Os revestimentos PVD (Physical Vapor Deposition) são conhecidos pela sua dureza, resistência ao desgaste e durabilidade, tornando-os altamente resistentes a riscos em muitas condições.No entanto, não são totalmente à prova de riscos.A resistência ao risco dos revestimentos PVD depende de factores como o tipo de material de revestimento, o substrato em que é aplicado e as condições ambientais.Embora os revestimentos PVD melhorem significativamente a dureza da superfície e a resistência ao desgaste dos materiais, podem ainda ser riscados por substâncias mais duras ou sob tensão mecânica extrema.A sua espessura (0,5-5 microns) e a elevada adesão ao substrato contribuem para a sua durabilidade, mas não são imunes a todas as formas de abrasão ou danos.
Pontos-chave explicados:
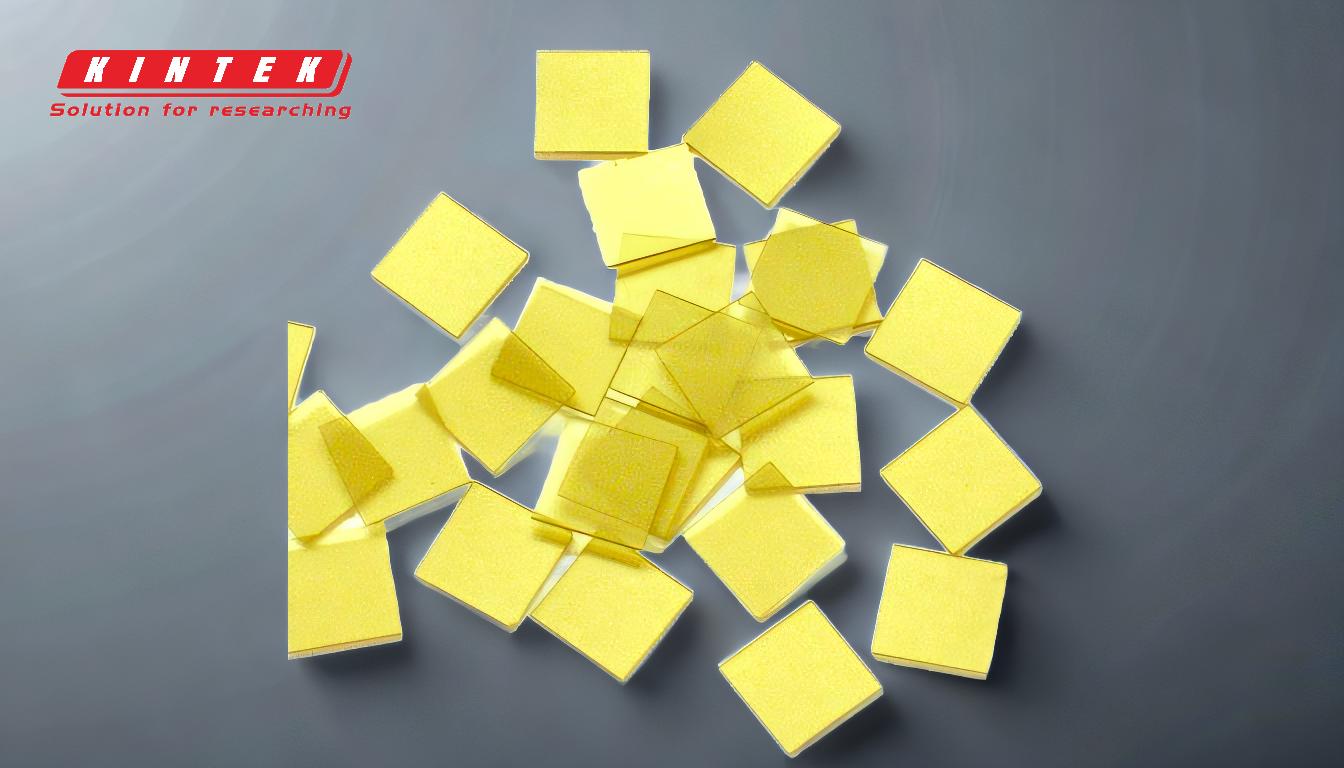
-
Os revestimentos PVD são altamente resistentes a riscos, mas não à prova de riscos
- Os revestimentos PVD são conhecidos pela sua elevada dureza, o que os torna resistentes a riscos e ao desgaste.No entanto, o termo "à prova de riscos" implica uma imunidade total aos riscos, o que não é o caso.
- A dureza dos revestimentos PVD, frequentemente medida na escala de Vickers, torna-os mais resistentes aos riscos do que muitos materiais não tratados.Por exemplo, os revestimentos como o TiN (nitreto de titânio) e o CrN (nitreto de crómio) são excecionalmente duros e resistentes.
- Apesar da sua dureza, os revestimentos PVD podem ainda ser riscados por materiais ou objectos mais duros do que o próprio revestimento, como diamantes ou certas cerâmicas.
-
A espessura e a aderência contribuem para a durabilidade
- Os revestimentos PVD são extremamente finos, variando entre 0,5 e 5 microns.Esta espessura permite-lhes reproduzir o acabamento original do substrato, proporcionando simultaneamente uma camada protetora.
- A excelente aderência dos revestimentos PVD ao substrato garante que o revestimento permanece intacto em condições normais de desgaste, reduzindo a probabilidade de riscos.
- No entanto, a espessura fina também significa que o revestimento tem uma profundidade limitada, pelo que a abrasão repetida ou as forças de alto impacto podem acabar por desgastar o revestimento.
-
O material e o substrato influenciam a resistência a riscos
- A resistência a riscos de um revestimento PVD é influenciada pelo material utilizado para o revestimento e pelo substrato em que é aplicado.Por exemplo, os revestimentos de TiN são mais duros e mais resistentes aos riscos do que alguns outros revestimentos.
- O material do substrato também desempenha um papel importante.Um substrato mais duro proporcionará um melhor suporte para o revestimento PVD, aumentando a sua resistência global aos riscos.
- Nalguns casos, a combinação de um revestimento PVD com um substrato específico pode melhorar significativamente o limite de fadiga e a resistência do material, como se viu com os revestimentos TiN na liga Ti-6Al-4V.
-
Factores ambientais e de aplicação
- O ambiente em que o material revestido é utilizado afecta a sua resistência aos riscos.Por exemplo, a exposição a partículas abrasivas ou a produtos químicos agressivos pode reduzir a eficácia do revestimento ao longo do tempo.
- Os revestimentos PVD são ideais para aplicações em indústrias como a automóvel, a aeroespacial e a médica, onde a resistência ao desgaste e a durabilidade são fundamentais.No entanto, em condições extremas, até os revestimentos PVD podem ficar comprometidos.
- O desempenho do revestimento em geometrias complexas, como a parte posterior e lateral das ferramentas, pode ser menos eficaz devido a limitações no processo de deposição, que podem afetar a resistência a riscos nessas áreas.
-
Vantagens e limitações
-
Vantagens:
- Elevada dureza e resistência ao desgaste.
- Excelente aderência ao substrato.
- Resistência à corrosão e à oxidação.
- Aspeto estético melhorado sem necessidade de polimento adicional.
-
Limitações:
- Não é totalmente à prova de riscos, especialmente contra materiais mais duros.
- Os revestimentos finos podem desgastar-se em condições extremas.
- O desempenho pode variar em geometrias complexas ou superfícies irregulares.
-
Vantagens:
-
Aplicações onde a resistência aos riscos é importante
-
Os revestimentos PVD são amplamente utilizados em indústrias onde a resistência a riscos é crítica, tais como
- Automóvel:Para componentes como anéis de pistão e peças de motor.
- Aeroespacial:Para lâminas de turbinas e outros componentes sujeitos a grandes tensões.
- Médico:Para instrumentos cirúrgicos e implantes.
- Bens de consumo:Para caixas de relógios, molduras de smartphones e artigos decorativos.
- Nestas aplicações, os revestimentos PVD proporcionam um equilíbrio entre durabilidade, estética e funcionalidade, embora não sejam imunes a todas as formas de danos.
-
Os revestimentos PVD são amplamente utilizados em indústrias onde a resistência a riscos é crítica, tais como
Em conclusão, embora os revestimentos PVD sejam altamente resistentes a riscos devido à sua dureza, resistência ao desgaste e excelente aderência, não são completamente à prova de riscos.O seu desempenho depende do material do revestimento, do substrato e das condições ambientais.Para a maioria das aplicações práticas, os revestimentos PVD oferecem uma proteção significativa contra riscos e desgaste, tornando-os uma escolha valiosa para aumentar a durabilidade e longevidade de vários materiais e componentes.
Tabela de resumo:
Aspeto-chave | Detalhes |
---|---|
Resistência aos riscos | Altamente resistente, mas não à prova de riscos; depende do material e do substrato. |
Espessura do revestimento | 0,5-5 microns, proporcionando durabilidade e mantendo o acabamento do substrato. |
Adesão | A excelente aderência garante uma proteção duradoura em condições normais. |
Influência do material | Os revestimentos TiN e CrN oferecem uma dureza e resistência a riscos superiores. |
Factores ambientais | Condições adversas ou partículas abrasivas podem reduzir a eficácia. |
Aplicações | Indústrias automóvel, aeroespacial, médica e de bens de consumo. |
Vantagens | Elevada dureza, resistência ao desgaste, resistência à corrosão e atrativo estético. |
Limitações | Não é totalmente à prova de riscos; os revestimentos finos podem desgastar-se sob tensão extrema. |
Saiba como os revestimentos PVD podem aumentar a durabilidade do seu produto- contacte os nossos especialistas hoje mesmo !