CVD (Deposição Química de Vapor) e PVD (Deposição Física de Vapor) são duas técnicas de revestimento amplamente utilizadas para pastilhas, cada uma com processos, propriedades e aplicações distintas. CVD envolve reações químicas em altas temperaturas, produzindo revestimentos densos e uniformes, adequados para aplicações em altas temperaturas e resistentes ao desgaste. O PVD, por outro lado, utiliza processos físicos no vácuo a temperaturas mais baixas, resultando em revestimentos mais finos e menos densos, com excelente adesão e acabamento superficial. A escolha entre CVD e PVD depende de fatores como compatibilidade de materiais, requisitos de aplicação e condições operacionais.
Pontos-chave explicados:
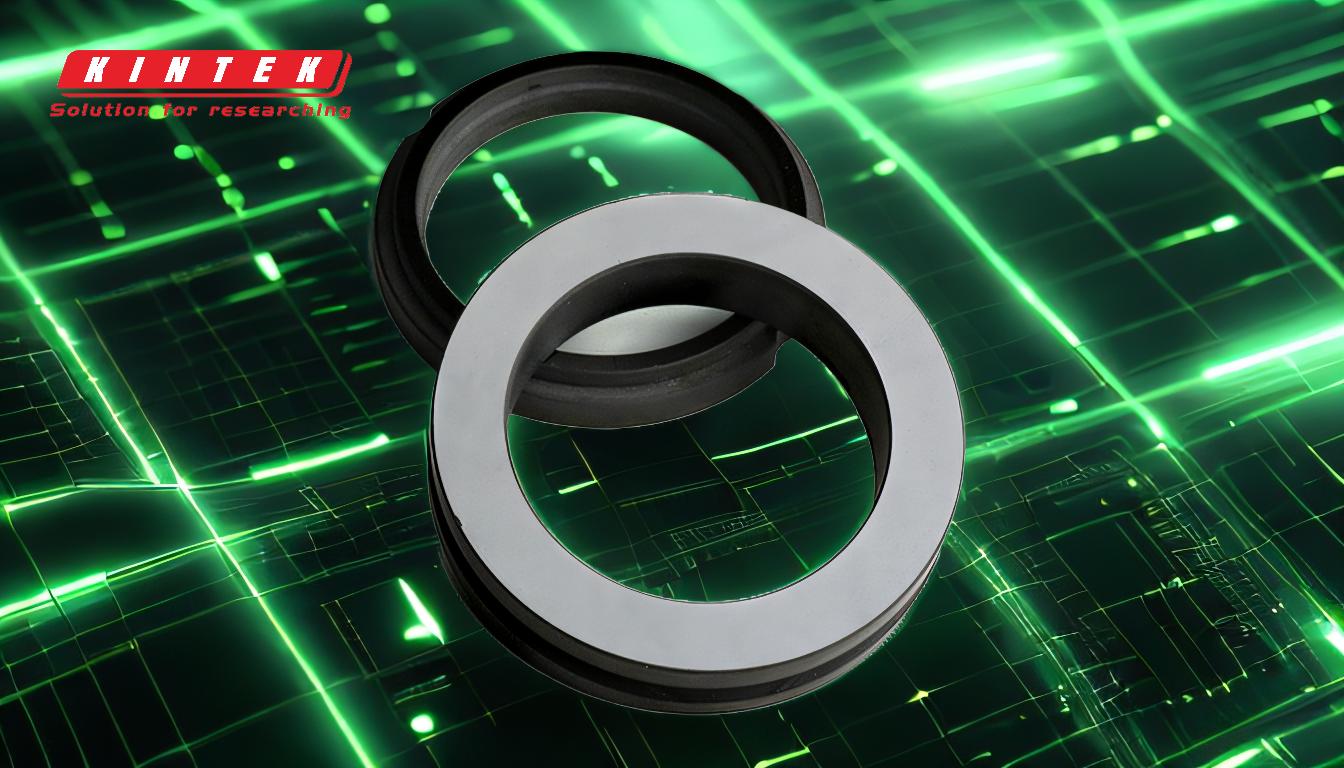
-
Mecanismo de Deposição:
- DCV: Usa reações químicas entre precursores gasosos e o substrato para formar um revestimento sólido. O processo é multidirecional, permitindo cobertura uniforme mesmo em geometrias complexas.
- PVD: Depende de processos físicos, como pulverização catódica ou evaporação, para depositar material no substrato. É um processo de linha de visão, o que significa que apenas as superfícies diretamente expostas à fonte são revestidas.
-
Temperaturas operacionais:
- DCV: Opera em altas temperaturas (450°C a 1050°C), o que pode causar tensões de tração e fissuras finas no revestimento. Isso o torna adequado para aplicações de alta temperatura.
- PVD: Opera em temperaturas mais baixas (250°C a 450°C), reduzindo o estresse térmico e tornando-o adequado para substratos sensíveis à temperatura.
-
Materiais de revestimento:
- DCV: Normalmente limitado a cerâmicas e polímeros devido à natureza química do processo.
- PVD: Pode depositar uma gama mais ampla de materiais, incluindo metais, ligas e cerâmicas, oferecendo maior versatilidade.
-
Propriedades de revestimento:
- DCV: Produz revestimentos mais densos e uniformes, ideais para aplicações que exigem alta resistência ao desgaste e estabilidade térmica.
- PVD: Resulta em revestimentos menos densos e menos uniformes, mas oferece adesão e acabamento superficial superiores, tornando-o adequado para aplicações de precisão.
-
Velocidade e Espessura da Aplicação:
- DCV: Demora mais para aplicar devido ao processo de reação química, mas pode produzir revestimentos mais espessos (10~20μm).
- PVD: Mais rápido de aplicar, mas normalmente resulta em revestimentos mais finos (3~5μm), que são suficientes para muitas aplicações de precisão.
-
Estresse e rachaduras:
- DCV: Altas temperaturas de processamento podem causar tensões de tração e rachaduras finas, o que pode afetar a durabilidade do revestimento.
- PVD: Forma tensões de compressão durante o resfriamento, reduzindo a probabilidade de rachaduras e melhorando a durabilidade do revestimento.
-
Aplicativos:
- DCV: Comumente usado em aplicações de alta temperatura e resistentes ao desgaste, como ferramentas de corte e componentes aeroespaciais.
- PVD: Preferido para aplicações que exigem excelente acabamento superficial e adesão, como dispositivos médicos e ferramentas de usinagem de precisão.
Compreender essas diferenças ajuda na seleção do método de revestimento apropriado com base nos requisitos específicos da aplicação.
Tabela Resumo:
Aspecto | DCV | PVD |
---|---|---|
Mecanismo de Deposição | Reações químicas, cobertura multidirecional | Processos físicos, cobertura de linha de visão |
Temperatura operacional | Alta (450°C a 1050°C), adequada para aplicações de alta temperatura | Inferior (250°C a 450°C), ideal para substratos sensíveis à temperatura |
Materiais de revestimento | Limitado a cerâmicas e polímeros | Ampla gama, incluindo metais, ligas e cerâmicas |
Propriedades de revestimento | Densa, uniforme, alta resistência ao desgaste, estabilidade térmica | Mais fino, menos denso, adesão superior, excelente acabamento superficial |
Velocidade do aplicativo | Revestimentos mais lentos e mais espessos (10~20μm) | Revestimentos mais rápidos e mais finos (3~5μm) |
Estresse e rachaduras | Tensão de tração, possíveis fissuras finas | Tensão compressiva, redução de fissuras |
Aplicativos | Alta temperatura, resistente ao desgaste (por exemplo, ferramentas de corte, aeroespacial) | Aplicações de precisão (por exemplo, dispositivos médicos, ferramentas de usinagem) |
Ainda não tem certeza de qual revestimento é adequado para suas pastilhas? Contate nossos especialistas hoje para aconselhamento personalizado!