Os revestimentos PVD (Physical Vapor Deposition) são de facto resistentes ao calor, o que os torna adequados para aplicações em que as temperaturas elevadas são uma preocupação.Estes revestimentos são conhecidos pela sua elevada dureza, resistência ao desgaste e resistência à corrosão, o que contribui para a sua capacidade de suportar temperaturas elevadas.Os revestimentos PVD são aplicados num ambiente de vácuo, resultando numa camada fina e duradoura que adere bem ao substrato.A sua estabilidade térmica, combinada com propriedades como a baixa fricção e a estabilidade química, torna-os ideais para indústrias como a automóvel, a aeroespacial e a médica, onde a resistência ao calor é fundamental.Embora os revestimentos PVD não sejam imunes a todas as condições de alta temperatura, o seu desempenho é geralmente superior ao de muitos outros métodos de revestimento.
Pontos-chave explicados:
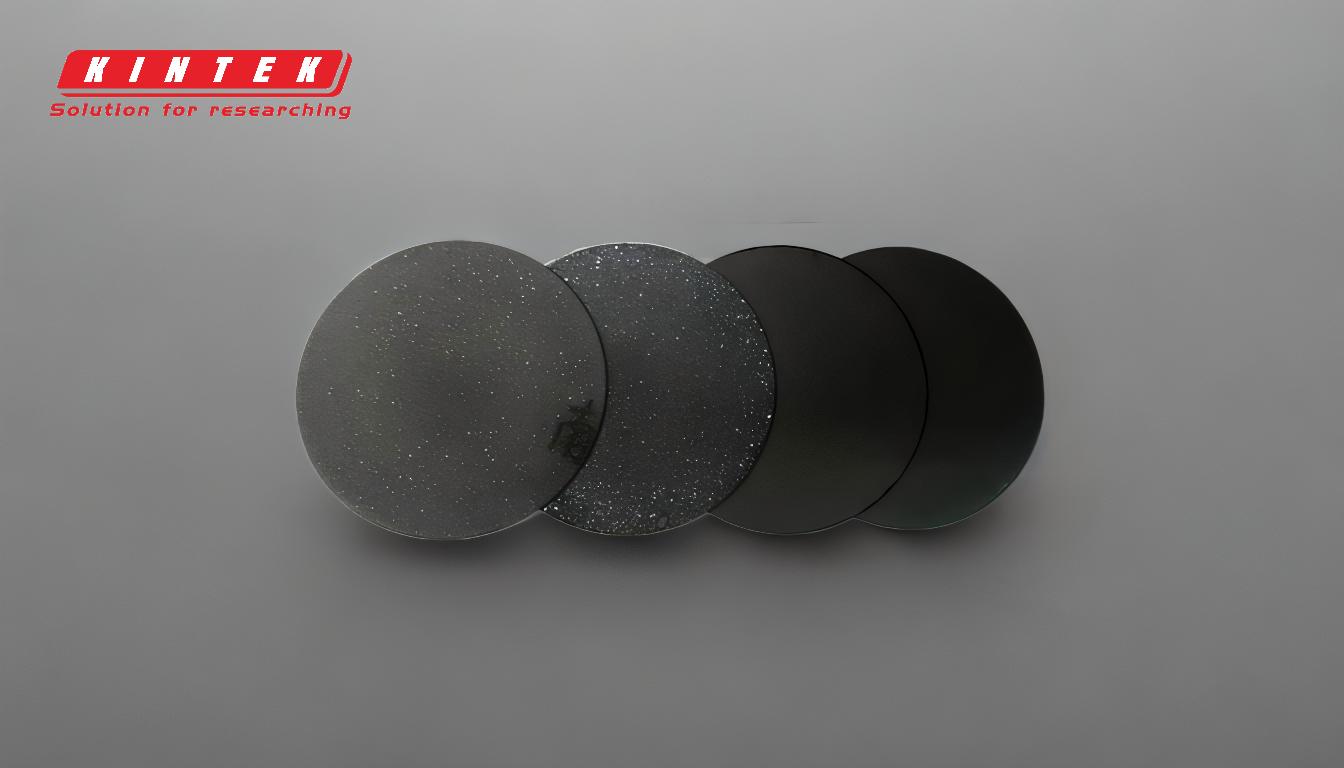
-
Resistência ao calor dos revestimentos PVD:
- Os revestimentos PVD apresentam uma excelente resistência ao calor devido à sua elevada dureza e estabilidade química.Estas propriedades permitem-lhes manter a integridade estrutural e o desempenho mesmo a temperaturas elevadas.
- Os revestimentos são frequentemente utilizados em ambientes de alta temperatura, como em motores de automóveis ou componentes aeroespaciais, onde têm de suportar o stress térmico sem se degradarem.
-
Natureza fina e durável:
- Os revestimentos PVD são extremamente finos, variando de 0,5 a 5 microns, mas a sua durabilidade é excecional.Esta espessura não compromete a sua capacidade de resistência ao calor, uma vez que os materiais utilizados em PVD (por exemplo, TiN, CrN) são inerentemente resistentes ao calor.
- A adesão dos revestimentos ao substrato é forte, garantindo que permanecem intactos mesmo sob ciclos térmicos ou tensão mecânica.
-
Aplicações em ambientes de alta temperatura:
-
Os revestimentos PVD são amplamente utilizados em indústrias onde a resistência ao calor é crítica.Por exemplo:
- Automóvel:Em componentes de motores como pistões e válvulas, onde são comuns temperaturas elevadas e fricção.
- Aeroespacial:Nas lâminas das turbinas e noutras peças expostas a um calor extremo durante o funcionamento.
- Médico:Em instrumentos cirúrgicos que são submetidos a esterilizações repetidas a altas temperaturas.
-
Os revestimentos PVD são amplamente utilizados em indústrias onde a resistência ao calor é crítica.Por exemplo:
-
Comparação com outros métodos de revestimento:
- Os revestimentos PVD superam muitos dos métodos de revestimento tradicionais, como a galvanoplastia, em termos de resistência ao calor.São mais duros, mais resistentes à corrosão e mais adequados para aplicações a altas temperaturas.
- Ao contrário de alguns revestimentos que se podem degradar ou oxidar a altas temperaturas, os revestimentos PVD mantêm as suas propriedades, o que os torna uma escolha fiável para ambientes exigentes.
-
Limitações dos revestimentos PVD na resistência ao calor:
- Embora os revestimentos PVD sejam resistentes ao calor, o seu desempenho pode ser influenciado pelo material do substrato e pelo processo PVD específico utilizado.Por exemplo, os revestimentos de determinadas ligas podem ter um melhor desempenho sob tensão térmica do que outros.
- A espessura do revestimento, embora benéfica para muitas propriedades, pode também limitar a sua capacidade de fornecer proteção a longo prazo em ambientes de temperatura extremamente elevada sem um suporte de substrato adequado.
-
Desempenho específico do material:
-
A resistência ao calor dos revestimentos PVD pode variar consoante os materiais utilizados.Por exemplo:
- TiN (nitreto de titânio):Conhecido pela sua elevada dureza e estabilidade térmica, tornando-o ideal para aplicações a altas temperaturas.
- CrN (Nitreto de Crómio):Oferece uma excelente resistência à oxidação e é normalmente utilizado em ambientes com temperaturas elevadas.
- A escolha do material de revestimento pode ser adaptada a requisitos específicos de resistência ao calor.
-
A resistência ao calor dos revestimentos PVD pode variar consoante os materiais utilizados.Por exemplo:
-
Vantagens adicionais que contribuem para a resistência ao calor:
-
Os revestimentos PVD fornecem outras propriedades que aumentam indiretamente a sua resistência ao calor:
- Resistência ao desgaste:Reduz a perda de material devido à fricção, o que é crucial em aplicações de alta temperatura.
- Resistência à corrosão:Protege o substrato contra a oxidação e a degradação química, que pode ser agravada pelo calor.
- Baixa fricção:Minimiza a geração de calor devido à fricção, melhorando ainda mais o desempenho do revestimento em ambientes de alta temperatura.
-
Os revestimentos PVD fornecem outras propriedades que aumentam indiretamente a sua resistência ao calor:
Em resumo, os revestimentos PVD são resistentes ao calor e adequados para aplicações que exigem durabilidade a altas temperaturas.A sua espessura, dureza e estabilidade química fazem deles a escolha preferida em indústrias onde o stress térmico é uma preocupação.No entanto, o seu desempenho pode variar com base no substrato e no material de revestimento específico, pelo que é essencial uma seleção cuidadosa para obter os melhores resultados.
Tabela de resumo:
Propriedade | Descrição |
---|---|
Resistência ao calor | A elevada dureza e a estabilidade química garantem o desempenho a temperaturas elevadas. |
Espessura | 0,5 a 5 microns, oferecendo durabilidade sem comprometer a resistência ao calor. |
Aplicações | Automóvel (peças de motor), aeroespacial (lâminas de turbina), médica (instrumentos cirúrgicos). |
Exemplos de materiais | TiN (nitreto de titânio), CrN (nitreto de crómio). |
Vantagens adicionais | A resistência ao desgaste, a resistência à corrosão e a baixa fricção aumentam a resistência ao calor. |
Descubra como os revestimentos PVD podem melhorar as suas aplicações a altas temperaturas. contacte-nos hoje !