Os revestimentos PVD (Physical Vapor Deposition) são conhecidos pela sua excecional durabilidade e resistência ao desgaste, à corrosão e à lascagem.Estes revestimentos ligam-se ao substrato a nível molecular, criando uma camada forte e fina que é altamente resistente a forças externas.Devido à sua dureza, resistência ao desgaste e propriedades de baixa fricção, os revestimentos PVD são menos susceptíveis de lascar em comparação com os revestimentos tradicionais.A sua capacidade de resistir a ambientes agressivos, incluindo temperaturas elevadas e condições corrosivas, aumenta ainda mais a sua durabilidade.Embora nenhum revestimento seja totalmente imune a danos, os revestimentos PVD estão entre as opções mais duradouras disponíveis, o que os torna ideais para aplicações exigentes em indústrias como a automóvel, a aeroespacial e a médica.
Pontos-chave explicados:
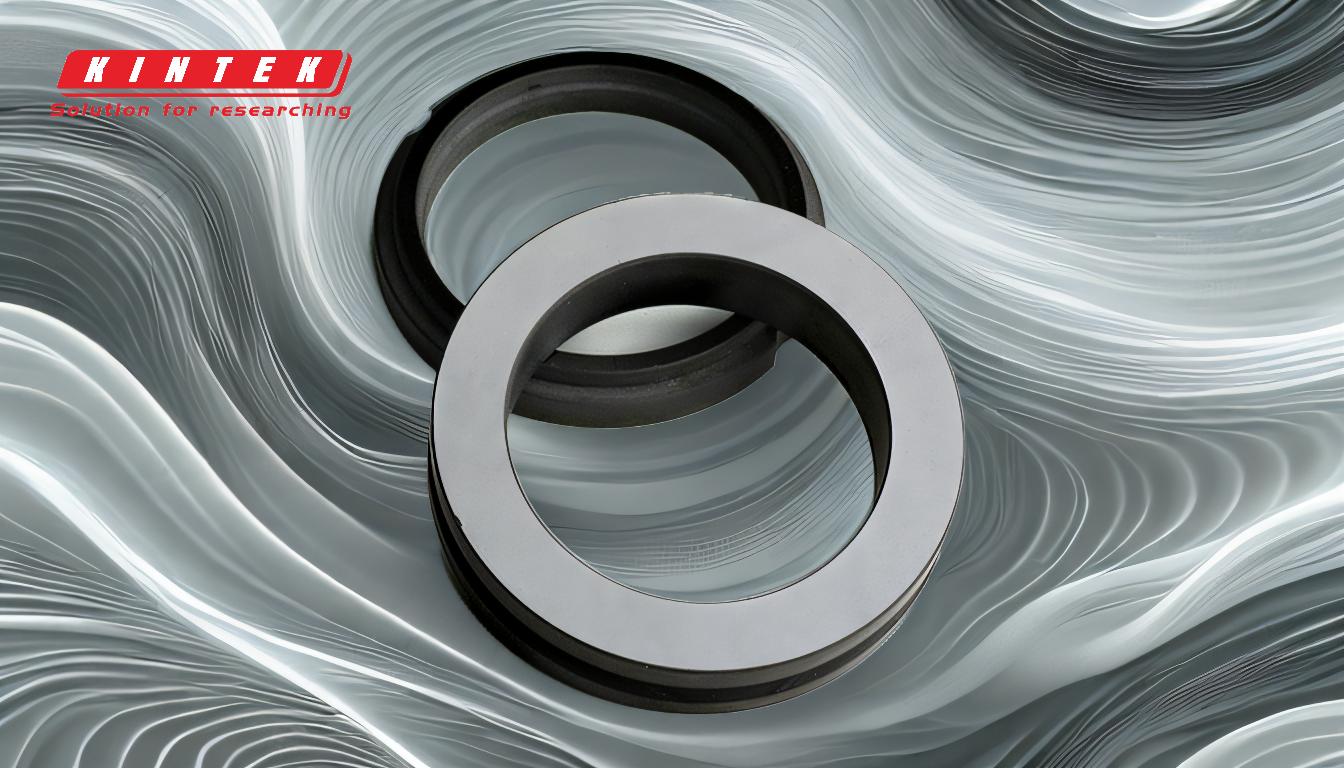
-
Ligação molecular e adesão
- Os revestimentos PVD formam uma ligação a nível molecular com o substrato, criando uma ligação forte e duradoura.
- Este mecanismo de ligação assegura que o revestimento adere firmemente à superfície, tornando-o resistente a lascar mesmo sob tensão mecânica ou impacto.
-
Dureza e resistência ao desgaste
- Os revestimentos PVD são conhecidos pela sua elevada dureza, muitas vezes superior à dos revestimentos tradicionais.
- A dureza do revestimento contribui para a sua capacidade de resistir ao desgaste, à abrasão e à lascagem, mesmo em ambientes de elevado stress.
-
Camada fina e durável
- Os revestimentos PVD são extremamente finos, variando normalmente entre 0,5 e 5 microns.
- Apesar da sua finura, estes revestimentos são altamente duráveis e difíceis de remover, reduzindo ainda mais a probabilidade de lascar.
-
Resistência à corrosão e à oxidação
- O ambiente de vácuo durante o processo PVD elimina a contaminação e evita a oxidação, resultando num revestimento que é altamente resistente à corrosão e à degradação ambiental.
- Esta resistência aumenta a durabilidade e a longevidade global do revestimento, reduzindo o risco de lascar ao longo do tempo.
-
Aplicações em sectores exigentes
- Os revestimentos PVD são amplamente utilizados em indústrias como a automóvel, a aeroespacial e a médica, onde a durabilidade e a resistência ao desgaste são fundamentais.
- A sua capacidade de resistir a condições adversas e ao stress mecânico torna-os menos propensos a lascar em comparação com outros revestimentos.
-
Comparação com os revestimentos tradicionais
- Ao contrário dos acabamentos tradicionais, os revestimentos PVD são significativamente mais duros e mais resistentes ao desgaste e à corrosão.
- Esta durabilidade superior torna-os menos susceptíveis de lascar, mesmo quando sujeitos a um manuseamento brusco ou a condições extremas.
-
Desempenho no mundo real
- Foi demonstrado que os revestimentos PVD melhoram o limite de fadiga e a resistência de materiais, como a liga Ti-6Al-4V, em percentagens significativas.
- Estas melhorias de desempenho demonstram ainda a capacidade do revestimento para resistir a danos, incluindo lascagem, em condições reais.
Em resumo, embora nenhum revestimento seja totalmente imune a danos, os revestimentos PVD estão entre as opções mais duráveis e resistentes a lascas disponíveis.A sua ligação molecular, dureza, espessura e resistência à corrosão e ao desgaste fazem deles uma excelente escolha para aplicações em que a durabilidade e a longevidade são fundamentais.
Tabela de resumo:
Caraterística-chave | Descrição |
---|---|
Ligação molecular | Forma uma ligação forte, a nível molecular, com o substrato, reduzindo os riscos de lascagem. |
Dureza e resistência ao desgaste | Ultrapassa os revestimentos tradicionais, oferecendo uma resistência superior ao desgaste e à abrasão. |
Camada fina e durável | Extremamente fina (0,5-5 mícrones), mas altamente durável, minimizando a formação de lascas. |
Resistência à corrosão | Resiste à corrosão e à oxidação, aumentando a longevidade em ambientes agressivos. |
Aplicações industriais | Amplamente utilizado na indústria automóvel, aeroespacial e médica para durabilidade e desempenho. |
Desempenho no mundo real | Melhora os limites de fadiga e a resistência, reduzindo os danos em condições extremas. |
Pretende aumentar a durabilidade dos seus materiais com revestimentos PVD? Contacte-nos hoje para saber mais!