A PVD (Deposição Física de Vapor) e a galvanoplastia são duas tecnologias de revestimento de superfícies amplamente utilizadas, cada uma com as suas próprias vantagens e limitações.O PVD é geralmente considerado superior em termos de durabilidade, resistência ao desgaste, segurança ambiental e longevidade estética.É mais duro, mais resistente à corrosão e à radiação UV e não necessita de revestimentos de proteção adicionais.A galvanoplastia, embora eficaz para determinadas aplicações, tende a degradar-se com o tempo, a manchar e a libertar substâncias químicas nocivas.O PVD é particularmente preferido em sectores como o aeroespacial, médico e marítimo devido à sua robustez e respeito pelo ambiente.No entanto, a escolha entre PVD e galvanoplastia depende, em última análise, da aplicação específica, do orçamento e das propriedades desejadas do revestimento.
Pontos-chave explicados:
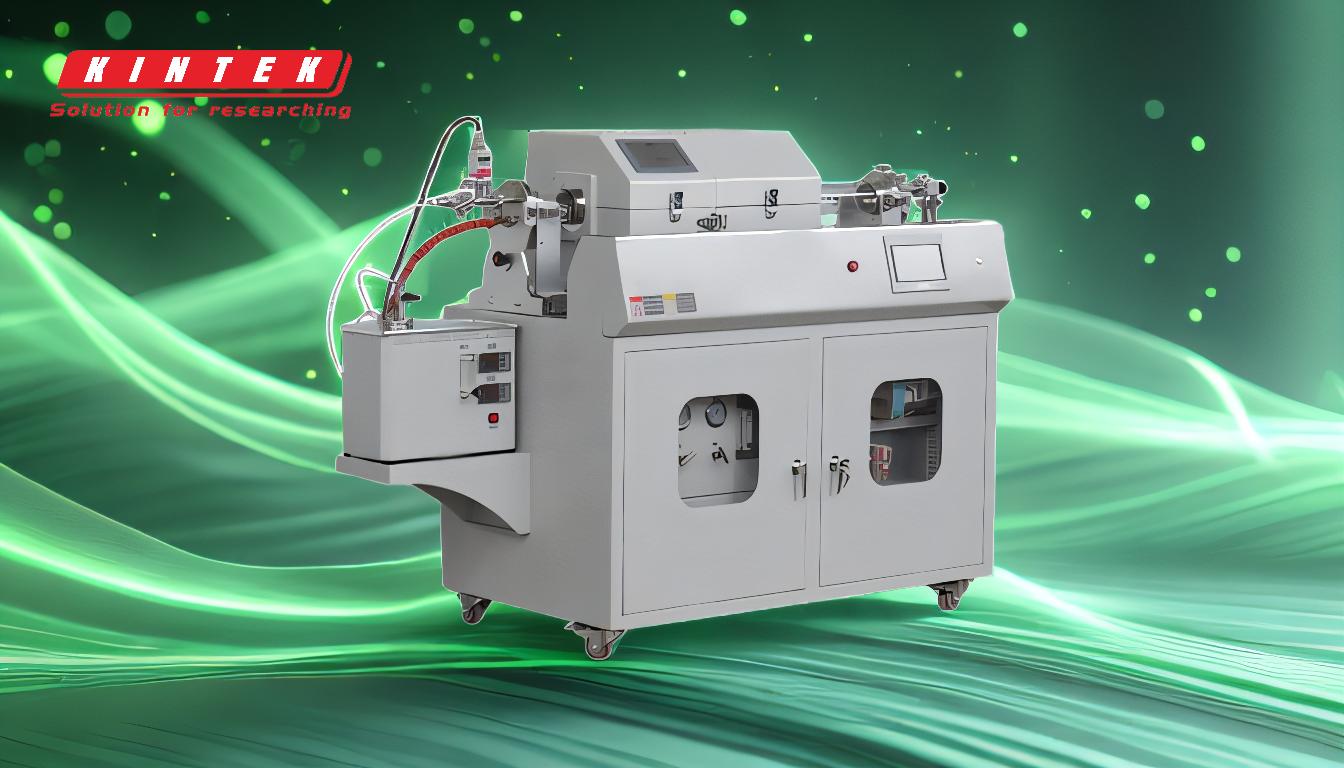
-
Durabilidade e resistência ao desgaste:
- Os revestimentos PVD são significativamente mais duros e mais resistentes ao desgaste em comparação com os revestimentos galvanizados.Isto torna o PVD ideal para aplicações em que a superfície revestida está sujeita a abrasão ou impacto frequentes.
- Os revestimentos galvanizados, embora duráveis, requerem frequentemente uma camada superior transparente que se pode degradar com o tempo, levando a manchas e corrosão.Os revestimentos PVD não requerem essas camadas adicionais, o que os torna inerentemente mais duradouros.
-
Segurança ambiental:
- O PVD é um processo amigo do ambiente que não produz subprodutos nocivos.Esta é uma vantagem significativa em relação à galvanoplastia, que envolve frequentemente a utilização de produtos químicos tóxicos e pode libertar substâncias nocivas para a atmosfera.
- Para as indústrias e aplicações em que o impacto ambiental é uma preocupação, o PVD é a escolha preferida devido ao seu processo de produção mais limpo e seguro.
-
Longevidade estética:
- Os revestimentos PVD mantêm a sua cor e aspeto ao longo do tempo, mesmo sob exposição prolongada à radiação UV.Isto torna-os ideais para aplicações em que o apelo estético é importante, como na eletrónica de consumo ou em artigos decorativos.
- Os revestimentos galvanizados, por outro lado, podem manchar ou descolorir com o tempo, especialmente se a camada protetora transparente se degradar.
-
Resistência à corrosão e aos produtos químicos:
- Os revestimentos PVD são altamente resistentes à corrosão, o que os torna adequados para ambientes agressivos, incluindo aplicações marítimas.Também resistem à água salgada, a riscos e à exposição prolongada à luz ultravioleta.
- Os revestimentos galvanizados, embora ofereçam algum nível de resistência à corrosão, são geralmente menos robustos e podem degradar-se mais rapidamente em ambientes exigentes.
-
Resistência à temperatura e à abrasão:
- Os revestimentos PVD podem suportar temperaturas elevadas e proporcionar uma excelente resistência à abrasão, tornando-os adequados para aplicações de elevado desempenho em sectores como o aeroespacial e os dispositivos médicos.
- Os revestimentos galvanizados podem não oferecer o mesmo nível de desempenho em condições extremas, limitando a sua utilização em ambientes de elevada tensão.
-
Uniformidade e aplicação:
- Os revestimentos PVD são mais uniformes na aparência, proporcionando um acabamento consistente que é difícil de obter com a galvanoplastia.Esta uniformidade é particularmente importante nas indústrias de precisão, onde mesmo pequenas imperfeições podem ser críticas.
- A galvanoplastia pode por vezes resultar em revestimentos irregulares, especialmente em geometrias complexas, o que pode afetar tanto o aspeto como o desempenho do artigo revestido.
-
Custo e manutenção:
- Embora os revestimentos PVD possam ter um custo inicial mais elevado, resultam frequentemente em custos de manutenção mais baixos ao longo do tempo devido à sua durabilidade e resistência ao desgaste e à corrosão.
- Os revestimentos galvânicos, embora potencialmente mais baratos à partida, podem exigir uma manutenção ou substituição mais frequente, conduzindo a custos mais elevados a longo prazo.
-
Aplicações no sector:
- O PVD é amplamente utilizado em sectores que exigem um elevado desempenho e durabilidade, tais como o sector aeroespacial, médico e de alta tecnologia.A sua capacidade de resistir a condições extremas torna-o uma escolha preferencial para aplicações críticas.
- A galvanoplastia continua a ser utilizada em muitas indústrias, especialmente quando o custo é uma preocupação fundamental, mas está a ser cada vez mais substituída pela PVD em aplicações em que o desempenho e a longevidade são mais importantes.
Em resumo, a PVD é geralmente a melhor escolha para aplicações que exigem elevada durabilidade, segurança ambiental e longevidade estética, enquanto a galvanoplastia pode ainda ser adequada para aplicações menos exigentes ou sensíveis ao custo.A decisão deve basear-se nos requisitos específicos do projeto, incluindo as necessidades de desempenho, as considerações ambientais e as restrições orçamentais.
Tabela de resumo:
Aspeto | PVD | Galvanoplastia |
---|---|---|
Durabilidade | Mais duro, mais resistente ao desgaste, sem necessidade de revestimentos adicionais. | Requer uma camada superior transparente; propenso a manchas e corrosão. |
Segurança ambiental | Sem subprodutos nocivos; amigo do ambiente. | Utiliza produtos químicos tóxicos; liberta substâncias nocivas. |
Longevidade estética | Mantém a cor e o aspeto sob exposição aos raios UV. | Manchas/descolorações ao longo do tempo. |
Resistência à corrosão | Altamente resistente à corrosão e a ambientes agressivos. | Menos robusto; degrada-se mais rapidamente em condições difíceis. |
Resistência à temperatura | Resiste a temperaturas elevadas; excelente para ambientes extremos. | Desempenho limitado em condições de tensão elevada. |
Uniformidade | Fornece revestimentos consistentes e uniformes. | Pode resultar em revestimentos irregulares em geometrias complexas. |
Custo | Custo inicial mais elevado, mas menor manutenção ao longo do tempo. | Custo inicial mais barato, mas custos de manutenção a longo prazo mais elevados. |
Aplicações industriais | Indústrias aeroespacial, médica, marítima e de alta tecnologia. | Aplicações sensíveis ao custo em que o desempenho é menos crítico. |
Ainda não tem a certeza de qual a tecnologia de revestimento mais adequada para o seu projeto? Contacte os nossos especialistas hoje para um aconselhamento personalizado!