A deposição por pulverização catódica é um processo crítico no fabrico de semicondutores, utilizado para depositar películas finas de materiais em substratos.Este processo envolve o bombardeamento de um material alvo com iões de alta energia, normalmente a partir de um plasma de árgon, o que faz com que os átomos do alvo sejam ejectados e depositados num substrato.Este método é particularmente valorizado pela sua capacidade de produzir revestimentos altamente puros e uniformes, essenciais para os requisitos de alto desempenho dos componentes semicondutores.A deposição por pulverização catódica é versátil, capaz de depositar uma ampla gama de materiais, incluindo metais e cerâmicas, e evoluiu significativamente desde a sua descoberta em meados do século XIX.
Pontos-chave explicados:
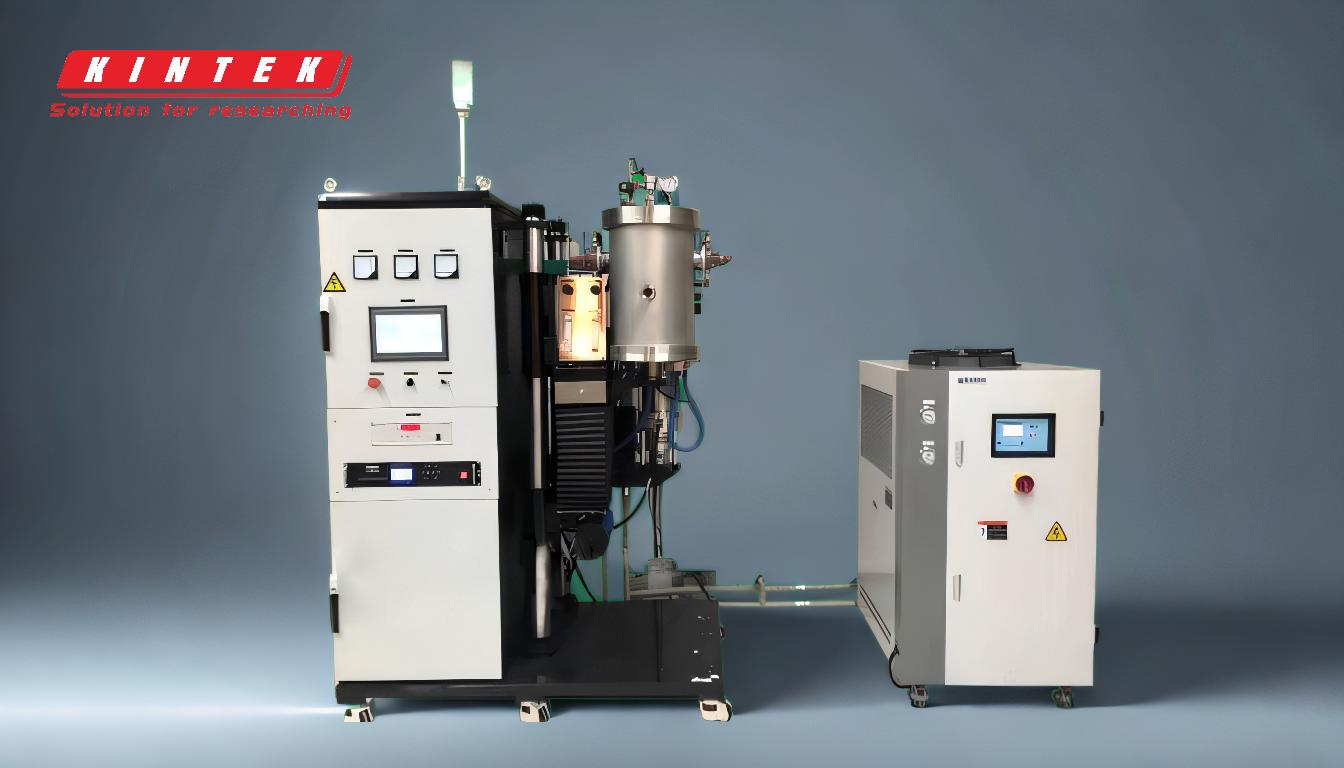
-
Mecanismo de deposição por pulverização catódica:
- A deposição por pulverização catódica consiste em expor um material alvo a um plasma de iões de alta energia, geralmente árgon.Estes iões colidem com o alvo, fazendo com que os átomos sejam ejectados da sua superfície.
- Os átomos ejectados formam uma nuvem de vapor que depois se condensa num substrato, formando uma película fina.Este processo é altamente controlado para garantir a uniformidade e a pureza do material depositado.
-
Aplicações no fabrico de semicondutores:
- Na produção de semicondutores, a deposição por pulverização catódica é utilizada para aplicar películas finas de materiais como o ouro, que são essenciais para a sua excelente condutividade eléctrica e térmica.
- O processo é crucial para criar as intrincadas camadas de metal e materiais dieléctricos necessários em circuitos integrados e outros dispositivos semicondutores.
-
Evolução histórica e avanços tecnológicos:
- A deposição por pulverização catódica foi observada pela primeira vez em meados do século XIX e encontrou aplicações comerciais na década de 1930.
- Após um período de declínio na década de 1950, a técnica recuperou a popularidade no final da década de 1950 e início da década de 1960 devido aos avanços na tecnologia de vácuo e ao desenvolvimento da pulverização por radiofrequência (rf), que permitiu a deposição de materiais dieléctricos.
-
Importância da pureza dos alvos de pulverização catódica:
- A pureza do alvo de pulverização catódica é fundamental, especialmente em aplicações de semicondutores.Mesmo vestígios de impurezas podem afetar significativamente o desempenho dos componentes semicondutores.
- Os alvos de elevada pureza garantem que as películas depositadas têm as propriedades eléctricas e térmicas necessárias para dispositivos semicondutores de elevado desempenho.
-
Utilização em Microscopia Eletrónica de Varrimento (SEM):
- O revestimento por pulverização catódica é também utilizado no SEM para melhorar a obtenção de imagens das amostras.Ao depositar uma fina camada condutora em amostras não condutoras ou sensíveis ao feixe, reduz os efeitos de carga e melhora a relação sinal/ruído, levando a imagens mais claras e detalhadas.
A deposição por pulverização catódica continua a ser uma técnica fundamental no fabrico de dispositivos semicondutores modernos, oferecendo uma precisão e versatilidade inigualáveis por outros métodos de deposição.A sua evolução e adaptação contínuas a novos materiais e tecnologias sublinham a sua importância para o avanço do fabrico de semicondutores.
Quadro de síntese:
Aspeto-chave | Detalhes |
---|---|
Mecanismo | Os iões de árgon de alta energia bombardeiam um alvo, ejectando átomos para formar uma película fina. |
Aplicações | Utilizado em dispositivos semicondutores para condutividade eléctrica e térmica. |
Desenvolvimento histórico | Descoberto no século XIX; avançado com a pulverização catódica por radiofrequência na década de 1960. |
Pureza do alvo | Alvos de elevada pureza asseguram propriedades eléctricas e térmicas óptimas. |
Aplicações SEM | Melhora a imagem ao depositar camadas condutoras em amostras não condutoras. |
Descubra como a deposição por pulverização catódica pode revolucionar os seus processos de semicondutores contacte os nossos especialistas hoje !