O revestimento PVD (Physical Vapor Deposition) é um processo sofisticado usado para aplicar revestimentos finos, duráveis e de alto desempenho em vários substratos. Os revestimentos são feitos vaporizando um material alvo em um ambiente de vácuo e depositando-o sobre um substrato, muitas vezes em combinação com gases reativos para formar compostos específicos. Os materiais comuns usados em revestimentos PVD incluem nitreto de titânio (TiN), nitreto de zircônio (ZrN), nitreto de cromo (CrN) e carbono semelhante ao diamante (DLC). Esses materiais fornecem propriedades aprimoradas, como dureza, resistência ao desgaste, resistência à corrosão e apelo estético. O processo envolve várias etapas, incluindo limpeza do substrato, vaporização, reação e deposição, garantindo um revestimento consistente e de alta qualidade.
Pontos-chave explicados:
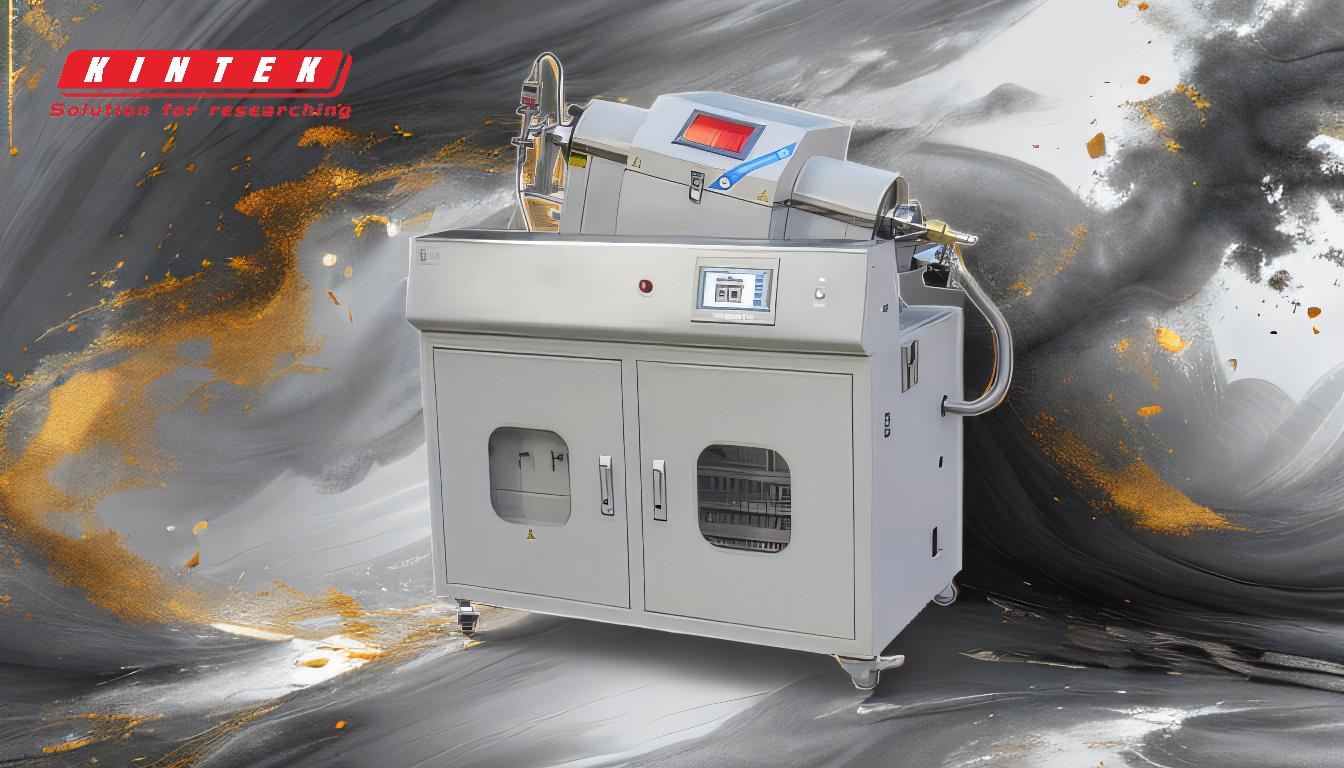
-
Materiais Utilizados em Revestimentos PVD:
- Nitreto de Titânio (TiN): Conhecido por sua aparência dourada, o TiN é amplamente utilizado por sua dureza e resistência ao desgaste. É comumente aplicado em ferramentas de corte, instrumentos médicos e acabamentos decorativos.
- Nitreto de Zircônio (ZrN): Oferece excelente resistência à corrosão e uma cor dourada brilhante. É frequentemente usado em aplicações que exigem durabilidade e estética.
- Nitreto de cromo (CrN): Oferece resistência superior à corrosão e é frequentemente usado em ambientes agressivos, como nas indústrias aeroespacial e automotiva.
- Carbono semelhante a diamante (DLC): Conhecido por sua excepcional dureza e baixo atrito, o DLC é utilizado em aplicações que exigem alta resistência ao desgaste, como componentes de motores e ferramentas de corte.
-
O Processo de Revestimento PVD:
- Limpeza de substrato: O substrato é cuidadosamente limpo para remover quaisquer contaminantes que possam afetar a aderência e a qualidade do revestimento.
- Vaporização: O material alvo é vaporizado em uma câmara de vácuo usando métodos como arcos elétricos, feixes de elétrons ou pulverização catódica.
- Reação: O material vaporizado reage com gases (por exemplo, nitrogênio ou oxigênio) para formar um composto com propriedades desejadas, como dureza ou cor.
- Deposição: O material vaporizado e reagido é depositado no substrato, formando um revestimento fino e uniforme.
- Controle de qualidade: Cada lote de componentes revestidos é testado quanto à consistência, espessura e cor usando técnicas como fluorescência de raios X (XRF) e espectrofotometria.
-
Fatores-chave no revestimento PVD:
- Transferência de linha de visão: PVD é um processo de linha de visão, o que significa que o revestimento é aplicado diretamente em superfícies visíveis à fonte de vapor. Isto requer um posicionamento cuidadoso do substrato.
- Pré-tratamento de superfície: A preparação adequada da superfície, incluindo limpeza e pré-tratamento, é crucial para garantir uma boa adesão e qualidade do revestimento.
- Ambiente de vácuo: O processo ocorre em ambiente de alto vácuo para evitar contaminação e garantir uma deposição pura.
- Evitar ar preso: Devem ser evitados furos roscados hermeticamente fechados para evitar que o ar preso afete a qualidade do revestimento.
-
Aplicações de revestimentos PVD:
- Ferramentas Industriais: Os revestimentos PVD são amplamente utilizados em ferramentas de corte, moldes e matrizes para aumentar sua durabilidade e desempenho.
- Instrumentos Médicos: A biocompatibilidade e a resistência à corrosão dos revestimentos PVD os tornam ideais para instrumentos cirúrgicos e implantes.
- Acabamentos Decorativos: Os revestimentos PVD são usados nas indústrias de joalheria e relojoaria por seu apelo estético e durabilidade.
- Automotivo e Aeroespacial: Os componentes dessas indústrias se beneficiam da resistência ao desgaste e à corrosão proporcionada pelos revestimentos PVD.
-
Vantagens dos revestimentos PVD:
- Durabilidade: Os revestimentos PVD são altamente duráveis e resistentes ao desgaste, corrosão e altas temperaturas.
- Versatilidade: O processo é compatível com uma ampla variedade de materiais, incluindo metais, plásticos e cerâmicas.
- Apelo Estético: Os revestimentos PVD podem ser adaptados para obter diversas cores e acabamentos, melhorando o apelo visual dos produtos revestidos.
- Amizade Ambiental: O processo PVD é ecologicamente correto, pois não envolve produtos químicos nocivos nem produz resíduos perigosos.
Em resumo, os revestimentos PVD são feitos de uma variedade de materiais, cada um oferecendo benefícios exclusivos, e são aplicados através de um processo preciso e controlado para melhorar o desempenho e a aparência de vários produtos.
Tabela Resumo:
Material | Propriedades | Aplicativos comuns |
---|---|---|
Nitreto de Titânio (TiN) | Dureza, resistência ao desgaste, aparência dourada | Ferramentas de corte, instrumentos médicos, acabamentos decorativos |
Nitreto de Zircônio (ZrN) | Resistência à corrosão, cor dourada brilhante | Aplicações que exigem durabilidade e estética |
Nitreto de cromo (CrN) | Resistência superior à corrosão | Aplicações aeroespaciais, automotivas e em ambientes agressivos |
Carbono semelhante a diamante (DLC) | Dureza excepcional, baixo atrito | Componentes de motores, ferramentas de corte, aplicações de alta resistência ao desgaste |
Interessado em aprimorar seus produtos com revestimentos PVD? Contate-nos hoje para saber mais!