Os revestimentos PVD (Deposição Física de Vapor) são conhecidos pelas suas propriedades finas, duradouras e de elevado desempenho.O tamanho ou espessura dos revestimentos PVD varia normalmente entre 0,25 mícron e 5 mícrones, dependendo da aplicação e do material.Esta espessura garante que os revestimentos não alteram as especificações das peças projectadas, proporcionando simultaneamente uma excelente dureza, resistência à corrosão e durabilidade.Os revestimentos PVD são amplamente utilizados em indústrias como a joalharia, a eletrónica e a indústria transformadora, devido ao seu desempenho superior em comparação com os métodos de revestimento tradicionais, como a galvanoplastia.Factores como o material do substrato, a espessura do revestimento e as condições de aplicação influenciam a longevidade e a eficácia dos revestimentos PVD.
Explicação dos pontos principais:
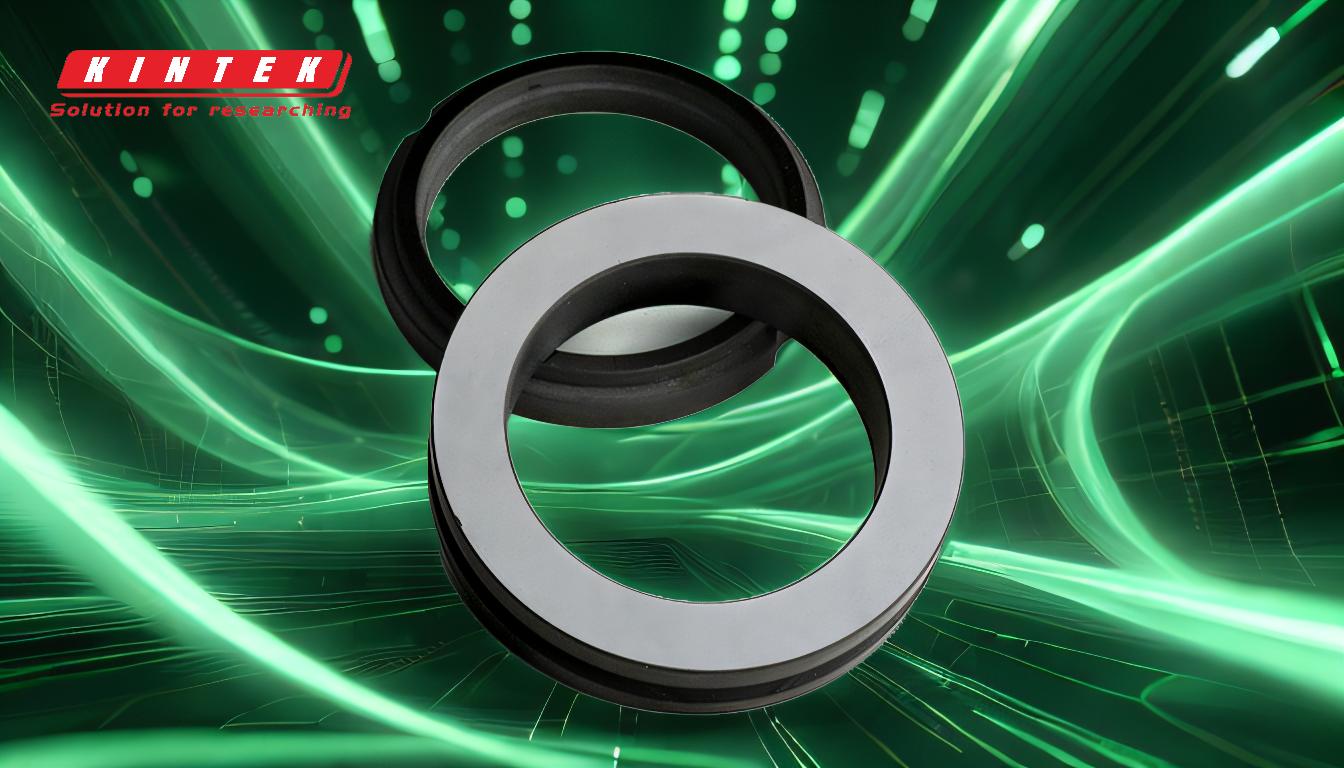
-
Gama de espessuras típicas dos revestimentos PVD:
- Os revestimentos PVD são geralmente muito finos, variando de 0,25 mícrones a 5 mícrones .Esta gama é significativamente mais fina do que o diâmetro de um cabelo humano, que é de cerca de 70 microns.Esta espessura garante que o revestimento não altera as dimensões ou especificações do material subjacente, tornando-o ideal para aplicações de precisão.
-
Aplicações e variações de espessura:
-
A espessura dos revestimentos PVD pode variar consoante a aplicação.Por exemplo:
- Na jóias A espessura do revestimento varia normalmente entre 0,25 mícron e 5 mícrones, proporcionando um acabamento durável e esteticamente agradável.
- Em aplicações industriais como o revestimento de bolachas, as espessuras podem ser tão baixas como 3 nanómetros como se vê no exemplo de um revestimento de ouro/paládio aplicado a uma bolacha de 6 polegadas utilizando um revestimento por pulverização catódica.
-
A espessura dos revestimentos PVD pode variar consoante a aplicação.Por exemplo:
-
Comparação com outros métodos de revestimento:
- Os revestimentos PVD são mais finos do que os produzidos por deposição química de vapor (CVD) que, normalmente, variam entre 5-10 microns.Apesar da sua espessura reduzida, os revestimentos PVD são mais duros, mais resistentes à corrosão e mais amigos do ambiente do que os métodos tradicionais, como a galvanoplastia e a pintura.
-
Durabilidade e longevidade:
-
Os revestimentos PVD são conhecidos pela sua durabilidade, que pode ir de
10 anos a centenas de anos
dependendo de factores como:
- O material de substrato que está a ser revestido.
- A espessura do revestimento .
- As condições de aplicação como a exposição a temperaturas elevadas ou a ambientes corrosivos.
-
Os revestimentos PVD são conhecidos pela sua durabilidade, que pode ir de
10 anos a centenas de anos
dependendo de factores como:
-
Vantagens dos revestimentos PVD:
- Dureza e resistência à corrosão:Os revestimentos PVD são mais duros e mais resistentes à corrosão do que os revestimentos galvanizados.
- Desempenho a altas temperaturas:Resistem a temperaturas elevadas e têm uma boa resistência ao impacto.
- Resistência à abrasão:Com uma camada superior transparente adicional resistente à abrasão, os revestimentos PVD alcançam uma excelente resistência ao desgaste.
- Respeito pelo ambiente:O PVD é um processo mais sustentável e amigo do ambiente em comparação com os métodos de revestimento tradicionais.
-
Processo de produção:
-
Os revestimentos PVD são produzidos por
condensação de vapores
de materiais como metais, carbono, cerâmica, vidro ou polímeros numa superfície adequada.As duas tecnologias de revestimento PVD mais utilizadas são
- Evaporação:O processo consiste em aquecer o material de revestimento até à sua vaporização e depois depositá-lo no substrato.
- Sputtering:Utiliza um plasma para ejetar átomos de um material alvo, que depois se depositam no substrato.
-
Os revestimentos PVD são produzidos por
condensação de vapores
de materiais como metais, carbono, cerâmica, vidro ou polímeros numa superfície adequada.As duas tecnologias de revestimento PVD mais utilizadas são
-
Importância da finura:
- A espessura dos revestimentos PVD (0,5 microns a 5 microns) garante que não alteram as especificações das peças projectadas .Isto é particularmente importante nas indústrias em que a precisão e a exatidão dimensional são críticas, como a eletrónica e a aeroespacial.
Ao compreender o tamanho e as propriedades dos revestimentos PVD, os compradores podem tomar decisões informadas sobre a sua adequação a aplicações específicas, garantindo um desempenho e uma longevidade óptimos.
Quadro de resumo:
Aspeto-chave | Detalhes |
---|---|
Gama de espessuras típicas | 0,25 microns a 5 microns |
Aplicações | Joalharia (0,25-5 microns), Industrial (tão baixo quanto 3 nanómetros) |
Comparação com CVD | Mais fino (5-10 microns para CVD), mais duro e mais resistente à corrosão |
Durabilidade | 10 anos a centenas de anos, consoante o substrato e as condições |
Vantagens | Elevada dureza, resistência à corrosão, desempenho a altas temperaturas |
Processo de produção | Evaporação e pulverização catódica |
Importância da finura | Mantém as especificações da peça, ideal para aplicações de precisão |
Pronto para melhorar as suas aplicações com revestimentos PVD? Contacte-nos hoje para saber mais!