Reactores de alta pressão
Aplicações
Os reactores de alta pressão são ferramentas indispensáveis no domínio da investigação química, particularmente quando se lida com condições extremas. Estes reactores especializados são meticulosamente concebidos para suportar e facilitar reacções químicas a alta temperatura e alta pressão, tornando-os ideais para o manuseamento de materiais que representam riscos significativos.
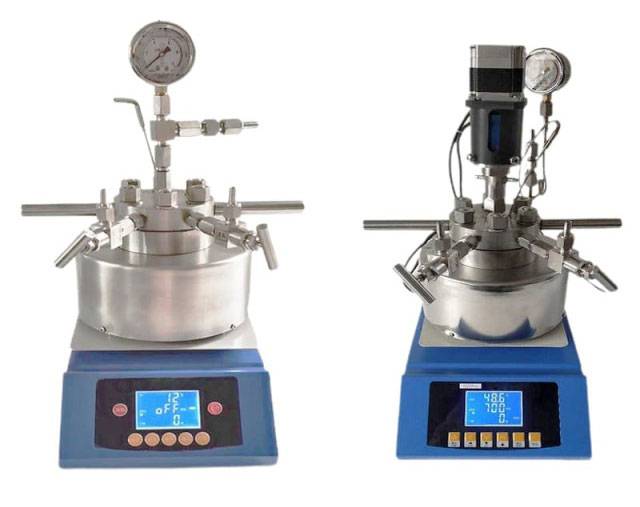
Especificamente, os reactores de alta pressão são cruciais para experiências que envolvem meios inflamáveis, explosivos e tóxicos. A sua construção robusta garante segurança e eficiência, permitindo aos investigadores manipular estas substâncias perigosas sem comprometer a integridade experimental. Esta capacidade é particularmente valiosa em indústrias como a petroquímica, a farmacêutica e as especialidades químicas, onde a necessidade de um controlo preciso das condições de reação é fundamental.
Além disso, a versatilidade dos reactores de alta pressão vai para além da segurança. Estão equipados para lidar com uma vasta gama de processos químicos, desde simples a complexos, permitindo um vasto espetro de aplicações. Quer se trate da síntese de novos compostos, da otimização de vias de reação ou do estudo da cinética da reação, os reactores de alta pressão proporcionam o ambiente necessário para alcançar os resultados desejados.
Em resumo, os reactores de alta pressão não são apenas ferramentas; são componentes essenciais para o avanço da investigação química e dos processos industriais, oferecendo segurança e funcionalidade nos ambientes mais exigentes.
Reactores de vidro
Funcionalidade
Os reactores de vidro são concebidos com uma construção de vidro de camada dupla, que é crucial para o manuseamento de uma variedade de materiais de reação. Este design único permite uma operação versátil, incluindo a agitação em condições de pressão normal e negativa. O vidro de dupla camada não só proporciona transparência para monitorizar as reacções, como também assegura um ambiente estável, facilitando o controlo constante da temperatura. Isto é conseguido através da integração de sistemas de aquecimento e arrefecimento, que podem manter uma regulação precisa da temperatura durante todo o processo de reação.
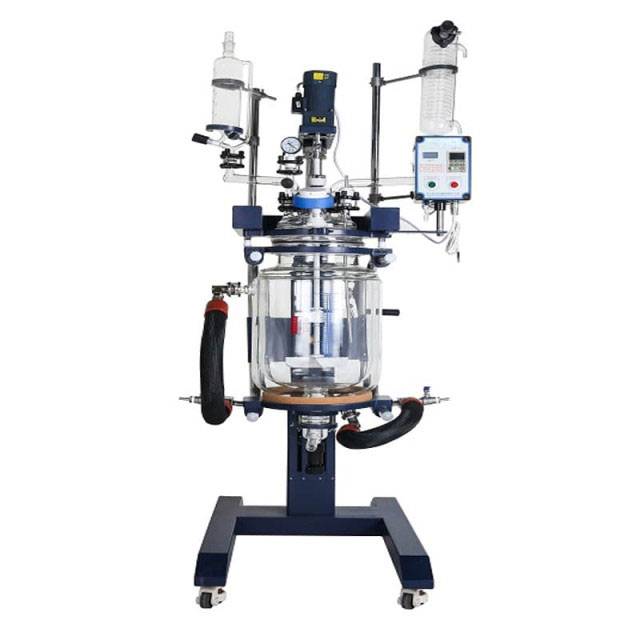
Para além do controlo da temperatura, a construção em vidro de dupla camada oferece caraterísticas de segurança melhoradas. A camada exterior de vidro funciona como uma barreira protetora, reduzindo o risco de exposição acidental a materiais perigosos. Este design é particularmente vantajoso quando se lida com compostos sensíveis ou voláteis, uma vez que minimiza o potencial de fugas e derrames.
A funcionalidade dos reactores de vidro vai para além da agitação básica e do controlo da temperatura. Estão também equipados com caraterísticas avançadas, como a regulação automática da pressão e sistemas de controlo programáveis. Estas caraterísticas permitem aos investigadores conduzir reacções complexas com elevada precisão e reprodutibilidade, tornando os reactores de vidro uma ferramenta indispensável nos laboratórios modernos.
Reactores Magnéticos
Mecanismo de vedação
Os reactores magnéticos utilizam uma sofisticada estrutura de vedação estática que integra um acoplador magnético. Este design é fundamental para atenuar os problemas de fugas, garantindo assim um ambiente de trabalho totalmente vedado. O acoplador magnético actua como um dispositivo de transmissão sem contacto, facilitando a transferência de binário e movimento sem contacto físico direto. Esta caraterística é particularmente vantajosa no manuseamento de materiais perigosos, onde mesmo fugas mínimas podem comprometer a integridade e a segurança experimental.
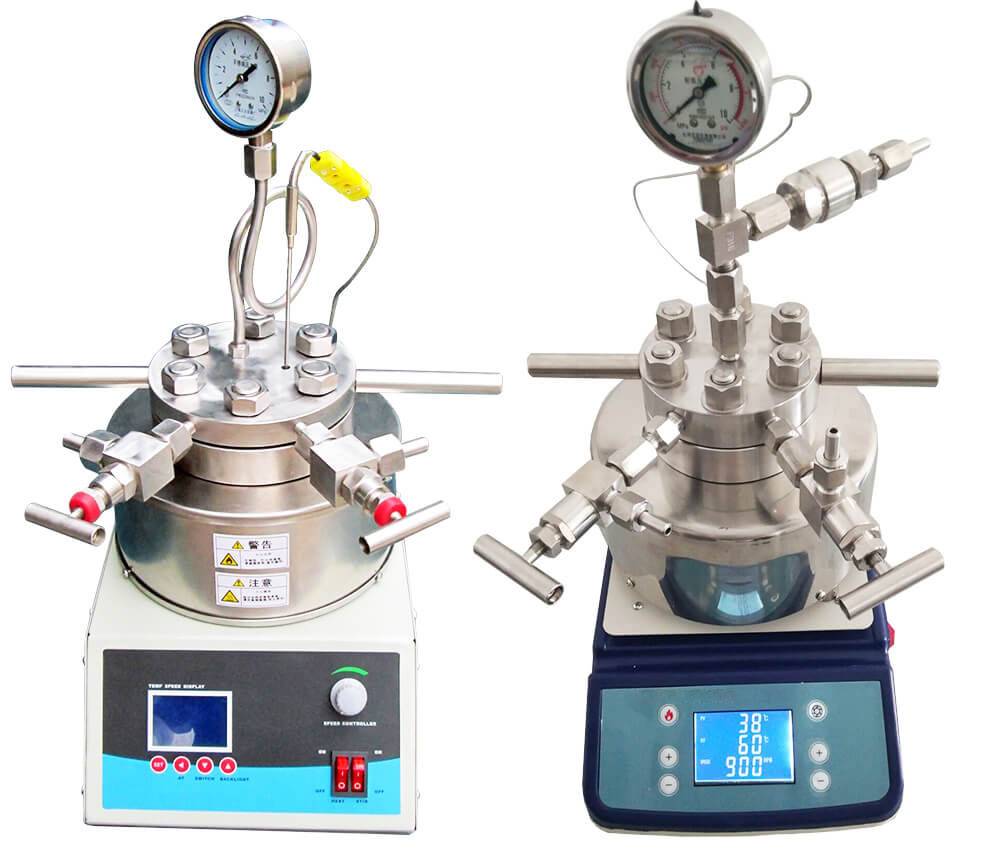
O mecanismo de vedação estática funciona com base no princípio dos campos magnéticos, que interagem com os componentes internos do reator para permitir um funcionamento suave sem a necessidade de vedantes mecânicos. Esta abordagem não só aumenta a durabilidade do reator como também simplifica os procedimentos de manutenção. Ao eliminar a necessidade de substituição frequente de vedantes, o custo operacional global é reduzido, tornando os reactores magnéticos uma escolha rentável para os laboratórios.
Além disso, a vedação completa garante que o ambiente de reação permanece imaculado, livre de contaminantes externos que possam alterar os resultados da reação. Este nível de controlo ambiental é crucial para experiências que requerem condições precisas, tais como as que envolvem meios tóxicos ou explosivos. A eficiência do acoplador magnético em manter um ambiente selado sublinha a adequação do reator para actividades de investigação e desenvolvimento de alto risco.
Sintetizadores de micro-ondas
Reacções catalíticas
Os sintetizadores de micro-ondas são fundamentais para catalisar uma vasta gama de reacções em vários domínios, incluindo química orgânica, produtos farmacêuticos e bioquímica. Estes sintetizadores aproveitam as propriedades únicas das micro-ondas para melhorar as taxas de reação e os rendimentos, tornando-os ferramentas indispensáveis nos laboratórios modernos.
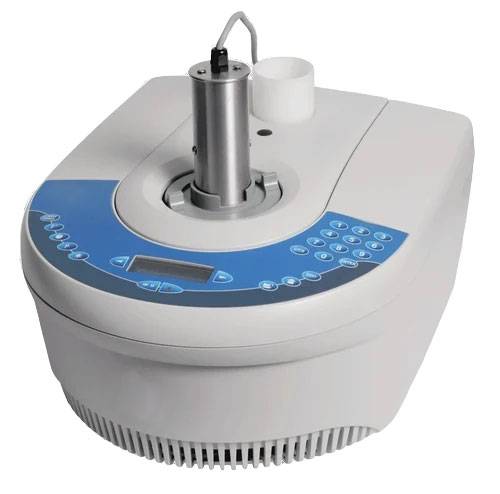
Uma das principais vantagens dos sintetizadores de micro-ondas é a sua capacidade de facilitar reacções orgânicas complexas. Estas reacções requerem frequentemente um controlo preciso da temperatura e da pressão, condições que as micro-ondas podem proporcionar de forma eficiente. Por exemplo, a síntese de produtos farmacêuticos envolve frequentemente transformações moleculares complexas que beneficiam do aquecimento rápido e uniforme proporcionado pelas micro-ondas.
No domínio da bioquímica, os sintetizadores de micro-ondas são utilizados para catalisar reacções que envolvem biomoléculas. Estas reacções podem ser particularmente difíceis devido à sensibilidade dos materiais biológicos ao calor e a outros factores ambientais. O aquecimento controlado e os tempos de reação rápidos proporcionados pelas micro-ondas ajudam a minimizar a degradação e a maximizar a pureza do produto.
Para além das reacções químicas, os sintetizadores de micro-ondas também desempenham um papel crucial nos processos físicos, como a extração de solventes. Esta técnica é amplamente utilizada na extração de compostos valiosos de misturas complexas, um processo que pode ser significativamente acelerado e optimizado utilizando energia de micro-ondas.
Em resumo, os sintetizadores de micro-ondas são ferramentas versáteis que estendem as suas capacidades catalíticas a um espetro de disciplinas científicas, melhorando tanto a eficiência como a eficácia da investigação e desenvolvimento laboratorial.
Calorímetros de reação
Medição
Os calorímetros de reação são ferramentas indispensáveis no laboratório, concebidas para medir o calor libertado ou absorvido durante reacções químicas ou processos físicos. Esta medição é crucial para obter conhecimentos no campo da termoquímica e cinética, que são essenciais para compreender as mudanças de energia e as taxas de reação envolvidas em vários processos.
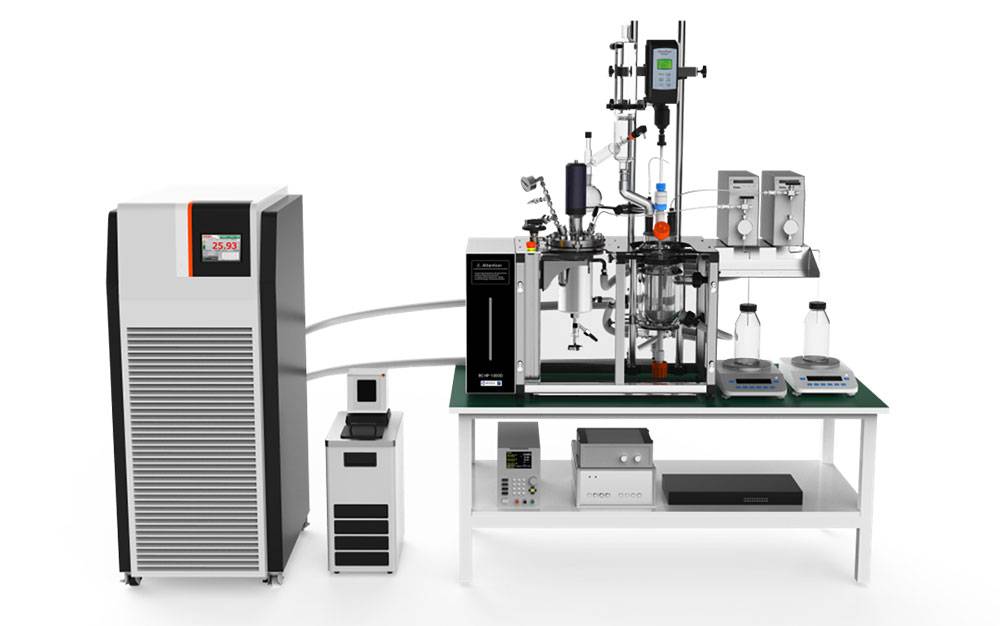
Os dados recolhidos pelos calorímetros de reação podem ser utilizados para analisar as propriedades termodinâmicas das reacções, como as alterações de entalpia e entropia, que são fundamentais para prever os resultados da reação e otimizar as condições de reação. Além disso, os parâmetros cinéticos derivados destas medições, como a energia de ativação e a ordem de reação, fornecem informações valiosas para o controlo do processo e aumento de escala.
Parâmetro de medição | Perceção Termoquímica | Perceção cinética |
---|---|---|
Libertação/Absorção de calor | Mudança de Entalpia | Taxa de reação |
Mudança de temperatura | Mudança de entropia | Energia de ativação |
Ao monitorizar o fluxo de calor, os investigadores podem também identificar potenciais perigos, tais como reacções exotérmicas que podem conduzir a reacções de fuga ou sobreaquecimento, garantindo assim práticas laboratoriais mais seguras. A integração de dados calorimétricos com outras técnicas analíticas melhora a compreensão global de sistemas de reação complexos, tornando os calorímetros de reação um componente essencial da investigação e desenvolvimento químicos modernos.
Dispositivos de Avaliação de Catalisadores
Princípios de Avaliação
Os dispositivos de avaliação de catalisadores simulam condições de reação do mundo real para avaliar a eficiência dos catalisadores. Esta avaliação baseia-se principalmente em métricas derivadas dos produtos de reação, que são meticulosamente analisados para medir a eficácia do catalisador. Estes métodos de avaliação são amplamente categorizados em dois tipos: estáticos e dinâmicos.
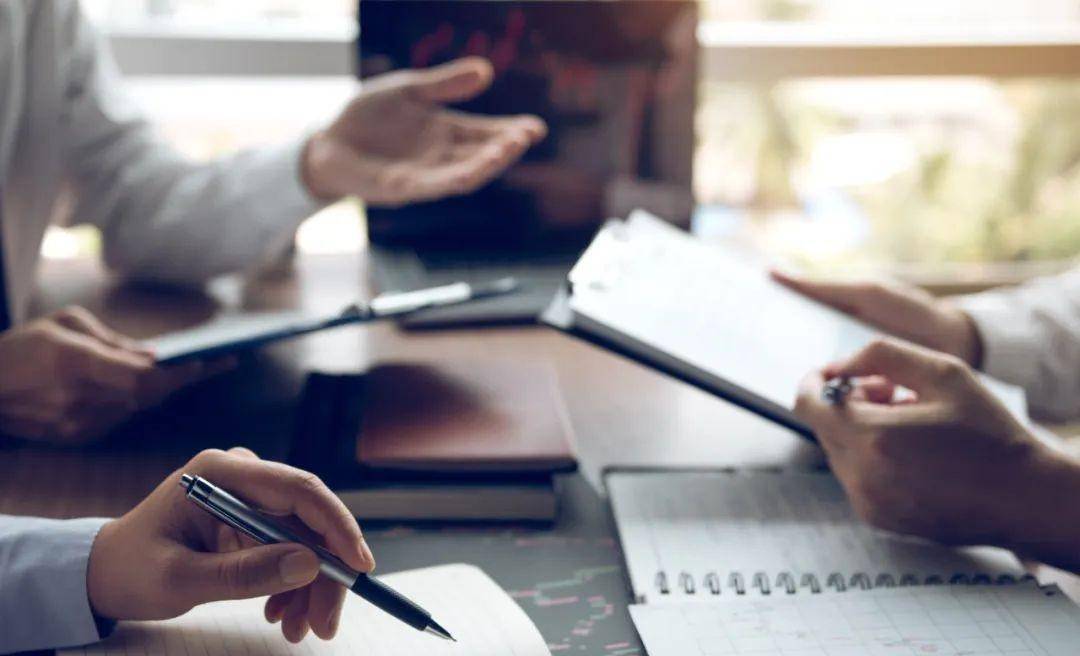
Avaliação estática envolve a criação de um ambiente controlado onde as condições de reação permanecem constantes durante toda a experiência. Este método é particularmente útil para estudar a atividade inicial e a seletividade dos catalisadores em condições estáveis. Os parâmetros-chave, como a temperatura, a pressão e as concentrações dos reagentes, são fixos, permitindo uma análise detalhada do desempenho do catalisador sem a interferência de variáveis flutuantes.
Avaliação dinâmica por outro lado, imita cenários industriais mais realistas onde as condições de reação estão sujeitas a alterações. Esta abordagem avalia a capacidade de um catalisador manter a sua eficiência em condições variáveis, tais como temperaturas flutuantes ou concentrações variáveis de reagentes. A avaliação dinâmica é crucial para prever o desempenho a longo prazo e a estabilidade dos catalisadores em processos contínuos, fornecendo informações que a avaliação estática por si só não pode oferecer.
Tipo de avaliação | Caraterísticas principais | Aplicação |
---|---|---|
Estática | Condições controladas e constantes | Estudos iniciais de atividade e seletividade |
Dinâmico | Condições variáveis | Desempenho a longo prazo e estabilidade em processos contínuos |
Os métodos de avaliação estáticos e dinâmicos são essenciais para uma avaliação abrangente da eficiência do catalisador, assegurando que o catalisador escolhido é optimizado para as condições de reação específicas que irá encontrar nas aplicações práticas.
Estações de trabalho de síntese
Automação
Os reactores de síntese totalmente automatizados, controlados por sistemas informáticos avançados, estão a revolucionar o campo da investigação de compostos e medicamentos. Estas máquinas sofisticadas lidam com uma miríade de processos com precisão e eficiência, incluindo alimentação, aquecimento, agitação e destilação. A automatização não só aumenta a reprodutibilidade e a exatidão das experiências, como também reduz o risco de erro humano, o que é particularmente crucial em ambientes de investigação delicados e de alto risco.
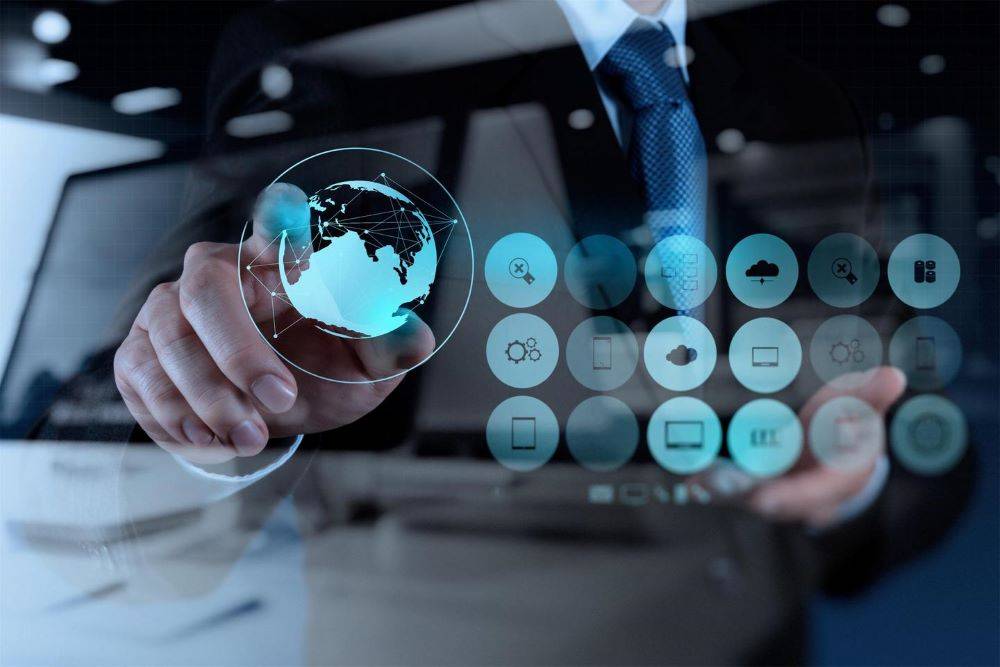
Uma das principais vantagens destes sistemas automatizados é a sua capacidade de gerir sequências complexas de operações sem intervenção manual. Esta capacidade é particularmente benéfica na síntese de compostos complexos em que o mais pequeno desvio pode levar a variações significativas no produto final. Os sistemas controlados por computador asseguram que cada passo é executado com os parâmetros exactos predefinidos pelos investigadores, mantendo assim a consistência em várias execuções.
Além disso, a automatização permite o funcionamento contínuo, o que pode acelerar significativamente o processo de investigação. Os investigadores podem programar experiências para serem executadas durante a noite ou aos fins-de-semana, maximizando a utilização do tempo de laboratório. Este funcionamento contínuo é facilitado pela conceção robusta dos reactores, que são construídos para suportar longos períodos de utilização sem comprometer o desempenho.
Para além das suas vantagens operacionais, os reactores de síntese automatizados também contribuem para a segurança no laboratório. Ao lidar com processos perigosos como aquecimento e destilação, estes sistemas minimizam a exposição dos investigadores a químicos e condições potencialmente perigosas. Isto não só protege a saúde e a segurança da equipa de investigação, como também assegura a conformidade com os rigorosos regulamentos de segurança laboratorial.
A integração do controlo por computador também permite a monitorização em tempo real e o registo de dados, fornecendo aos investigadores informações valiosas sobre a dinâmica da reação. Estes dados podem ser utilizados para otimizar as condições de reação, identificar ineficiências e aperfeiçoar o processo de síntese. A capacidade de analisar e ajustar em tempo real é um avanço significativo que pode levar a resultados de investigação mais eficientes e eficazes.
Em resumo, o advento de reactores de síntese totalmente automatizados representa uma mudança fundamental na forma como a investigação de compostos e medicamentos é conduzida. Ao tirar partido da precisão controlada por computador, estes sistemas aumentam a reprodutibilidade, aceleram os prazos de investigação, melhoram a segurança e fornecem dados valiosos para a otimização do processo. À medida que a tecnologia continua a evoluir, o seu impacto no campo da síntese química deverá crescer, abrindo caminho para novas descobertas e inovações.
CONTACTE-NOS PARA UMA CONSULTA GRATUITA
Os produtos e serviços da KINTEK LAB SOLUTION foram reconhecidos por clientes de todo o mundo. A nossa equipa terá todo o prazer em ajudar com qualquer questão que possa ter. Contacte-nos para uma consulta gratuita e fale com um especialista de produto para encontrar a solução mais adequada para as suas necessidades de aplicação!