
---|---|
Métodos comuns | PVD, CVD (RF PECVD, CVD de filamento quente) |
Espessura do revestimento | 0,5 a 2,5 microns |
Principais vantagens | Resistência ao desgaste, baixa fricção, durabilidade |
Aplicações | Ferramentas de corte, peças para automóveis, dispositivos médicos, eletrónica |
Compatibilidade de substratos | Carboneto, aço, cerâmica |
Gama de temperaturas | PVD:Temperaturas mais baixas; CVD:Mais de 750°C |
Factores ambientais | Câmara de vácuo, ambiente de gás controlado |
Descubra a solução de revestimento DLC ideal para as suas necessidades- contacte hoje os nossos especialistas !