Os reactores descontínuos, embora versáteis e amplamente utilizados em laboratório e em ambientes de produção em pequena escala, apresentam várias desvantagens significativas.Estas incluem custos de mão de obra elevados, desafios no aumento da produção, longos períodos de inatividade durante as operações, instrumentação limitada, qualidade inconsistente do produto e riscos de segurança, tais como explosões.Além disso, os reactores descontínuos são geralmente mais adequados para reacções homogéneas, limitando a sua aplicabilidade em processos industriais mais complexos.Estas desvantagens tornam-nos menos eficientes e rentáveis em comparação com os reactores de fluxo contínuo, que oferecem rendimentos mais elevados, melhor controlo e custos de fabrico mais baixos.
Pontos-chave explicados:
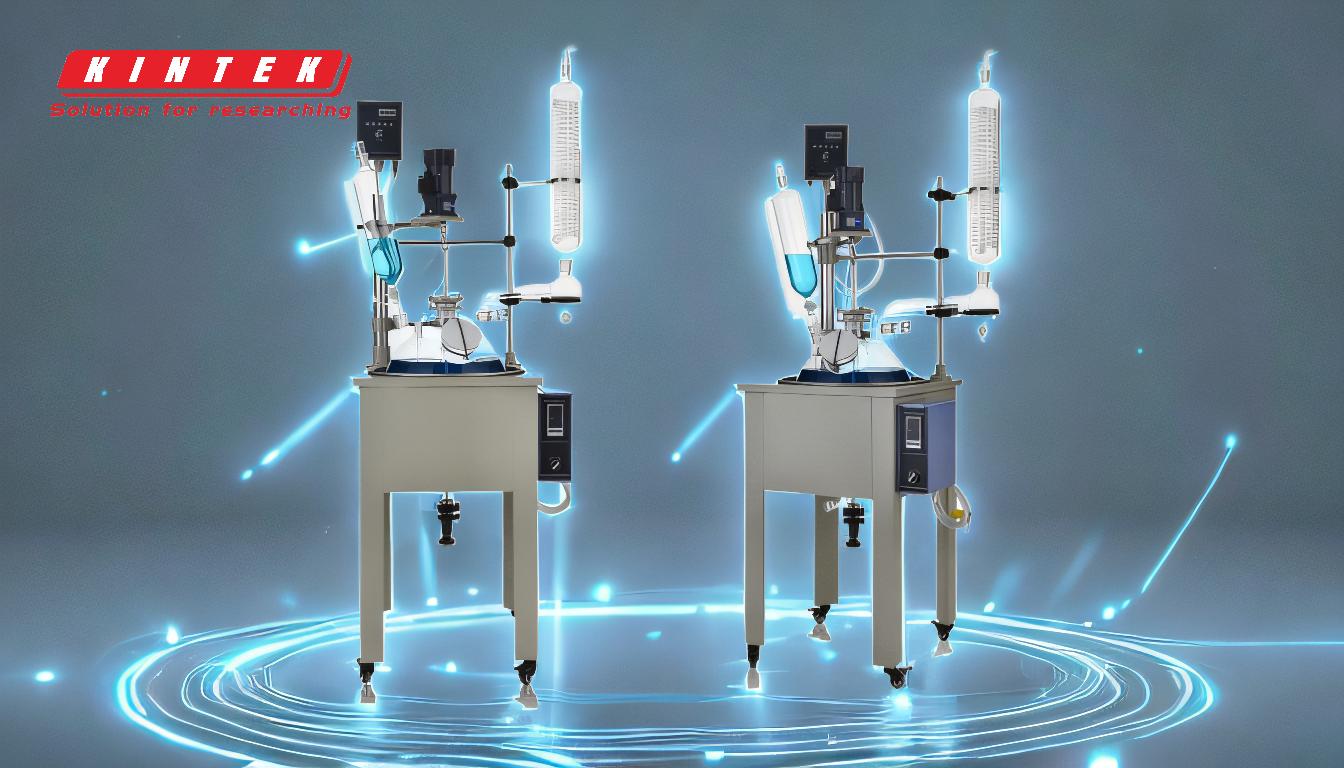
-
Custos elevados de mão de obra por unidade de produção
- Os reactores descontínuos requerem uma intervenção manual significativa para tarefas como o carregamento, a descarga e a limpeza.Isto aumenta os custos de mão de obra, especialmente quando comparados com os reactores de fluxo contínuo, que são mais automatizados e requerem menos supervisão humana.
- A natureza repetitiva dos processos em lote também leva a ineficiências, uma vez que os trabalhadores têm de executar as mesmas tarefas várias vezes para cada lote.
-
Dificuldade em manter a produção em grande escala
- Os reactores descontínuos não são adequados para a produção industrial em grande escala devido à sua capacidade limitada e à necessidade de ciclos frequentes de arranque e paragem.
- O aumento da produção com reactores descontínuos implica frequentemente a utilização de múltiplos reactores, o que aumenta os custos e a complexidade.Os reactores de fluxo contínuo, pelo contrário, são concebidos para produção de grandes volumes e podem funcionar continuamente sem interrupções.
-
Longos tempos de paragem durante a carga e descarga
- Uma parte significativa do ciclo de produção em reactores descontínuos é gasta em tarefas não produtivas, como o carregamento de reagentes, o aquecimento ou arrefecimento do sistema e a descarga de produtos.
- Estes tempos de inatividade reduzem a eficiência global e o rendimento, tornando os reactores descontínuos menos adequados para processos de produção sensíveis ao tempo ou de elevada procura.
-
Falta de Instrumentação e Controlo
- Os reactores descontínuos carecem frequentemente de sistemas avançados de instrumentação e controlo, o que dificulta a monitorização e a otimização das condições de reação em tempo real.
- Isto pode levar a inconsistências na qualidade do produto e a uma menor fiabilidade do processo, uma vez que os operadores têm menos controlo sobre variáveis como a temperatura, a pressão e a mistura.
-
Má qualidade e consistência do produto
- Devido à falta de controlo preciso e à variabilidade inerente entre lotes, os reactores descontínuos produzem frequentemente produtos com uma qualidade inconsistente.
- Isto é particularmente problemático em indústrias onde a uniformidade do produto é crítica, como a farmacêutica ou de especialidades químicas.
-
Riscos de explosão durante o esvaziamento
- Os reactores descontínuos podem apresentar riscos de segurança, especialmente durante a fase de esvaziamento, quando os reagentes ou subprodutos residuais podem reagir de forma imprevisível.
- O design dos reactores descontínuos não está optimizado para lidar com explosões poderosas, tornando-os menos seguros em comparação com os reactores de fluxo contínuo, que são concebidos para gerir condições de alta pressão e alta temperatura de forma mais eficaz.
-
Aplicabilidade limitada a reacções homogéneas
- Os reactores descontínuos são principalmente adequados para reacções homogéneas, em que os reagentes e os produtos se encontram numa única fase (por exemplo, líquido ou gás).
- São menos eficazes para reacções heterogéneas, que envolvem múltiplas fases (por exemplo, sólido-líquido ou gás-líquido), limitando ainda mais a sua versatilidade em aplicações industriais.
-
Custos de fabrico e operacionais mais elevados
- Embora os reactores descontínuos possam poupar nos custos iniciais de fabrico devido à sua conceção mais simples, as suas ineficiências operacionais e maiores requisitos de mão de obra resultam frequentemente em custos mais elevados a longo prazo.
- Os reactores de fluxo contínuo, apesar do seu investimento inicial mais elevado, oferecem custos de fabrico mais baixos e rácios mais elevados de valor por produto (VTO) ao longo do tempo.
-
Incapacidade de atingir condições de estado estacionário
- Os reactores descontínuos não atingem um estado estacionário, o que significa que as condições de reação (por exemplo, temperatura, pressão e concentração) mudam ao longo do tempo.
- Isto dificulta o controlo e a otimização da reação, conduzindo a potenciais ineficiências e a rendimentos de produto abaixo do ideal.
-
Design e tecnologia desactualizados
- Os reactores descontínuos sofreram alterações mínimas de conceção ao longo do tempo, baseando-se em métodos tradicionais que carecem dos avanços observados nos reactores de fluxo contínuo.
- Isto limita a sua capacidade de competir com as tecnologias de reactores modernos, que oferecem melhor desempenho, rendimentos mais elevados e caraterísticas de segurança melhoradas.
Em resumo, embora os reactores descontínuos sejam simples e versáteis, as suas desvantagens - que vão desde os elevados custos de mão de obra e fraca escalabilidade até aos riscos de segurança e qualidade inconsistente do produto - tornam-nos menos adequados para aplicações industriais modernas.Os reactores de fluxo contínuo, com a sua tecnologia avançada e eficiência superior, são cada vez mais preferidos para processos de produção em grande escala e de elevada procura.
Tabela de resumo:
Desvantagem | Descrição |
---|---|
Custos laborais elevados | Requer uma intervenção manual significativa, aumentando os custos operacionais. |
Fraca escalabilidade | Não é ideal para produção em grande escala devido aos frequentes ciclos de arranque e paragem. |
Longos tempos de inatividade | Tarefas não produtivas, como carregar e descarregar, reduzem a eficiência. |
Instrumentação limitada | A falta de monitorização e controlo em tempo real conduz a resultados inconsistentes. |
Qualidade inconsistente do produto | A variabilidade entre lotes afecta a uniformidade do produto. |
Riscos de segurança | Riscos de explosão durante o esvaziamento devido a reacções imprevisíveis. |
Limitado a reacções homogéneas | Menos eficaz para reacções complexas e multifásicas. |
Custos operacionais mais elevados | As ineficiências a longo prazo ultrapassam as poupanças de custos iniciais. |
Sem condições de estado estável | As condições de reação mudam ao longo do tempo, dificultando a otimização. |
Tecnologia desactualizada | Não possui os avanços observados nos reactores de fluxo contínuo modernos. |
Descubra como os reactores de fluxo contínuo podem resolver os seus desafios de produção- contacte-nos hoje !