O molde de duas placas, embora amplamente utilizado na moldagem por injeção, tem algumas desvantagens que podem afetar a eficiência da produção, o custo e a flexibilidade do design.As principais desvantagens incluem limitações na colocação de portas, que restringem as opções de design e podem levar a compromissos estéticos ou funcionais.Além disso, a necessidade de remover o sistema de corrediças após a moldagem aumenta o desperdício de mão de obra e de material, afectando a eficiência e a sustentabilidade globais.Abaixo, analisamos estas desvantagens em pormenor, fornecendo uma compreensão abrangente das suas implicações para os compradores de equipamento e consumíveis.
Pontos-chave explicados:
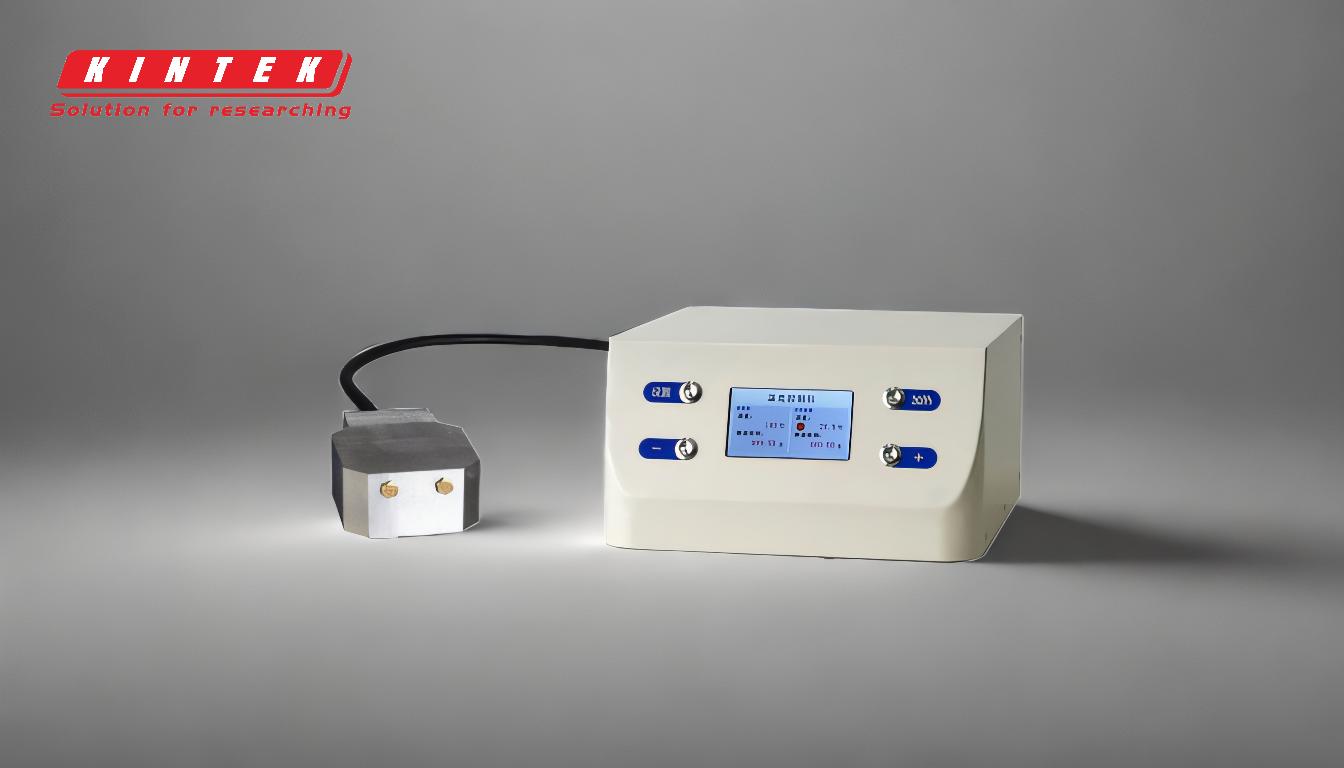
-
Opções limitadas de colocação de portas:
- Explicação:Num molde de duas placas, a porta (o ponto onde o plástico derretido entra na cavidade do molde) é tipicamente limitada ao lado da peça, a menos que sejam tomadas medidas especiais.Esta limitação pode afetar o design e a funcionalidade do produto final.
-
Implicações:
- Restrições de projeto:As portas laterais podem não ser adequadas para peças que exijam acabamentos estéticos ou com geometrias complexas.Este facto pode limitar a versatilidade do molde para diferentes designs de produtos.
- Complexidade acrescida:A implementação de medidas especiais para colocar os portões em locais alternativos pode aumentar a complexidade e o custo do molde, tornando-o menos económico para projectos mais simples.
-
Remoção do sistema de canais:
- Explicação:Após a moldagem por injeção, o sistema de canais (os canais através dos quais o plástico fundido flui para a cavidade do molde) deve ser removido da peça acabada.Este é um processo manual ou semi-automatizado que aumenta o ciclo de produção.
-
Implicações:
- Aumento dos custos laborais:A necessidade de remover as corrediças manualmente ou com maquinaria adicional aumenta os custos de mão de obra e o tempo de produção.
- Desperdício de material:O sistema de corrediças é normalmente descartado após a remoção, levando a desperdício de material.Isto pode ser uma preocupação significativa para operações focadas na sustentabilidade.
- Requisitos de pós-processamento:O processo de remoção pode exigir equipamento ou passos adicionais, como o corte ou a retificação, complicando ainda mais o fluxo de trabalho da produção.
-
Impacto na eficiência da produção:
- Explicação:O efeito combinado da colocação limitada de portas e da remoção de canais pode reduzir a eficiência global da produção.
-
Implicações:
- Tempos de ciclo mais longos:A necessidade de remover as corrediças e as potenciais restrições de conceção podem prolongar o ciclo de produção, reduzindo o rendimento.
- Custos operacionais mais elevados:O aumento da mão de obra, o desperdício de material e a potencial necessidade de equipamento adicional contribuem para custos operacionais mais elevados.
- Problemas de escalabilidade:Para a produção em larga escala, estas ineficiências podem tornar-se significativas, tornando os moldes de duas placas menos adequados para o fabrico de grandes volumes.
-
Considerações sobre o material:
- Explicação:O tipo de material utilizado na moldagem por injeção pode agravar as desvantagens dos moldes de duas placas.
-
Implicações:
- Compatibilidade de materiais:Alguns materiais podem não fluir bem através das portas laterais, levando a defeitos ou inconsistências no produto final.
- Propriedades térmicas:Os materiais com propriedades térmicas específicas podem exigir uma colocação mais precisa da porta, o que pode ser um desafio com moldes de duas placas.
-
Soluções alternativas:
- Explicação:Embora os moldes de duas placas tenham as suas desvantagens, a compreensão de soluções alternativas pode ajudar a mitigar estes problemas.
-
Implicações:
- Moldes de três placas:Estes moldes permitem uma colocação mais flexível das comportas e uma separação automática dos canais, reduzindo o desperdício de mão de obra e de material.
- Sistemas de canais quentes:Estes sistemas eliminam a necessidade de remoção do canal, mantendo o plástico fundido no sistema de canais, melhorando a eficiência e reduzindo o desperdício.
- Otimização do design:Trabalhar em estreita colaboração com os projectistas de moldes para otimizar a colocação da porta e o design do canal pode ajudar a atenuar algumas das desvantagens dos moldes de duas placas.
Em conclusão, embora os moldes de duas placas sejam uma escolha comum para a moldagem por injeção, as suas limitações na colocação da porta e a necessidade de remoção do canal podem afetar a eficiência da produção, o custo e a flexibilidade do design.Compreender estas desvantagens é crucial para que os compradores de equipamento e consumíveis tomem decisões informadas e explorem soluções alternativas que satisfaçam melhor as suas necessidades de produção.
Tabela de resumo:
Desvantagem | Explicação | Implicações |
---|---|---|
Opções limitadas de colocação de portões | Os portões são normalmente limitados lateralmente, o que afecta a conceção e a funcionalidade. | - Restrições de design para estética/geometrias complexas.- Aumento dos custos do molde. |
Remoção do sistema de canais | Remoção manual ou semi-automatizada das corrediças após a moldagem. | - Custos de mão de obra mais elevados.- Desperdício de material.- Etapas adicionais de pós-processamento. |
Impacto na eficiência da produção | Efeitos combinados das limitações do portão e da remoção do corredor. | - Tempos de ciclo mais longos.- Custos operacionais mais elevados.- Desafios de escalabilidade. |
Considerações sobre o material | O tipo de material pode piorar os problemas do molde de duas placas. | - Problemas de compatibilidade com portas laterais.- Problemas de propriedade térmica. |
Soluções alternativas | Opções para mitigar os inconvenientes do molde de duas placas. | - Moldes de três placas.- Sistemas de canais quentes.- Otimização do design. |
Descubra como as soluções alternativas podem melhorar o seu processo de moldagem por injeção. contacte-nos hoje para obter aconselhamento especializado!