Os revestimentos PVD (Deposição Física de Vapor) são, de facto, altamente resistentes à corrosão, o que os torna adequados para aplicações exigentes em que a durabilidade é fundamental.Estes revestimentos criam uma camada fina, dura e duradoura que se liga fortemente ao substrato, aumentando a sua resistência à corrosão, à oxidação e ao desgaste.O processo envolve a vaporização de um material alvo no vácuo e a sua deposição no substrato, garantindo um revestimento puro e duradouro.Os revestimentos PVD, como o nitreto de zircónio (ZrN), demonstraram um desempenho excecional em testes de resistência à corrosão, incluindo testes de névoa salina neutra e testes CASS.A sua dureza, finura e forte aderência tornam-nos ideais para ambientes agressivos, incluindo zonas costeiras.
Pontos-chave explicados:
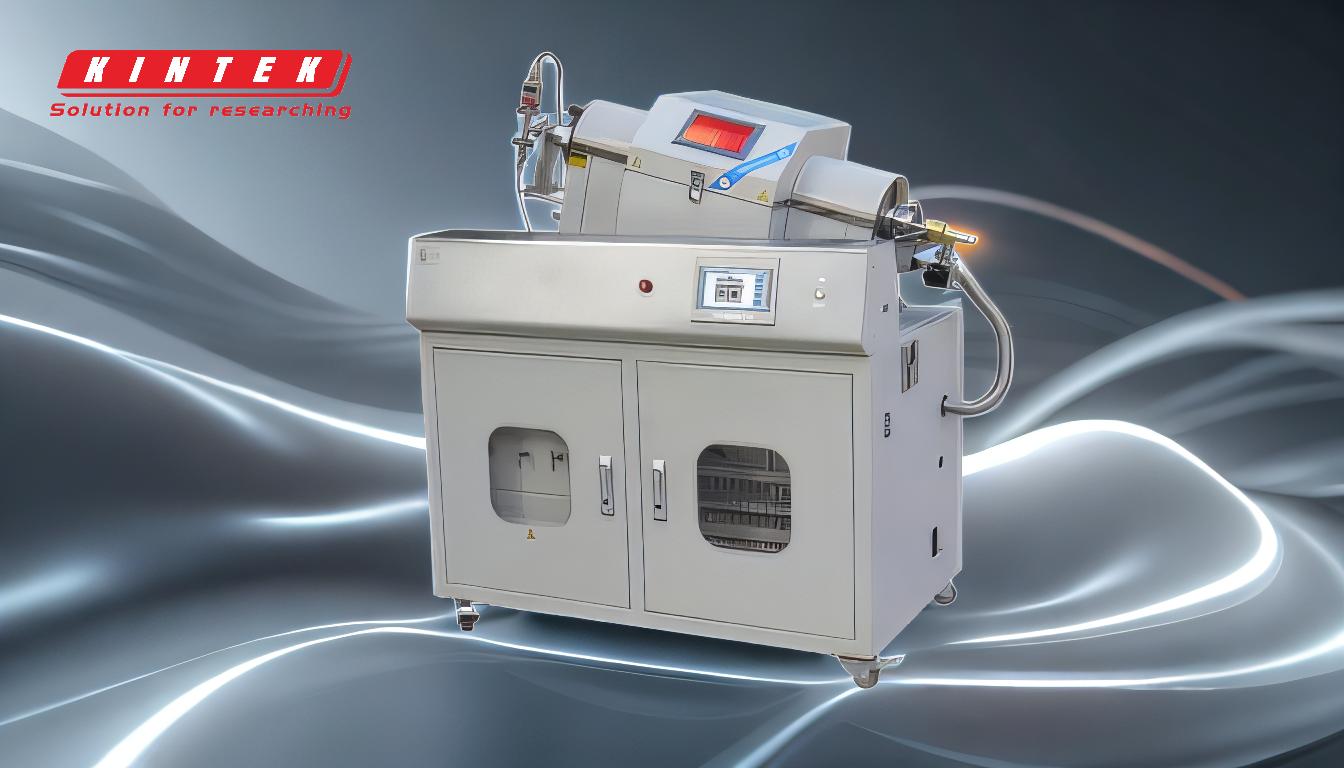
-
Resistência à corrosão dos revestimentos PVD:
- Os revestimentos PVD são altamente resistentes à corrosão e à oxidação.Formam uma camada protetora que protege o substrato de factores ambientais que causam ferrugem, manchas ou degradação.
- A finura dos revestimentos PVD (0,5 a 5 microns) não compromete a sua eficácia.Pelo contrário, a sua extrema finura torna-os difíceis de remover, garantindo uma proteção a longo prazo.
-
Durabilidade e dureza:
- Os revestimentos PVD são quatro vezes mais duros do que o crómio, o que os torna altamente resistentes a riscos e duradouros.Esta dureza contribui para a sua capacidade de resistir a condições adversas, incluindo ambientes corrosivos.
- A dureza do revestimento é um fator crítico para a sua durabilidade.Por exemplo, um revestimento de TiN (nitreto de titânio) pode aumentar o limite de fadiga e a resistência de um material de substrato como a liga Ti-6Al-4V.
-
Aderência e longevidade:
- Os revestimentos PVD aderem fortemente ao substrato, penetrando-o mesmo ligeiramente.Esta forte adesão garante que o revestimento permanece intacto durante períodos prolongados, aumentando a vida útil do produto até dez vezes em alguns casos.
- O processo de recozimento utilizado no revestimento PVD assegura que a camada está isenta de impurezas, melhorando ainda mais a sua durabilidade e resistência ao desgaste e à corrosão.
-
Desempenho em testes de corrosão:
- Os revestimentos PVD, como o Nitreto de Zircónio (ZrN), demonstraram um desempenho excecional em testes de corrosão normalizados.Por exemplo, ultrapassaram as 1200 horas em testes de névoa salina neutra (ASTM B117) e mais de 150 horas em testes CASS, que são medidas rigorosas de resistência à corrosão.
- Estes resultados realçam a adequação dos revestimentos PVD para aplicações expostas a ambientes corrosivos, tais como ambientes marinhos ou costeiros.
-
Aplicações em ambientes agressivos:
- Os revestimentos PVD são ideais para projectos expostos a ambientes agressivos, incluindo os que se encontram perto da costa, onde a água salgada e a humidade podem acelerar a corrosão.
- A sua capacidade de replicar o acabamento original dos materiais com um esforço mínimo torna-os versáteis para aplicações funcionais e estéticas.
-
Processo e pureza:
- O processo PVD envolve a vaporização de um material alvo no vácuo e a sua deposição no substrato.Isto assegura um revestimento puro, sem impurezas, o que aumenta a sua durabilidade e resistência à corrosão.
- O processo permite um controlo preciso das propriedades do revestimento, incluindo a espessura, a dureza e a aderência, garantindo um desempenho ótimo para aplicações específicas.
Em resumo, os revestimentos PVD são altamente resistentes à corrosão devido à sua dureza, forte aderência e pureza.O seu desempenho em testes de corrosão rigorosos e a sua adequação a ambientes agressivos fazem deles uma excelente escolha para aplicações que requerem uma durabilidade duradoura e proteção contra a corrosão.
Tabela de resumo:
Caraterística | Detalhes |
---|---|
Resistência à corrosão | Altamente resistente à ferrugem, manchas e oxidação; ideal para ambientes agressivos. |
Dureza | 4x mais duro do que o crómio; resistente a riscos e durável. |
Adesão | Adere fortemente aos substratos, aumentando a longevidade até 10 vezes. |
Desempenho em testes | Excede 1200 horas em testes de névoa salina neutra e 150 horas em testes CASS. |
Aplicações | Adequado para ambientes marinhos, costeiros e outros ambientes corrosivos. |
Processo | Revestimentos puros e sem impurezas através de vaporização a vácuo, garantindo durabilidade. |
Aumente a durabilidade do seu projeto com revestimentos PVD- contacte os nossos especialistas hoje mesmo !