As extrusoras de parafuso único, embora amplamente utilizadas em várias indústrias, têm várias desvantagens notáveis que podem afetar a sua eficiência, versatilidade e desempenho geral.Estas limitações incluem uma menor eficiência de produção, especialmente com materiais de elevada viscosidade ou multicomponentes, o que pode levar a tempos de produção mais longos e a custos operacionais mais elevados.Além disso, as extrusoras de parafuso único podem ter dificuldades com as tarefas de mistura e composição, limitando a sua capacidade de lidar com formulações de materiais complexos.A sua conceção também as torna menos adaptáveis a determinadas aplicações, como as que exigem um controlo preciso da temperatura ou taxas de produção elevadas.Compreender estas desvantagens é crucial para que os compradores de equipamento tomem decisões informadas com base nas suas necessidades de produção específicas.
Pontos-chave explicados:
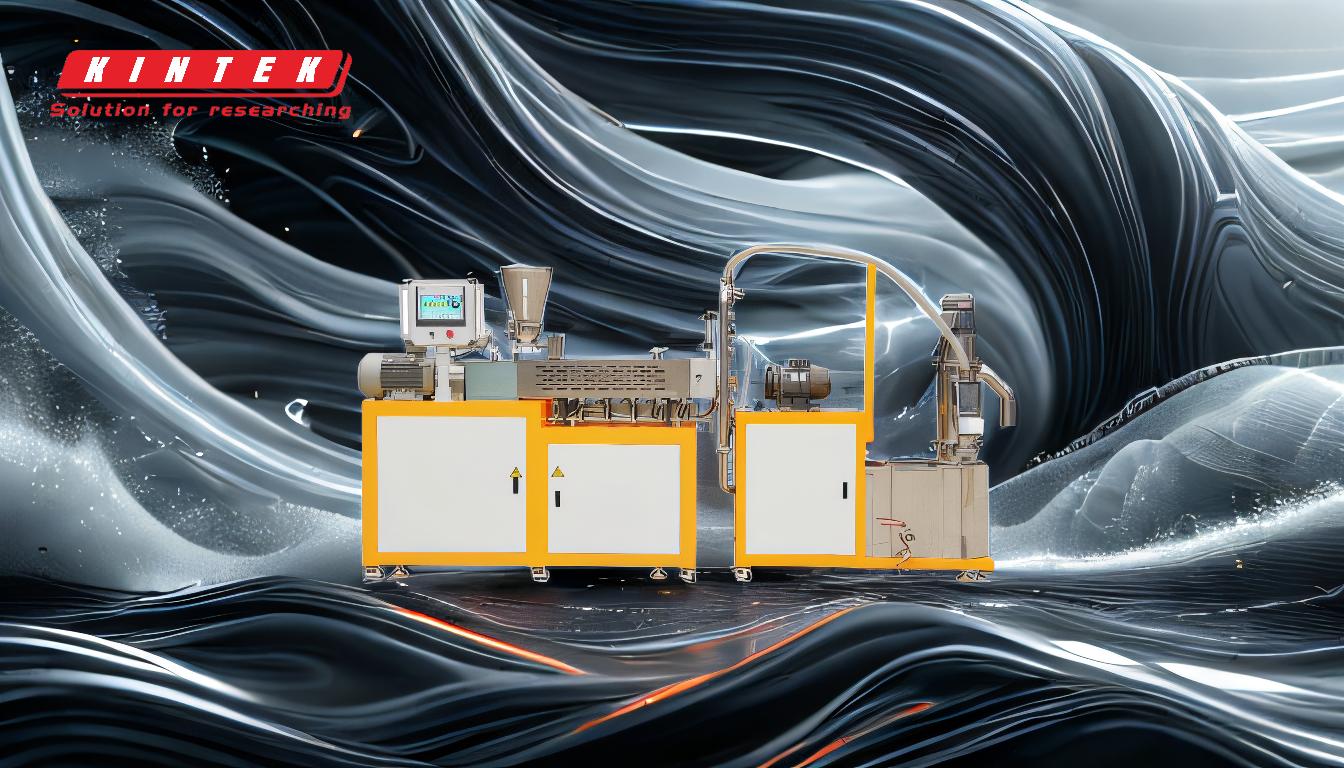
-
Menor eficiência de produção:
- As extrusoras de parafuso simples são geralmente menos eficientes em comparação com as extrusoras de parafuso duplo, particularmente quando processam materiais de alta viscosidade ou misturas de múltiplos componentes.
- A menor eficiência resulta das capacidades limitadas de cisalhamento e mistura da conceção de um único parafuso, o que pode resultar num processamento desigual do material e em tempos de ciclo mais longos.
- Esta ineficiência pode levar a um aumento dos custos operacionais, uma vez que é necessária mais energia e tempo para atingir o resultado pretendido.
-
Desafios com materiais de alta viscosidade:
- Os materiais de elevada viscosidade requerem forças de cisalhamento e de mistura significativas para garantir um processamento uniforme, que as extrusoras de parafuso único têm frequentemente dificuldade em fornecer.
- A falta de uma mistura eficaz pode levar a uma homogeneização incompleta, resultando numa má qualidade do produto e num potencial desperdício de material.
- Esta limitação torna as extrusoras de parafuso único menos adequadas para aplicações que envolvam polímeros altamente viscosos ou formulações complexas.
-
Capacidades limitadas de mistura e composição:
- As extrusoras de parafuso único não são ideais para tarefas que requerem uma mistura ou composição completa de vários materiais, como a adição de cargas, corantes ou aditivos.
- A ausência de parafusos entrelaçados nos modelos de parafuso único reduz a sua capacidade de atingir as elevadas taxas de cisalhamento necessárias para uma composição eficaz.
- Como resultado, os fabricantes podem ter de investir em equipamento adicional ou optar por extrusoras de duplo parafuso para satisfazer os requisitos de mistura e composição.
-
Adaptabilidade reduzida para aplicações complexas:
- As extrusoras de parafuso único são menos versáteis quando se trata de lidar com aplicações especializadas, tais como as que requerem um controlo preciso da temperatura, taxas de produção elevadas ou processamento avançado de materiais.
- O seu design mais simples limita a sua capacidade de se adaptar a exigências de produção variáveis, tornando-as menos adequadas para indústrias que requerem flexibilidade e precisão.
- Por exemplo, indústrias como a farmacêutica ou de materiais avançados podem considerar as extrusoras de parafuso único inadequadas para as suas necessidades.
-
Desafios operacionais e de manutenção:
- As ineficiências e limitações das extrusoras de parafuso único podem levar a um maior desgaste, exigindo uma manutenção mais frequente e um maior tempo de inatividade.
- Os desafios operacionais, como a dificuldade em obter uma qualidade de produto consistente, podem também resultar em custos mais elevados e numa produtividade reduzida ao longo do tempo.
- Estes factores tornam as extrusoras de parafuso simples menos rentáveis a longo prazo para determinadas aplicações.
-
Comparação com extrusoras de parafuso duplo:
- As extrusoras de parafuso duplo oferecem várias vantagens em relação às extrusoras de parafuso simples, incluindo melhor mistura, maior rendimento e maior adaptabilidade a materiais complexos.
- Embora as extrusoras de duplo parafuso possam ter um custo inicial mais elevado, o seu desempenho e eficiência superiores justificam frequentemente o investimento em aplicações que requerem capacidades de processamento avançadas.
- Os compradores devem avaliar cuidadosamente as suas necessidades de produção para determinar se as vantagens das extrusoras de duplo parafuso compensam o custo inicial mais baixo dos modelos de parafuso único.
Ao compreender estas desvantagens, os compradores de equipamento podem tomar decisões mais informadas e selecionar o tipo de extrusora que melhor se adapta aos seus requisitos de produção e objectivos a longo prazo.
Tabela de resumo:
Desvantagem | Impacto |
---|---|
Menor eficiência de produção | Tempos de ciclo mais longos, custos operacionais mais elevados e processamento de material desigual. |
Desafios com materiais de alta viscosidade | Fraca homogeneização, desperdício de material e inadequação para polímeros viscosos. |
Mistura e composição limitadas | Ineficaz para adicionar cargas, corantes ou atingir taxas de cisalhamento elevadas. |
Adaptabilidade reduzida | Menos adequado para um controlo preciso da temperatura, elevado rendimento ou materiais avançados. |
Desafios operacionais e de manutenção | Maior desgaste, manutenção frequente e maior tempo de inatividade. |
Comparação com extrusoras de parafuso duplo | Os parafusos duplos oferecem melhor mistura, maior rendimento e maior adaptabilidade. |
Precisa de ajuda para escolher a extrusora certa para as suas necessidades de produção? Contacte os nossos especialistas hoje para um aconselhamento personalizado!