A redução do tempo de produção na moldagem por compressão é crucial para melhorar a eficiência e reduzir os custos.Três métodos eficazes incluem evitar secções espessas no design, utilizar equipamento de compressão por parafuso e pré-aquecer o material.Evitar secções espessas garante uma cura mais rápida e uniforme, enquanto o equipamento de compressão por parafuso melhora o fluxo de material e reduz os tempos de ciclo.O pré-aquecimento do material minimiza o tempo necessário para que o material atinja a temperatura de moldagem ideal.Além disso, a abertura do molde de compressão para permitir a saída de gases durante o ciclo de moldagem é conhecida como \"desgaseificação\" ou \"respiração,\" o que evita defeitos e garante peças de maior qualidade.
Pontos-chave explicados:
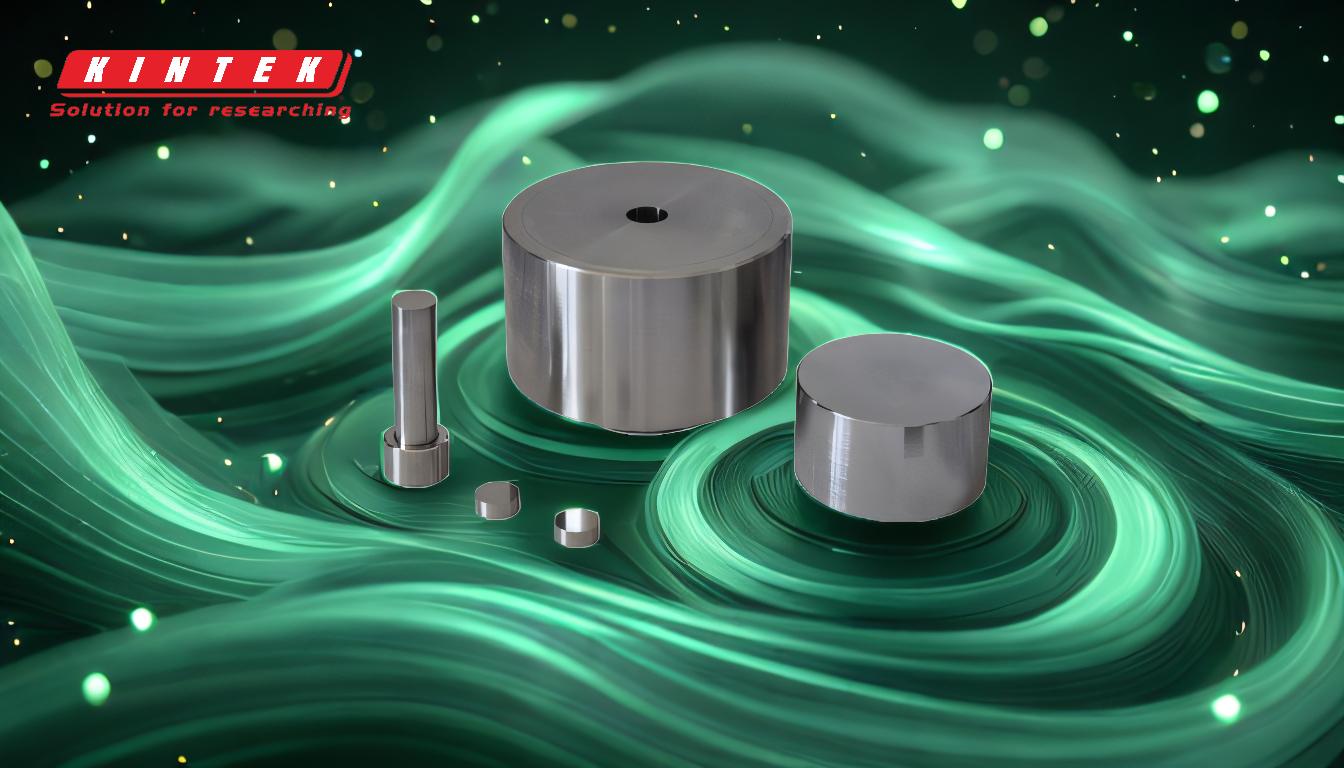
-
Evitar secções espessas no design
- As secções espessas de uma peça moldada demoram mais tempo a curar porque a transferência de calor é mais lenta, levando a uma cura desigual e a tempos de ciclo mais longos.
- Ao conceber peças com espessura de parede uniforme, a distribuição de calor torna-se mais consistente, reduzindo o tempo total de produção.
- As secções mais finas também reduzem a utilização de material, o que pode diminuir os custos e melhorar a qualidade das peças.
-
Utilizar equipamento de compressão por parafuso
- O equipamento de compressão por parafuso combina as vantagens da moldagem por injeção e por compressão, permitindo um melhor fluxo de material e tempos de ciclo mais rápidos.
- O mecanismo de parafuso pré-plastifica o material, assegurando que está uniformemente aquecido e pronto para ser moldado, o que reduz o tempo necessário para que o material atinja a temperatura ideal.
- Este método também melhora a consistência da peça e reduz o desperdício, aumentando ainda mais a eficiência da produção.
-
Pré-aquecer o material
- O pré-aquecimento do material antes de entrar no molde reduz o tempo necessário para o material atingir a temperatura de moldagem, acelerando o ciclo global.
- O pré-aquecimento pode ser efectuado utilizando aquecedores externos ou incorporando elementos de aquecimento no equipamento de moldagem.
- Este passo também melhora o fluxo de material e reduz o risco de defeitos, tais como vazios ou preenchimentos incompletos, o que pode poupar tempo ao minimizar o retrabalho.
-
Desgaseificação (respiração) durante o ciclo de moldagem
- A abertura ligeira do molde durante o ciclo de moldagem para permitir a saída de gases retidos é conhecida como desgaseificação ou respiração.
- Este passo evita defeitos como bolhas, vazios ou imperfeições superficiais causadas por ar ou gases presos.
- Embora a desgaseificação acrescente uma breve pausa ao ciclo, acaba por poupar tempo ao reduzir a necessidade de correcções pós-moldagem ou rejeições de peças.
Ao implementar estas estratégias, os fabricantes podem reduzir significativamente o tempo de produção na moldagem por compressão, mantendo ou mesmo melhorando a qualidade das peças.
Tabela de resumo:
Método | Benefícios |
---|---|
Evitar secções espessas no design | Cura mais rápida, distribuição uniforme do calor, utilização reduzida de material, custos mais baixos |
Utilizar equipamento de compressão por parafuso | Tempos de ciclo mais rápidos, melhor fluxo de material, qualidade consistente das peças |
Pré-aquecer o material | Tempo de aquecimento reduzido, melhor fluxo de material, menos defeitos |
Desgaseificação (respiração) | Evita defeitos, reduz o retrabalho, garante peças de maior qualidade |
Optimize o seu processo de moldagem por compressão hoje mesmo- contacte os nossos especialistas para soluções à medida!