Os revestimentos PVD (Deposição Física de Vapor) são conhecidos pela sua elevada dureza, que varia normalmente entre 1500 HV (Dureza Vickers) e 4500 HV, dependendo do tipo de revestimento, do material do substrato e do método PVD utilizado. A título de comparação, os aços-carbono têm uma dureza de cerca de 250 HV, enquanto os aços nitretados ou niquelados/cromados variam entre 600 HV e 1000 HV. Os revestimentos PVD, como o TiN (nitreto de titânio), são particularmente apreciados pela sua capacidade de melhorar a resistência ao desgaste, a resistência à corrosão e a durabilidade. Nalguns casos, os revestimentos especializados, como o DLC (Diamond-Like Carbon), podem atingir valores de dureza tão elevados como 9000 HV. A dureza dos revestimentos PVD é um fator crítico no seu desempenho, tornando-os adequados para aplicações exigentes em indústrias como a automóvel, a aeroespacial e a médica.
Explicação dos pontos principais:
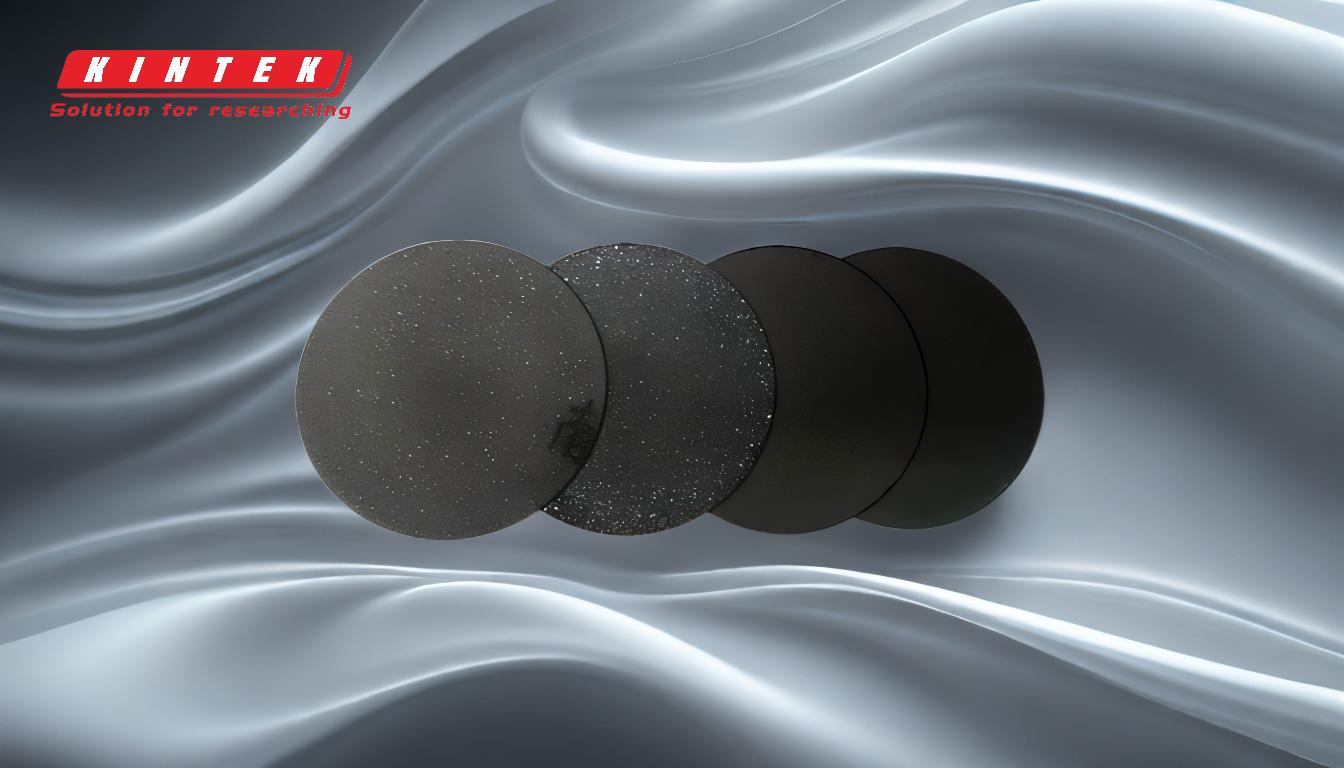
-
Gama de dureza dos revestimentos PVD:
- Os revestimentos PVD têm normalmente uma gama de dureza de 1500 HV a 4500 HV dependendo do material de revestimento e do processo específicos.
- Para referência, 900 HV corresponde a 67 HRC (Rockwell C) o que é significativamente mais duro do que muitos materiais comuns, como o aço-carbono (250 HV) ou os aços nitretados (600-1000 HV).
- Revestimentos especializados, tais como DLC (Diamond-Like Carbon) podem alcançar valores de dureza ainda mais elevados, atingindo até 9000 HV .
-
Factores que influenciam a dureza:
-
A dureza dos revestimentos PVD depende de vários factores:
- Material do revestimento: Diferentes materiais (por exemplo, TiN, TiCN, CrN, DLC) têm níveis de dureza variáveis.
- Material do substrato: O material subjacente pode influenciar as propriedades do revestimento. Por exemplo, os revestimentos de TiN sobre a liga Ti-6Al-4V melhoram os limites de fadiga e a resistência.
- Método PVD: O processo PVD específico (por exemplo, pulverização catódica, evaporação por arco) e as competências do operador podem afetar a dureza do revestimento.
- Espessura: Os revestimentos PVD são muito finos (0,5-5 microns), mas a sua dureza é optimizada para o desempenho.
-
A dureza dos revestimentos PVD depende de vários factores:
-
Comparação com outros materiais:
- Aços ao carbono: Normalmente, têm uma dureza de cerca de 250 HV (25 HRC) .
- Aços nitretados ou niquelados/cromados: Varia entre 600 HV e 1000 HV .
- Revestimentos PVD: A 1500-4500 HV os revestimentos PVD são significativamente mais duros, o que os torna ideais para aplicações que exigem elevada resistência ao desgaste e durabilidade.
-
Aplicações e vantagens:
- Os revestimentos PVD são amplamente utilizados em sectores como automóvel, aeroespacial e médica devido à sua elevada dureza, resistência ao desgaste e resistência à corrosão.
- Também proporcionam baixa fricção e aparência estética melhorada tornando-os adequados para fins funcionais e decorativos.
-
Dureza e resistência ao desgaste:
- Embora uma dureza elevada esteja geralmente relacionada com maior resistência ao desgaste não existe uma relação direta entre os dois. Valores de dureza acima do limiar ótimo podem indicar descarbonetação o que pode reduzir o desempenho.
- Os revestimentos PVD estabelecem um equilíbrio entre a dureza e outras propriedades como tenacidade e adesão para garantir uma durabilidade a longo prazo.
-
Revestimentos especializados:
- Revestimentos DLC: Estes estão entre os revestimentos PVD mais duros, com valores de dureza que atingem até 9000 HV . São particularmente apreciados pelo seu baixo atrito e excelente resistência ao desgaste .
- Revestimentos TiN: Utilizados habitualmente pelo seu aspeto dourado e elevada dureza, são ideais para ferramentas de corte, moldes e aplicações decorativas.
-
Medição da dureza:
- A dureza é normalmente medida usando o método Dureza Vickers (HV) que é adequada para revestimentos finos. Para comparação, Rockwell C (HRC) também é utilizada, com 900 HV equivalente a 67 HRC.
-
Dureza e resistência à corrosão óptimas:
- Os revestimentos PVD atingem um nível ótimo de dureza que aumenta a sua resistência à corrosão . Uma dureza excessiva pode levar à formação de fases duras, o que pode comprometer o desempenho.
Em resumo, a dureza dos revestimentos PVD é uma propriedade fundamental que os torna altamente duráveis e adequados para aplicações exigentes. A sua dureza varia entre 1500 HV e 4500 HV, com revestimentos especializados como o DLC a atingirem até 9000 HV. Esta dureza excecional, combinada com resistência ao desgaste, resistência à corrosão e baixa fricção, torna os revestimentos PVD inestimáveis em várias indústrias.
Tabela de resumo:
Aspeto | Detalhes |
---|---|
Gama de dureza | 1500-4500 HV (até 9000 HV para revestimentos DLC) |
Materiais de comparação | Aço carbono: 250 HV; Aços nitretados: 600-1000 HV |
Principais vantagens | Elevada resistência ao desgaste, resistência à corrosão, baixa fricção e durabilidade |
Aplicações | Utilizações nos sectores automóvel, aeroespacial, médico e decorativo |
Revestimentos especializados | TiN (nitreto de titânio), DLC (carbono-diamante) |
Medição | Dureza Vickers (HV); 900 HV = 67 HRC |
Saiba como os revestimentos PVD podem melhorar o desempenho dos seus materiais- contacte os nossos especialistas hoje mesmo !