CVD (Deposição Química de Vapor) e PVD (Deposição Física de Vapor) são duas técnicas de deposição de filme fino amplamente utilizadas, cada uma com seu próprio conjunto de vantagens e limitações. A escolha entre CVD e PVD depende da aplicação específica, dos requisitos de materiais e das restrições operacionais. O CVD é mais adequado para aplicações que exigem revestimentos uniformes em geometrias complexas e ambientes de alta temperatura, enquanto o PVD é ideal para materiais sensíveis à temperatura e aplicações que necessitam de taxas de deposição mais rápidas. Abaixo, exploramos as principais diferenças, vantagens e limitações de ambos os métodos para ajudar a determinar qual é o melhor para casos de uso específicos.
Pontos-chave explicados:
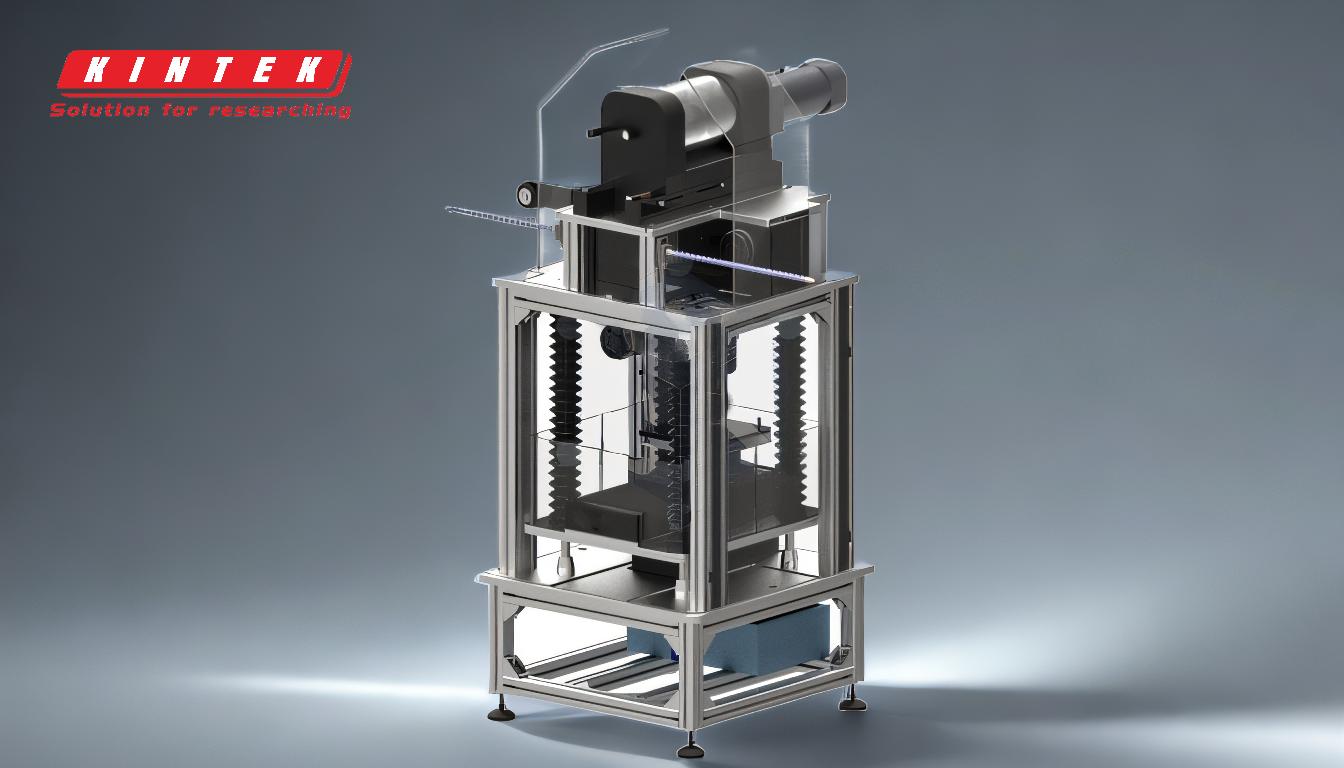
-
Mecanismo de Deposição:
- DCV: Envolve reações químicas entre precursores gasosos e a superfície do substrato, formando um revestimento sólido. Este processo é multidirecional, permitindo cobertura uniforme mesmo em geometrias complexas e furos profundos.
- PVD: Depende de processos físicos como pulverização catódica ou evaporação para depositar materiais sólidos no substrato. É um processo de linha de visão, o que significa que é menos eficaz para revestir áreas sombreadas ou formas complexas.
-
Temperaturas operacionais:
- DCV: Opera em temperaturas mais altas (450°C a 1050°C), tornando-o inadequado para materiais sensíveis à temperatura, como certos polímeros ou substratos de baixo ponto de fusão.
- PVD: Opera em temperaturas mais baixas (250°C a 450°C), tornando-o uma melhor escolha para materiais sensíveis à temperatura.
-
Gama de materiais de revestimento:
- DCV: Usado principalmente para depositar cerâmicas e polímeros. Pode utilizar compostos químicos voláteis, possibilitando a deposição de elementos de difícil evaporação.
- PVD: Pode depositar uma gama mais ampla de materiais, incluindo metais, ligas e cerâmicas, tornando-o mais versátil para diversas aplicações.
-
Uniformidade e densidade do revestimento:
- DCV: Produz revestimentos mais densos e uniformes devido ao processo de reação química, que garante cobertura completa mesmo em geometrias complexas.
- PVD: Os revestimentos são menos densos e menos uniformes, mas podem ser aplicados mais rapidamente, tornando-os adequados para aplicações onde a velocidade é crítica.
-
Limitações da linha de visão:
- DCV: Não limitado por efeitos de linha de visão, permitindo a deposição de revestimento em furos profundos, áreas sombreadas e geometrias complexas.
- PVD: Limitado pela linha de visão, tornando-o menos eficaz para revestir formas complexas ou áreas não expostas diretamente à fonte de deposição.
-
Consumo de energia e restrições térmicas:
- DCV: Requer elevados custos de energia para aquecer a fase gasosa e o substrato, o que pode ser uma desvantagem em termos de despesas operacionais e impacto ambiental.
- PVD: Opera no vácuo e em temperaturas mais baixas, reduzindo o consumo de energia e tornando-o mais adequado para aplicações sensíveis à temperatura.
-
Aplicativos:
- DCV: Comumente usado na fabricação de semicondutores, optoeletrônica e aplicações que exigem revestimentos uniformes e de alta pureza.
- PVD: Amplamente utilizado em revestimentos decorativos, revestimentos resistentes ao desgaste e aplicações que envolvem materiais sensíveis à temperatura.
-
Desperdício de Materiais:
- DCV: Produz menos desperdício de material, pois apenas a área aquecida é revestida. Técnicas avançadas, como lasers controlados por computador, podem melhorar ainda mais o revestimento seletivo.
- PVD: Pode resultar em mais desperdício de material devido à natureza do processo de deposição física.
-
Espessura e suavidade do filme:
- DCV: Normalmente produz filmes mais espessos e suaves, ideais para aplicações que exigem alta durabilidade e precisão.
- PVD: Produz filmes mais finos e com menos suavidade, adequados para aplicações onde velocidade e versatilidade são priorizadas.
-
Custo e Complexidade:
- DCV: Mais fácil de operar e não requer uma configuração complicada, mas os altos custos de energia e as restrições térmicas podem aumentar as despesas operacionais.
- PVD: Requer um ambiente de vácuo, o que pode aumentar a complexidade e o custo da configuração, mas oferece taxas de deposição mais rápidas e menor consumo de energia.
Concluindo, a escolha entre CVD e PVD depende dos requisitos específicos da aplicação. O CVD é melhor para aplicações de alta temperatura e alta precisão que exigem revestimentos uniformes, enquanto o PVD é mais adequado para materiais sensíveis à temperatura e aplicações que necessitam de taxas de deposição mais rápidas. Ambos os métodos têm vantagens e limitações únicas e a decisão deve basear-se numa avaliação minuciosa dos requisitos operacionais e materiais.
Tabela Resumo:
Aspecto | DCV | PVD |
---|---|---|
Mecanismo de Deposição | Reações químicas, cobertura multidirecional e uniforme | Processos físicos, linha de visão, menos eficazes para formas complexas |
Temperaturas operacionais | Alta (450°C a 1050°C), inadequada para materiais sensíveis à temperatura | Baixo (250°C a 450°C), ideal para materiais sensíveis à temperatura |
Gama de materiais de revestimento | Principalmente cerâmicas e polímeros | Metais, ligas, cerâmicas, maior versatilidade de materiais |
Uniformidade de revestimento | Revestimentos mais densos e uniformes | Menos denso, menos uniforme, mas taxas de deposição mais rápidas |
Linha de visão | Não limitado, eficaz para geometrias complexas | Limitado, menos eficaz para áreas sombreadas |
Consumo de energia | Altos custos de energia devido a altas temperaturas | Menor consumo de energia, opera no vácuo |
Aplicativos | Semicondutores, optoeletrônica, revestimentos de alta pureza | Aplicações decorativas, resistentes ao desgaste e sensíveis à temperatura |
Desperdício de Materiais | Menos desperdício, técnicas de revestimento seletivas | Mais resíduos devido ao processo de deposição física |
Espessura do filme | Filmes mais espessos e suaves | Filmes mais finos e menos lisos |
Custo e Complexidade | Configuração mais fácil, custos operacionais mais elevados | Configuração complexa de vácuo, deposição mais rápida, menores custos de energia |
Ainda não tem certeza de qual técnica de deposição de filme fino é adequada para sua aplicação? Contate nossos especialistas hoje para aconselhamento personalizado!