Quando as cerâmicas, em particular as argilas, são cozidas num forno, o carbono e os compostos orgânicos que contêm sofrem um processo chamado oxidação, onde se queimam.Esta combustão é essencial para evitar defeitos no produto final, tais como inchaço ou descoloração, que podem ocorrer se o carbono não for totalmente removido.O processo envolve o aquecimento do material a temperaturas elevadas, normalmente entre 500°C e 900°C, onde o carbono reage com o oxigénio para formar dióxido de carbono e outros gases, que são depois expelidos do forno.Após a cozedura, o material é arrefecido e processado, muitas vezes envolvendo moagem e peletização, antes de ser embalado para transporte.
Pontos-chave explicados:
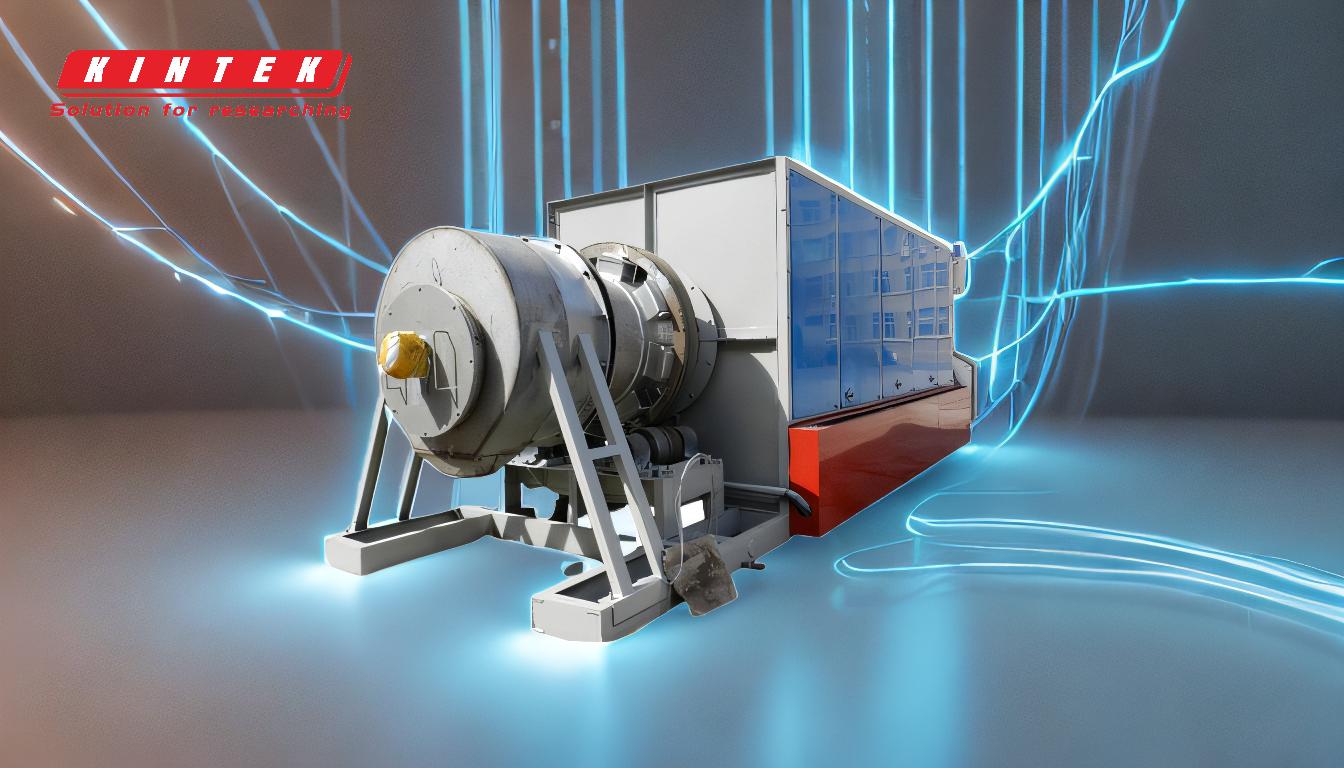
-
Presença de carbono na cerâmica:
- Os materiais cerâmicos, especialmente as argilas, contêm naturalmente carbono e compostos orgânicos.Estes podem ter origem na decomposição de matéria vegetal e animal no solo onde a argila é formada.
-
A necessidade de queimar o carbono:
- Durante o processo de cozedura num forno, é fundamental queimar o carbono e os compostos orgânicos.Se estes não forem removidos, podem causar defeitos nos produtos cerâmicos, tais como inchaço, cortiça negra ou descoloração, que comprometem a integridade estrutural e a qualidade estética do produto final.
-
Processo de oxidação:
- A queima do carbono ocorre através de um processo de oxidação.Este processo envolve o aquecimento do material cerâmico a temperaturas tipicamente entre 500°C e 900°C.A estas temperaturas, o carbono reage com o oxigénio presente na atmosfera do forno para formar dióxido de carbono (CO₂) e outros subprodutos gasosos.
- O processo de oxidação é cuidadosamente controlado para garantir a combustão completa dos materiais carbonáceos.Uma oxidação inadequada pode deixar carbono residual, conduzindo aos defeitos acima mencionados.
-
Complicações durante a cozedura:
- A combustão de carbono e de compostos orgânicos pode produzir complicações durante o processo de cozedura.Estas incluem a libertação de gases que podem causar inchaço ou furos no corpo cerâmico se não forem devidamente ventilados.Além disso, a oxidação rápida pode levar a choques térmicos, potencialmente provocando fissuras nas peças cerâmicas.
-
Processamento pós-queima:
- Depois de o carbono ter sido queimado e o material cerâmico ter sido cozido, o material é arrefecido.Este processo de arrefecimento deve ser controlado para evitar tensões térmicas que possam provocar fissuras.
- Uma vez arrefecido, o material pode ser submetido a um processamento adicional, como a moagem para obter o tamanho de partícula desejado, a peletização para facilitar o manuseamento e o ensacamento para transporte.Isto assegura que o material está pronto para a sua próxima utilização ou para distribuição.
-
Importância do controlo da temperatura:
- A temperatura a que o carbono arde é crítica.Se a temperatura do forno for demasiado baixa, o carbono pode não entrar em combustão total, dando origem a defeitos.Por outro lado, se a temperatura for demasiado elevada, pode causar outros problemas, como a sobreaquecimento, que pode enfraquecer a estrutura cerâmica.
- Os operadores de fornos devem monitorizar e controlar cuidadosamente a temperatura ao longo do ciclo de cozedura para garantir resultados óptimos.
-
Considerações ambientais:
- A libertação de dióxido de carbono e outros gases durante o processo de cozedura tem implicações ambientais.Os fornos modernos estão frequentemente equipados com sistemas de captura e tratamento destas emissões para minimizar o seu impacto ambiental.
- A combustão eficiente do carbono também contribui para reduzir a pegada de carbono global do processo de fabrico de cerâmica.
Em resumo, a queima de carbono num forno é uma etapa crítica no processo de fabrico de cerâmica.Envolve um processo de oxidação cuidadosamente controlado para assegurar a remoção completa do carbono e dos compostos orgânicos, evitando assim defeitos no produto final.O controlo adequado da temperatura, a ventilação e o processamento pós-queima são essenciais para obter cerâmicas de alta qualidade.Além disso, as considerações ambientais desempenham um papel importante na gestão das emissões produzidas durante este processo.
Tabela de resumo:
Aspeto-chave | Detalhes |
---|---|
Presença de carbono | As cerâmicas, especialmente as argilas, contêm carbono proveniente da matéria orgânica decomposta. |
Necessidade de queimar o carbono | Evita defeitos como inchaço, descoloração e cortiça negra. |
Processo de oxidação | O carbono reage com o oxigénio a 500°C-900°C para formar CO₂, assegurando a combustão. |
Complicações durante a queima | A libertação de gás pode causar inchaço ou fissuras se não for devidamente ventilado. |
Processamento pós-queima | O arrefecimento, a moagem, a peletização e a embalagem garantem a prontidão do material. |
Controlo da temperatura | Crítico para evitar a queima insuficiente ou excessiva, que pode enfraquecer a cerâmica. |
Impacto ambiental | As emissões são geridas para reduzir a pegada de carbono da produção de cerâmica. |
Assegurar uma cerâmica de alta qualidade com soluções de cozedura especializadas- contacte-nos hoje para mais informações!