A fundição em molde cerâmico é um processo de fundição de precisão utilizado para criar peças metálicas complexas e pormenorizadas.Envolve a criação de um molde cerâmico através da aplicação de uma pasta cerâmica num padrão de molde, deixando-a secar e, em seguida, removendo a pasta seca para formar o molde.O molde é depois curado através da eliminação de voláteis por aquecimento a baixa temperatura e endurecido num forno a alta temperatura.Este processo é ideal para produzir peças com detalhes finos, superfícies lisas e elevada precisão dimensional.Segue-se uma descrição detalhada dos principais passos envolvidos na fundição de moldes cerâmicos.
Pontos-chave explicados:
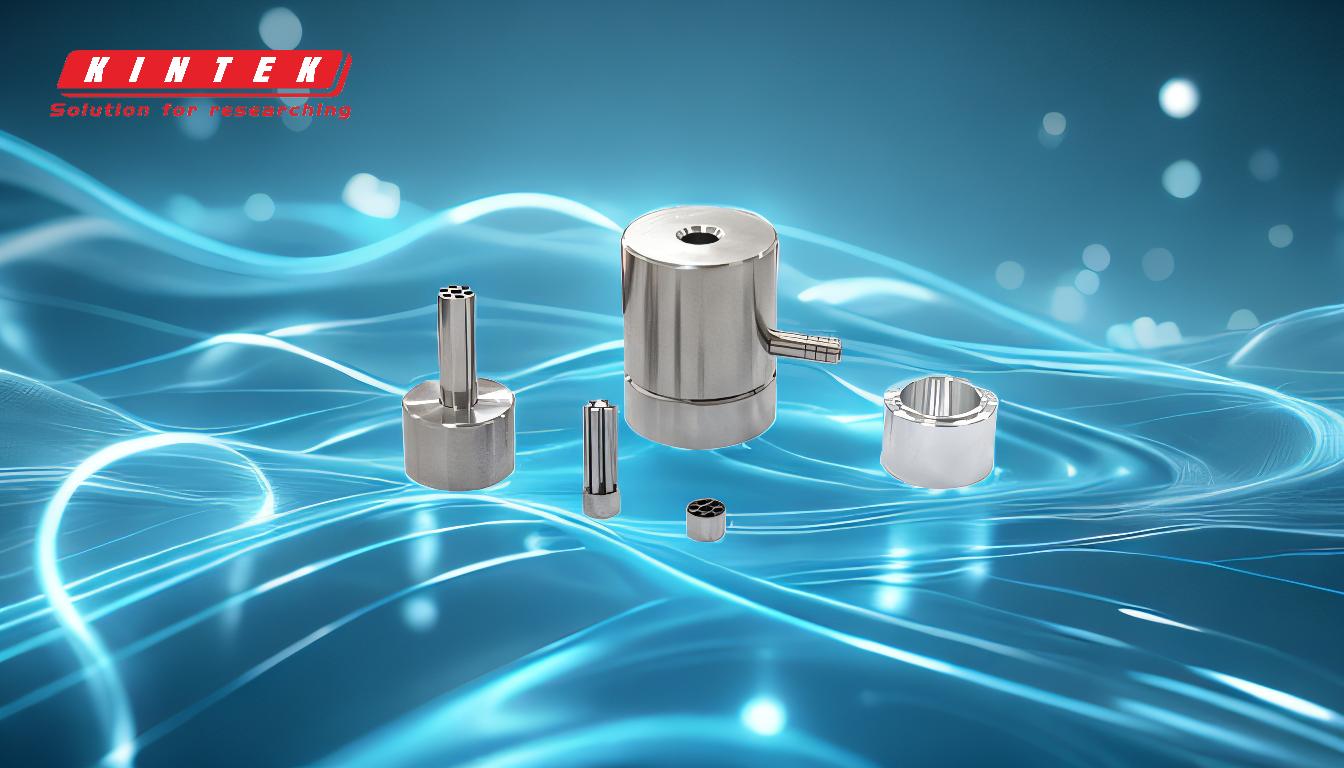
-
Aplicar e solidificar a pasta cerâmica no padrão do molde:
- O processo começa com a preparação de uma pasta cerâmica, que é uma mistura de partículas finas de cerâmica e um aglutinante líquido.Esta pasta é aplicada a um molde, normalmente feito de cera, plástico ou metal, que tem a forma do produto final.
- A pasta é cuidadosamente revestida no molde para garantir uma cobertura uniforme e captar todos os pormenores do molde.Uma vez aplicada, a pasta é deixada a secar e solidificar, formando um invólucro de cerâmica à volta do padrão.
-
Remover a pasta seca para criar um molde para o objeto desejado:
- Depois de a pasta cerâmica ter secado e solidificado, o passo seguinte é remover o padrão do molde.Normalmente, isto é feito através da fusão, queima ou dissolução do material do molde, deixando para trás um molde de cerâmica oco que replica a forma do molde original.
- Este passo é crucial, pois garante que o molde representa exatamente a forma e os detalhes do produto final.O processo de remoção deve ser feito com cuidado para evitar danificar o delicado molde de cerâmica.
-
Elimine os voláteis colocando o molde num forno de baixa temperatura ou utilizando um maçarico:
- Uma vez removido o padrão do molde, o molde cerâmico pode ainda conter substâncias voláteis, tais como humidade residual ou aglutinantes orgânicos, que têm de ser eliminados antes de o molde poder ser utilizado para fundição.
- O molde é colocado num forno a baixa temperatura ou exposto a um maçarico para eliminar lentamente estes voláteis.Este passo, conhecido como desparafinagem ou queima, assegura que o molde está livre de quaisquer substâncias que possam causar defeitos na peça fundida final.
-
Endurecer o molde num forno de alta temperatura:
- Depois de os voláteis terem sido removidos, o molde cerâmico é endurecido por aquecimento num forno de alta temperatura.Este passo, conhecido como sinterização, fortalece o material cerâmico e prepara-o para suportar as altas temperaturas do metal fundido durante a fundição.
- O processo de sinterização também ajuda a eliminar qualquer porosidade remanescente no molde cerâmico, garantindo uma superfície lisa e sem defeitos na peça fundida final.
-
Verter o metal fundido no molde cerâmico:
- Quando o molde de cerâmica estiver totalmente preparado, está pronto para o processo de fundição.O metal fundido é vertido no molde, preenchendo a cavidade e assumindo a forma do padrão original.
- O molde é concebido para suportar as altas temperaturas do metal fundido, assegurando que a peça final mantém todos os pormenores e dimensões intrincados do padrão original.
-
Arrefecimento e remoção da peça fundida:
- Depois de o metal fundido ter sido vertido no molde, deixa-se arrefecer e solidificar.Assim que o metal arrefece, o molde de cerâmica é cuidadosamente quebrado para revelar a peça fundida final.
- O molde cerâmico é normalmente destruído durante este processo, uma vez que foi concebido para ser um molde de utilização única.No entanto, o elevado nível de pormenor e precisão alcançado com a fundição em molde cerâmico torna-o um processo valioso para a produção de peças metálicas complexas e de alta qualidade.
-
Acabamento pós-fundição:
- Depois de a peça fundida ser retirada do molde, pode ser submetida a processos de acabamento adicionais, tais como retificação, polimento ou tratamento térmico, para obter o acabamento superficial e as propriedades mecânicas pretendidas.
- Estes passos de acabamento garantem que a peça final cumpre as especificações exigidas e está pronta a ser utilizada na aplicação pretendida.
Em resumo, a fundição em molde cerâmico é um processo de fundição altamente preciso e detalhado que envolve a criação de um molde cerâmico a partir de um padrão, a cura e o endurecimento do molde e, em seguida, a fundição de metal fundido no molde para produzir uma peça final.O processo é ideal para criar peças complexas e intrincadas com elevada precisão dimensional e superfícies lisas.
Tabela de resumo:
Passo | Descrição |
---|---|
1.Aplicar pasta cerâmica | Revestir um padrão de molde com pasta cerâmica para capturar detalhes finos. |
2.Remover o padrão do molde | Derreter ou dissolver o molde para deixar um molde oco de cerâmica. |
3.Eliminar os voláteis | Utilizar um aquecimento a baixa temperatura ou um maçarico para remover substâncias residuais. |
4.Endurecer o molde | Sinterizar o molde num forno de alta temperatura para obter resistência e suavidade. |
5.Verter metal fundido | Encher o molde de cerâmica com metal fundido para formar a peça final. |
6.Arrefecer e retirar a peça | Retire o molde de cerâmica para revelar a peça fundida acabada. |
7.Acabamento pós-fundição | Retificar, polir ou tratar termicamente a peça para obter as propriedades desejadas. |
Descubra como a fundição em molde cerâmico pode elevar a sua produção- contacte os nossos especialistas hoje !