Os revestimentos PVD (Physical Vapor Deposition) e DLC (Diamond-Like Carbon) são ambas tecnologias avançadas de tratamento de superfícies, mas diferem significativamente na sua composição, aplicação e caraterísticas de desempenho.PVD é um termo geral para uma variedade de processos de revestimento que depositam películas finas de materiais, incluindo metais, ligas e cerâmicas, sobre um substrato num ambiente de vácuo.O DLC, por outro lado, é um tipo específico de revestimento que consiste numa forma de carbono amorfo com propriedades semelhantes às do diamante, tais como elevada dureza e baixa fricção.Embora o PVD possa ser utilizado para aplicar uma vasta gama de materiais, os revestimentos DLC são especificamente concebidos para proporcionar uma resistência excecional ao desgaste, baixa fricção e elevada dureza, o que os torna ideais para aplicações que exigem durabilidade e desempenho extremos.
Explicação dos pontos principais:
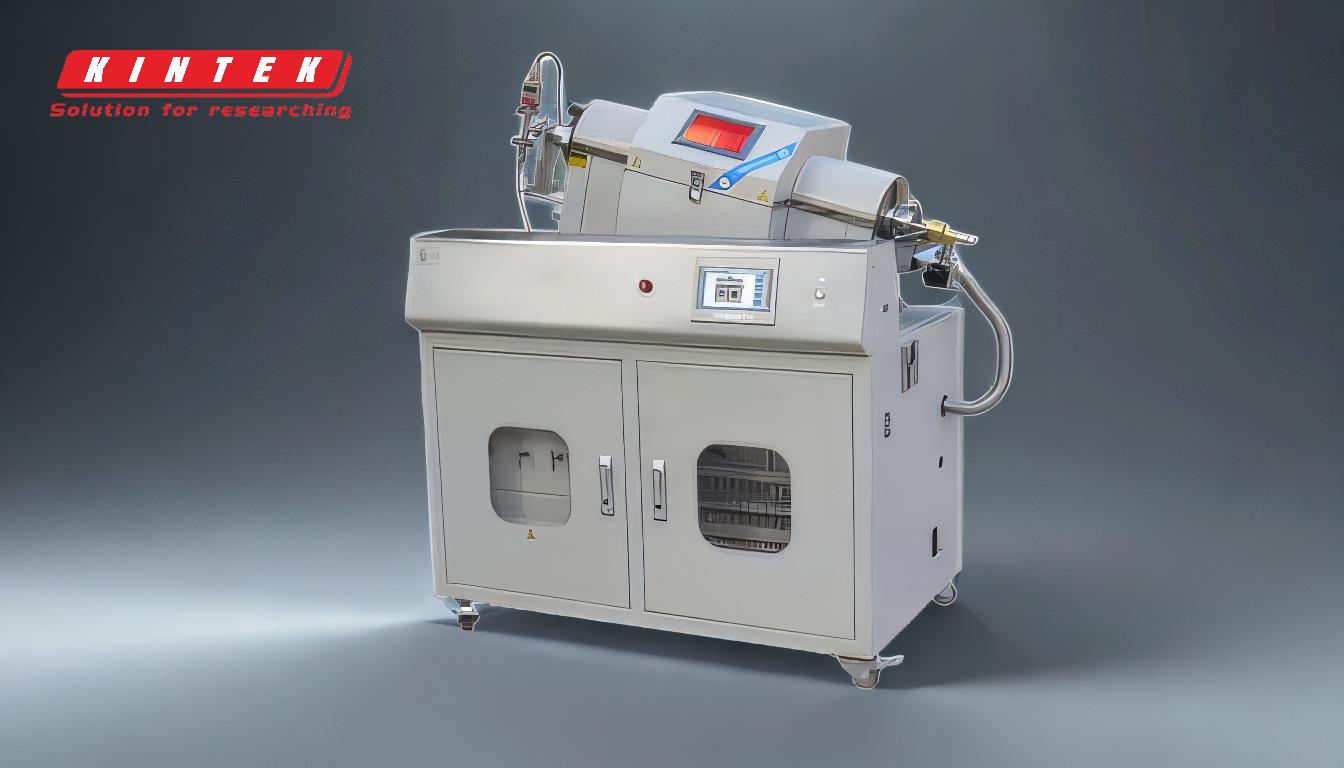
-
Composição e diferenças de material:
- Revestimento PVD:O PVD pode depositar uma vasta gama de materiais, incluindo metais, ligas e cerâmicas.O processo envolve a vaporização física do material de revestimento, que é depois depositado no substrato num ambiente de vácuo.
- Revestimento DLC:O DLC é um tipo específico de revestimento feito de carbono amorfo, que tem propriedades semelhantes às do diamante.Caracteriza-se por uma elevada dureza, baixa fricção e excelente resistência ao desgaste.Os revestimentos DLC são normalmente aplicados utilizando técnicas PVD ou CVD (Chemical Vapor Deposition).
-
Processos de aplicação:
- Revestimento PVD:Os processos PVD ocorrem numa câmara de vácuo a altas temperaturas.O material de revestimento é vaporizado através de métodos físicos, como a pulverização catódica ou a evaporação, e depois depositado no substrato.Este processo permite a aplicação de uma grande variedade de materiais.
- Revestimento DLC:Os revestimentos DLC são normalmente aplicados utilizando técnicas PVD ou CVD.Na PVD, a fonte de carbono é vaporizada e depositada no substrato, enquanto na CVD, é utilizada uma reação química para depositar a película de carbono.Ambos os métodos resultam num revestimento duro e duradouro com propriedades semelhantes às do diamante.
-
Caraterísticas de desempenho:
- Revestimento PVD:Os revestimentos PVD são conhecidos pela sua elevada pureza, uniformidade e excelente aderência ao substrato.São frequentemente mais duros e mais resistentes à corrosão do que os revestimentos aplicados por galvanoplastia.Os revestimentos PVD também oferecem resistência a altas temperaturas e ao impacto, excelente resistência à abrasão e durabilidade.
- Revestimento DLC:Os revestimentos DLC são especificamente concebidos para proporcionar uma resistência excecional ao desgaste, baixa fricção e elevada dureza.Estas propriedades tornam os revestimentos DLC ideais para aplicações que exigem durabilidade e desempenho extremos, como nas indústrias automóvel e aeroespacial.
-
Impacto ambiental:
- Revestimento PVD:O PVD é considerado uma alternativa mais amiga do ambiente aos processos de revestimento tradicionais, como a cromagem.Produz revestimentos duráveis e de longa duração sem gerar substâncias tóxicas, o que o torna uma escolha ética para a proteção de peças em veículos e outros produtos.
- Revestimento DLC:Os revestimentos DLC são também amigos do ambiente, uma vez que não produzem subprodutos nocivos durante o processo de revestimento.A utilização de revestimentos DLC pode reduzir a necessidade de lubrificantes e outros tipos de manutenção, contribuindo ainda mais para a sustentabilidade ambiental.
-
Aplicações:
- Revestimento PVD:Os revestimentos PVD são utilizados numa vasta gama de aplicações, incluindo revestimentos de película fina para energia fotovoltaica, dispositivos semicondutores, dispositivos de visão, investigação e dispositivos médicos, investigação sobre corrosão, revestimentos antirreflexo, estudos de interações interfaciais, aplicações aeroespaciais e automóveis de elevado desempenho e deposição de película em vários substratos, incluindo polímeros.
- Revestimento DLC:Os revestimentos DLC são particularmente úteis em aplicações que requerem extrema durabilidade e desempenho, tais como componentes automóveis (por exemplo, peças de motor, componentes de transmissão), ferramentas de corte e dispositivos médicos.O baixo atrito e a elevada dureza dos revestimentos DLC tornam-nos ideais para reduzir o desgaste e prolongar a vida útil de componentes críticos.
Em resumo, embora os revestimentos PVD e DLC ofereçam soluções avançadas de tratamento de superfícies, diferem na sua composição, processos de aplicação e caraterísticas de desempenho.Os revestimentos PVD são versáteis e podem ser utilizados para aplicar uma vasta gama de materiais, enquanto os revestimentos DLC são especificamente concebidos para proporcionar uma excecional resistência ao desgaste, baixa fricção e elevada dureza, o que os torna ideais para aplicações exigentes.Ambos os tipos de revestimento são amigos do ambiente e oferecem vantagens significativas em relação aos métodos de revestimento tradicionais.
Tabela de resumo:
Aspeto | Revestimento PVD | Revestimento DLC |
---|---|---|
Composição | Metais, ligas, cerâmicas | Carbono amorfo com propriedades semelhantes ao diamante |
Processo de aplicação | Vaporização numa câmara de vácuo (pulverização catódica/evaporação) | Técnicas PVD ou CVD para deposição de carbono |
Desempenho | Elevada pureza, uniformidade, resistência à corrosão, durabilidade | Excecional resistência ao desgaste, baixa fricção, elevada dureza |
Impacto ambiental | Amigo do ambiente, sem subprodutos tóxicos | Amigo do ambiente, reduz a necessidade de lubrificantes |
Aplicações | Fotovoltaica, semicondutores, dispositivos médicos, aeroespacial, automóvel | Componentes automóveis, ferramentas de corte, dispositivos médicos |
Precisa de ajuda para escolher o revestimento certo para a sua aplicação? Contacte os nossos especialistas hoje para um aconselhamento personalizado!